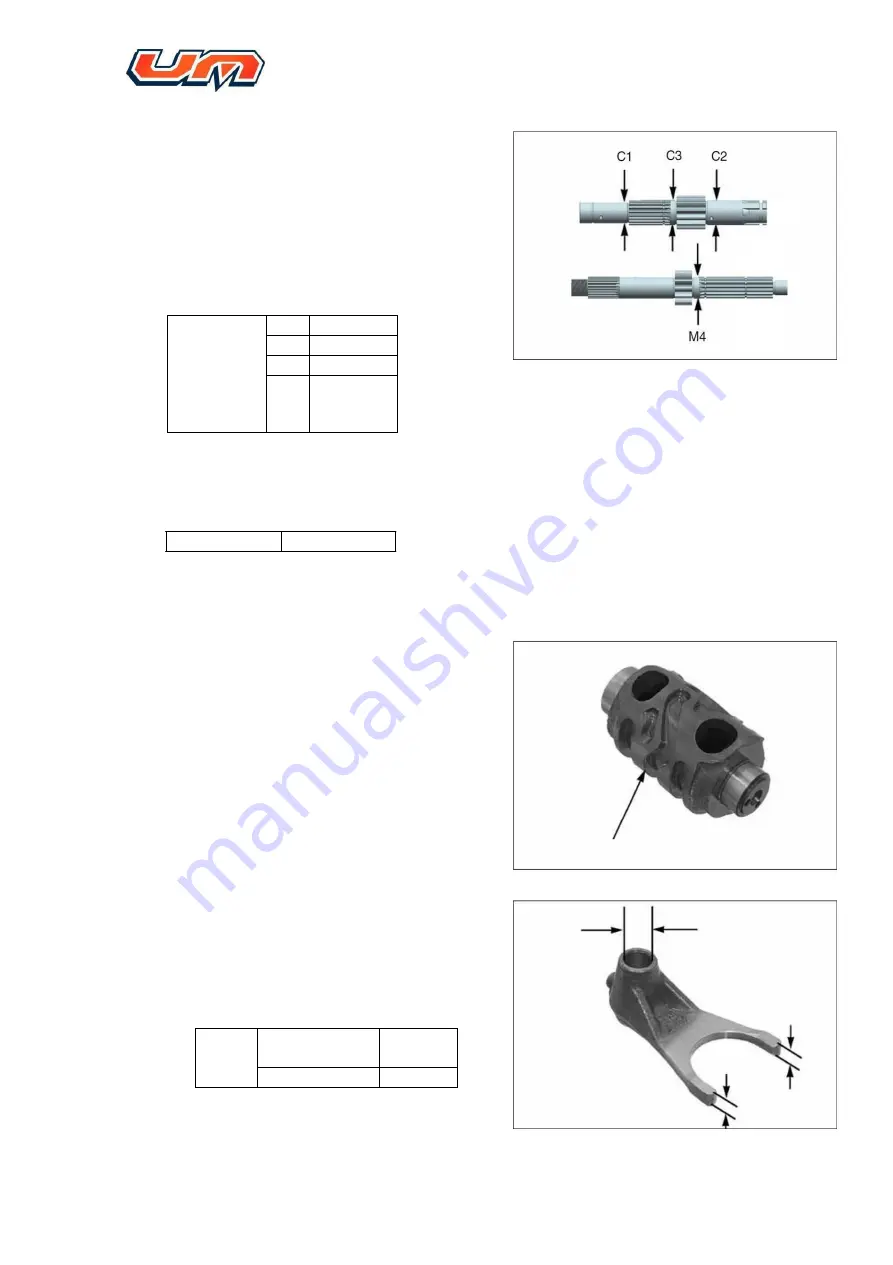
CBF 125 AIR COOLING ENGINE SERVICE MANUAL
XTREET 125 EFI
89
Check spline key and main and counter shaft for
abnormal wear and damage
Measure
diameter
of
shaft
at
gear-matching position.
Service limit
of outer
diameter of
main and
counter
shafts
M4
φ16.93mm
C1
φ16.93mm
C2
φ19.94mm
C3
φ19.95mm
Calculate fit clearance between gears and
shaft sleeve
Service limit
0.10mm
8.4.5.
Check of gearshift drum
8.4.5.1.
Check both ends of gearshift drum and
profiled groove for abnormal wear or
damage
8.4.5.2.
Check fork for abnormal wear and
deformation
Measure fork inner hole diameter and ear
thickness
Service
limit
Inner hole
diameter
10.07mm
Ear thickness
4.50mm
Summary of Contents for CBF 125
Page 1: ...CBF 125 ENGINE AIR COOLING SERVICE MANUAL AND EFI DIAGNOSTIC ...
Page 24: ...CBF 125 AIR COOLING ENGINE SERVICE MANUAL XTREET125EFI 24 4 1 Cylinder Head exploded view ...
Page 37: ...37 ...
Page 50: ...CBF 125 AIR COOLING ENGINE SERVICE MANUAL XTREET 125 EFI 50 ...
Page 83: ...CBF 125 AIR COOLING ENGINE SERVICE MANUAL XTREET 125 EFI 83 8 1 Crankcase exploded view ...