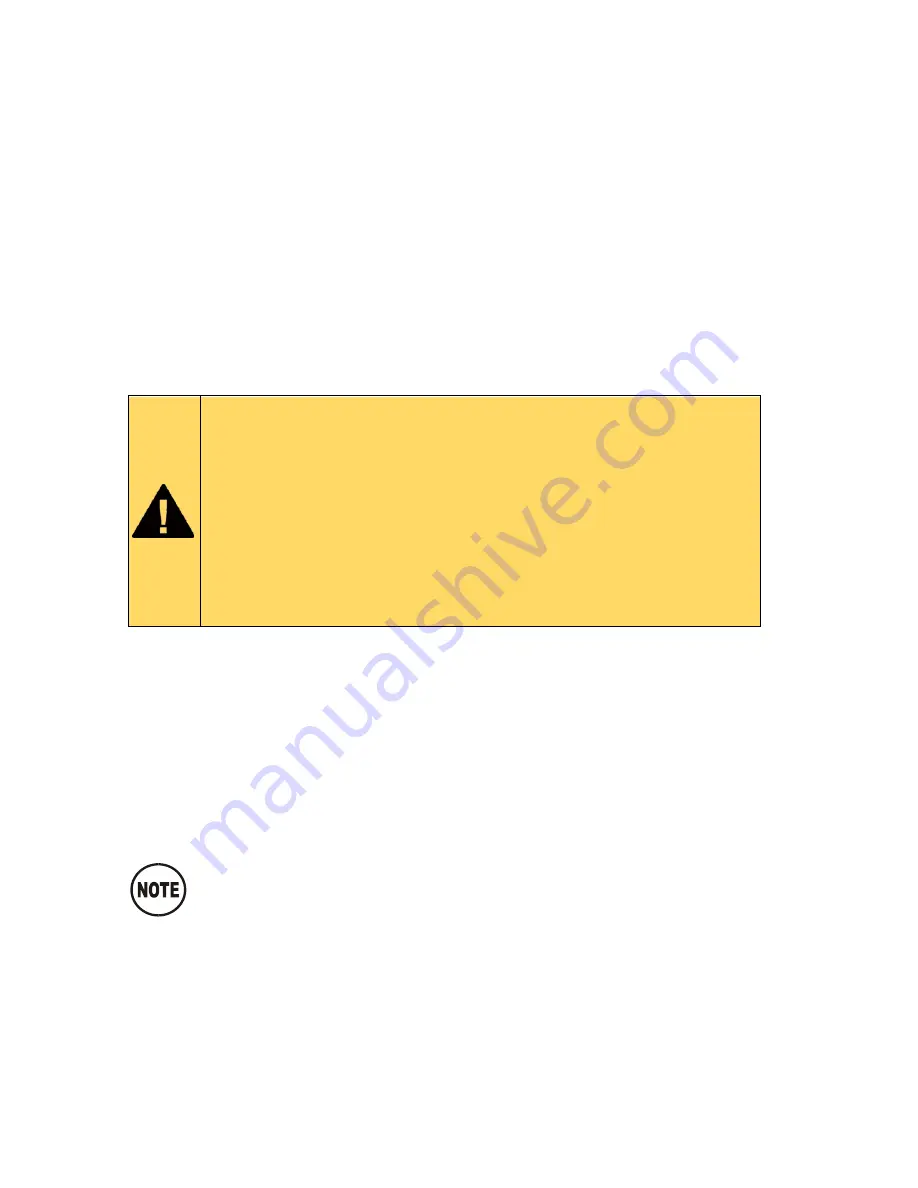
VMAC
– Vehicle Mounted Air Compressors
Toll Free:
1-888-241-2289
Fax: 1-250-740-3201
78
After Starting the Engine Checklist
Allow the vehicle to reach operating temperature.
Turn on the compressor. The compressor clutch should engage, and the
engine speed should increase to between 2,000 and 3,000 rpm in
response to the throttle control.
Allow the compressor to run for approximately 10 seconds.
Turn off the compressor.
Shut down the engine and check the compressor oil level. Add oil as
necessary to bring the level to the “FULL” line in the sight glass and check
for leaks.
Ensure any stored air is drained from the system.
Start the engine. Assistance may be required for the next steps.
The following tests confirm that the drive disable system is
working correctly. The drive disable system prevents the
VMAC throttle from increasing engine rpm unless the
transmission is in “PARK” and the park brake is engaged.
2 people are required to perform this safety test. 1 person
must remain in the driver seat and be prepared to actuate the
service (foot) brake if necessary.
The second person will actuate the compressor switch and
ball valve as necessary.
Install the VMAC Air Test Tool (P/N: A700052) with the 30 cfm (1/8 in)
orifice installed and the ball valve closed.
With the engine running and the vehicle in “PARK”, release the parking
brake.
Turn on the compressor and open the ball valve. The clutch should
engage, but engine speed should NOT increase.
Close the ball valve.
Turn off the compressor.
Reapply the park brake.
The steps marked with asterisks will be repeated.
*
With the engine running, Depress the service (foot) brake and shift the
transmission out of “PARK”.
*
Turn on the compressor and open the ball valve. The clutch should
engage, but engine speed should NOT increase.
*
Close the ball valve.
*
Turn off the compressor.
Summary of Contents for V300004
Page 1: ...Installation Manual for VMAC System V300004 2015 2016 Ford Transit 3 7 L Gas...
Page 2: ......
Page 90: ...This page intentionally left blank...
Page 91: ......
Page 92: ......