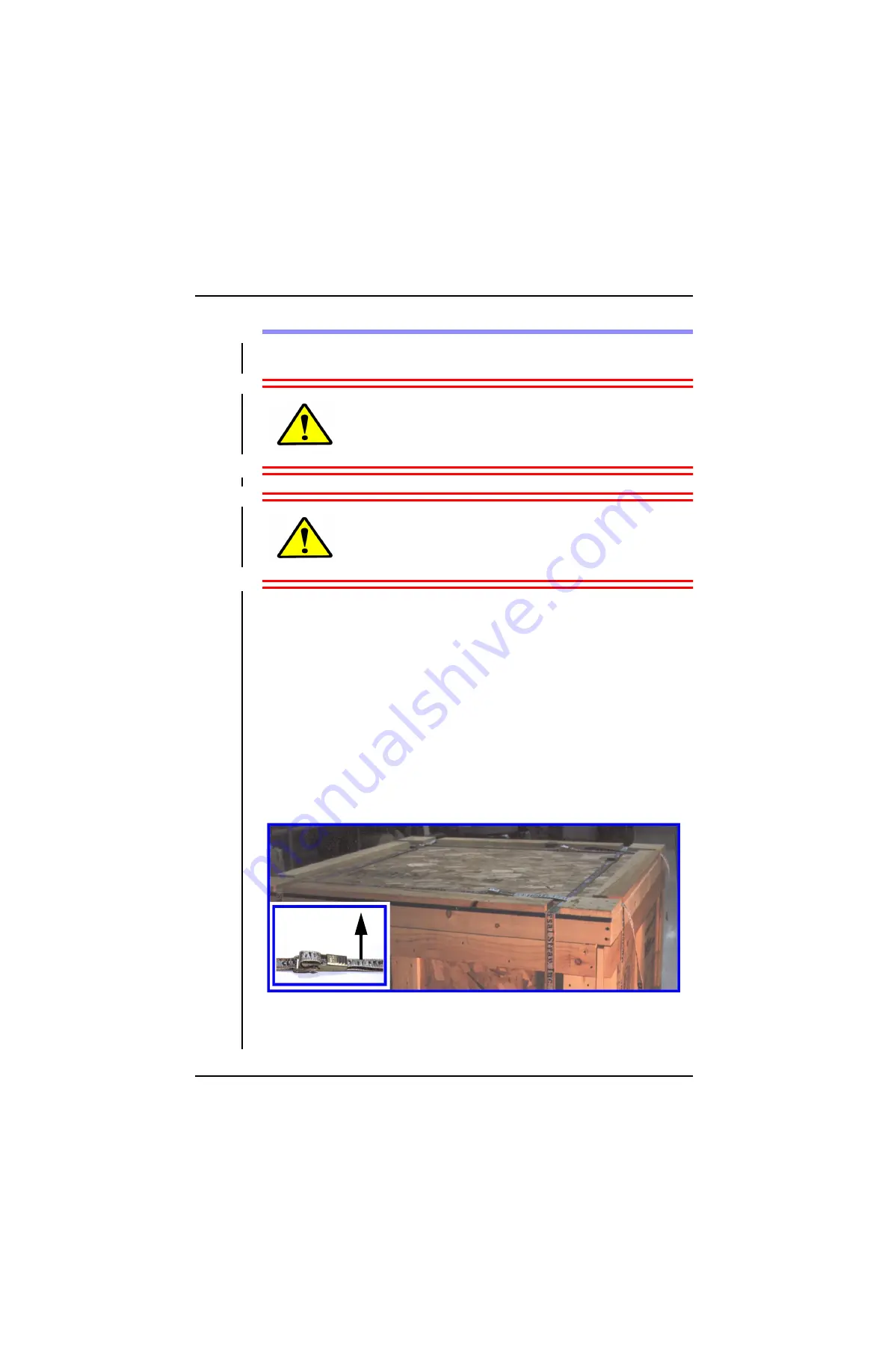
SP-2000/X-Y
Installation
3-4
User Manual
Removing The SP-2000/X-Y From Its Crate
CAUTION: Do not try to push the pedestal off the base of
the crate and down the ramp. You may cause serious electri-
cal and/or mechanical damage.
CAUTION: At least two people are needed to remove the
pedestal from the crate.
As shipped from the factory, the on board batteries of the SP-2000/X-Y are fully
charged. Therefore, unless the dolly is left crated for an extremely long time, it
can be driven off the skid under battery power using the ramp supplied. If you
cannot drive the dolly under its own battery power, the alternate procedure
described below will require the temporary use of the AC power supply and
power/data cable.
Uncrating The Pedestal
1.
The shipping crate is re-usable and should be saved for repacking the ped-
estal or should be shipped back to Vinten. Make sure that you retain the
sides, top, ramp, interior brace and the four straps.
2.
Release the four straps that hold the crate together by pulling up on the
latch on each buckle. Remove the straps.
3.
Using two or more people, lift the top of the crate and set it aside.
Pull Up
To Release
Summary of Contents for AutoCam SP-2000/X-Y
Page 10: ...Table Of Contents x This page left blank intentionally ...
Page 11: ...User Manual 1 1 1 Safety Introduction ...
Page 21: ...SP 2000 X Y Safety Introduction User Manual 1 11 This page left blank intentionally ...
Page 28: ...SP 2000 X Y Safety Introduction 1 18 User Manual This page left blank intentionally ...
Page 29: ...User Manual 2 1 2 Operation ...
Page 40: ...SP 2000 X Y Operation 2 12 User Manual This page left blank intentionally ...
Page 41: ...User Manual 3 1 3 Installation ...
Page 57: ...SP 2000 X Y Installation User Manual 3 17 This page left blank intentionally ...
Page 63: ...SP 2000 X Y Installation User Manual 3 23 This page left blank intentionally ...
Page 67: ...User Manual 4 1 4 Maintenance And Repair ...
Page 71: ...SP 2000 X Y Maintenance And Repair User Manual 4 5 This page left blank intentionally ...
Page 79: ...SP 2000 X Y Maintenance And Repair User Manual 4 13 This page left blank intentionally ...
Page 81: ...SP 2000 X Y Maintenance And Repair User Manual 4 15 North Sensors West Sensors ...
Page 85: ...SP 2000 X Y Maintenance And Repair User Manual 4 19 This page left blank intentionally ...
Page 91: ...SP 2000 X Y Maintenance And Repair User Manual 4 25 This page left blank intentionally ...
Page 95: ...SP 2000 X Y Maintenance And Repair User Manual 4 29 This page left blank intentionally ...
Page 106: ...SP 2000 X Y Index IV This page left blank intentionally ...