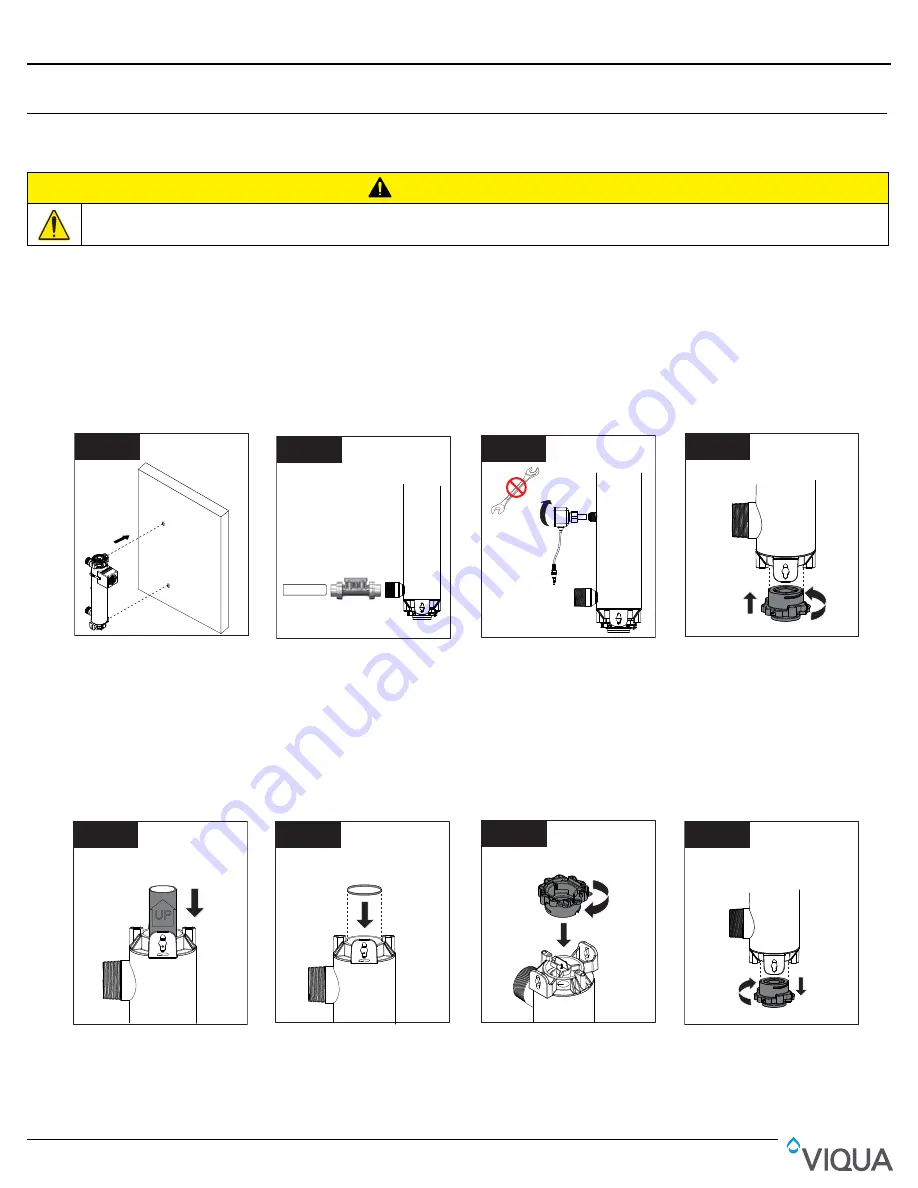
Installation
8
Section 3
Installation
3.1 Installing UV System
Prerequisites:
•
Determine appropriate indoor location of the controller and chamber, refer to
Section 2.1
.
•
Make sure that the controller is installed higher than the chamber and away from all water sources.
•
Ensure adequate clearance above chamber to allow for removal of the lamp and sleeve.
•
Make sure to turn off the main water supply.
•
Make all necessary plumbing connections refer to
Section 2.1
.
Procedure:
C A U T I O N
Electronic controller must be connected to a Ground Fault Protected Circuit (GFCI) receptacle.
1
•
Install the UV Chamber
vertically with the following
spacing on the wall using
screws.
•
PRO10: 18.5"
•
H, PRO20: 27.5"
•
K, PRO30/50: 37.5"
Note: Ensure chamber is
installed with green arrows
pointing upwards.
2
2
•
Connect Flow Meter Sensor
(PRO10,20,30 models only)
to chamber using 1¼” unions
supplied.
Note: LED must face up.
Ensure proper length of
straight pipe 1.0" Diameter at
inlet side of Flow Meter
Sensor and use a 1¼” to 1"
Reducing Coupler (not
supplied).
3
•
Install the sensor to the UV
system (for PRO models
only).
Note: DO NOT use wrench to
tighten the sensor.
4
2
1
•
Connect the sleeve bolt at the
bottom of the sleeve
assembly. Ensure sleeve bolt
is rotated full 1/4 turn until
positive stop.
5
•
Insert sleeve with arrow
pointing up.
Note: DO NOT rotate sleeve
and touch glass with bare
hands.
6
•
Wet O-ring with water then
place over top end of sleeve.
7
2
1
•
Connect the sleeve bolt to the
top of the sleeve assembly.
Ensure sleeve bolt is rotated
full 1/4 turn until positive stop.
8
1
2
•
Remove the sleeve bolt at the
bottom of the sleeve
assembly.