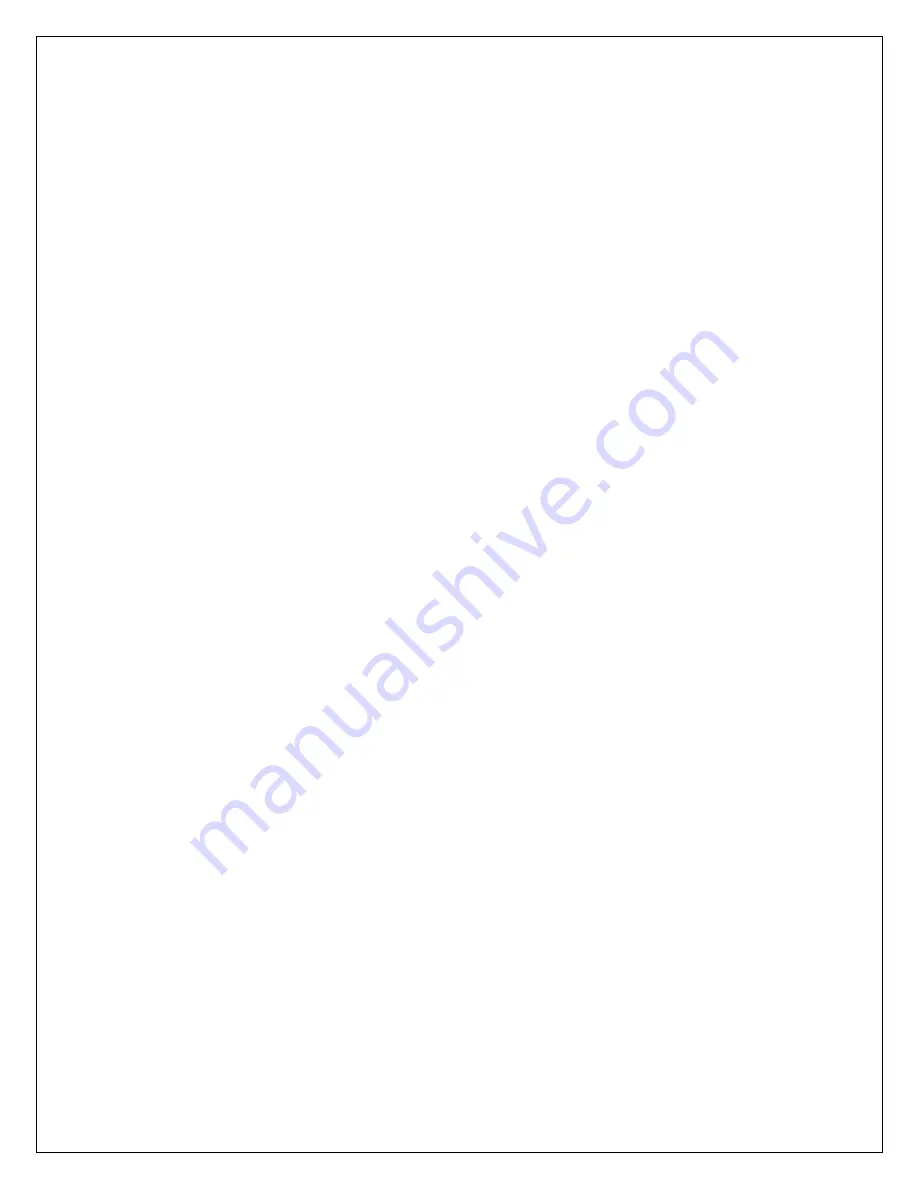
-3-
Cellar Construction Guide
This is only a guide and shall be considered as the minimum requirements.
All interior walls, ceilings and floors shall have a vapor barrier and a minimum of
R13 insulation. All exterior walls and ceiling shall have a vapor barrier and a
minimum of R19 insulation. The vapor barrier shall be installed on the warm side
of insulation. All joints, door frames, electrical outlets or switches and any pipes
or vents that go through the cellar shall be sealed to prevent air and moisture
leaking into the cellar. Concrete, rock, and brick are not insulations or vapor
barriers. Doors shall be of a minimum size, insulated to at least R13 and tightly
sealed with high quality weather stripping. Be sure to seal the bottom of the door
and fill gap between the
door’s frame and wall before installing the cap molding.
In order to maintain 55 °F in the wine cellar, the ambient temperature surrounding
the cellar shall not exceed the temperature of the cellar by more than 25 °F.
No cellar walls shall receive direct sun or strong wind.
Lighting shall be of low wattage, with a timer to insure lights are not left on when
the cellar is not occupied.
The cooling system will not be able to maintain the proper temperature if fresh
moisture-laden air is constantly being introduced to the cellar. Symptoms of this
condition are; cooling unit runs all the time with only a slight reduction in
temperature and/or water overflows from the cooling unit. Because of the
temperature difference between the inside and outside, very small cracks can
allow large amounts of outside air to enter into the cellar. Please be aware that
moisture can pass through solid concrete, paint and wood. Often a newly
constructed cellar contains fresh wood, paint, concrete and other building
materials. These materials contain large amounts of moisture. When placed into
operation in this type of environment, the system will work harder to remove this
extra moisture resulting in increased
“run” time.