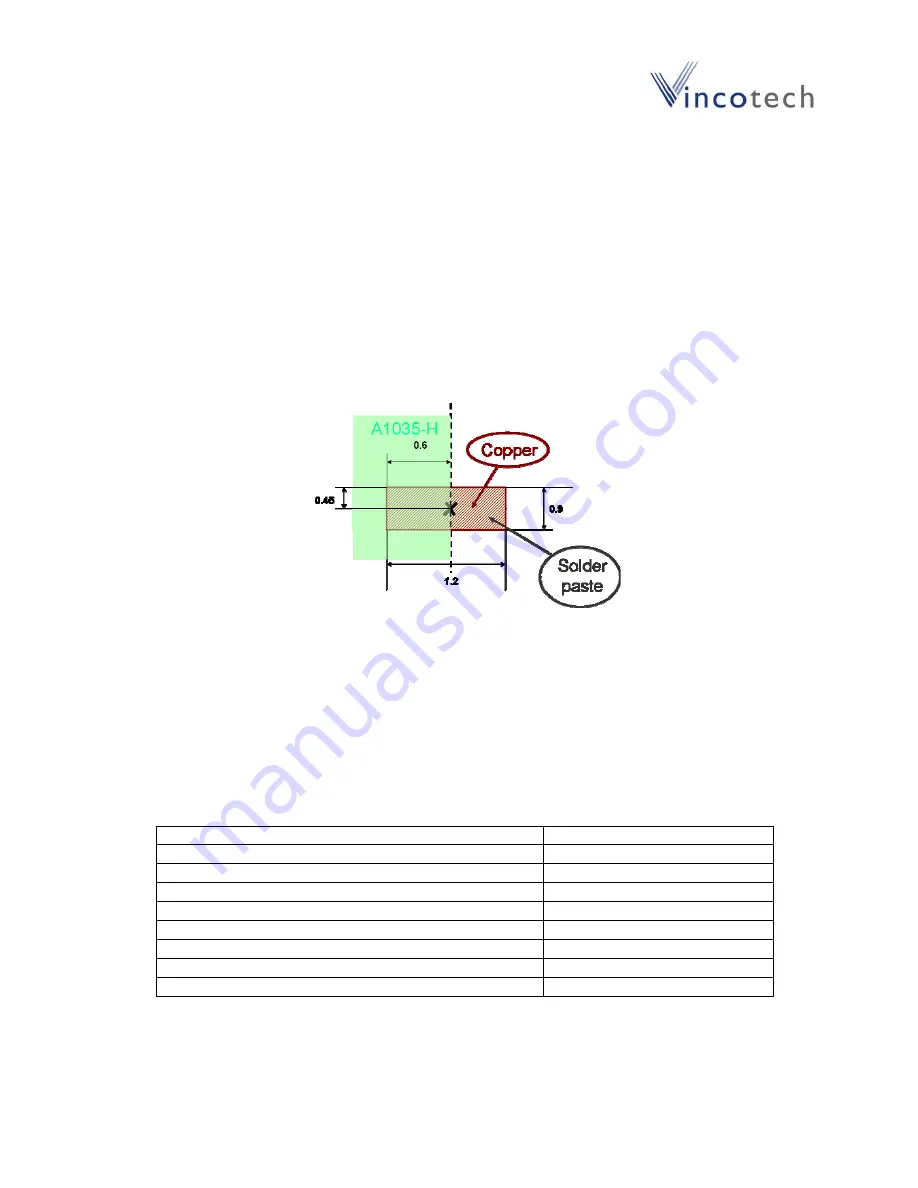
7 Mounting
This chapter describes the suggested mounting process for the A1035-H receiver
modules. In a RoHS compliant product with a RoHS compliant process it is recom-
mended to use chemical tin as the counter-part to the module’s pins. This will guar-
antee highest resistance against shocks.
7.1 Proposed Footprint for Soldering
The following proposal of a footprint for soldering is assuming a stencil thickness of
150µm.
³
marks the center of the through holes.
Figure 11: Soldering footprint proposal A1035-H
Please note that copper and solder paste footprint are identical. The final footprint
has to be evaluated and qualified by the manufacturer according to the specific
processes.
7.2 Recommended Profile for Reflow Soldering
Typical values for reflow soldering of the module in convection or IR/convection ov-
ens are as follows (according to IPC/JEDEC J-STD-020D):
Parameter Value
Peak temperature (RoHS compliant process)
245°C
Average ramp up rate to peak (217°C to Peak)
3°C / second max.
Preheat temperature
min=150°C; max=200°C
Ramp up time from min. to max. preheat temperature 60 … 120 seconds
Temperature maintained above 217°C
60 … 150 seconds
Time within 5°C of actual peak temperature
30 seconds
Ramp down rate
6°C / second max.
Time 25°C to peak temperature
8 minutes max.
Table 8: Reflow soldering profile A1035-H
V1.5 – Dec-09
User’s Manual
Page 22 of 37