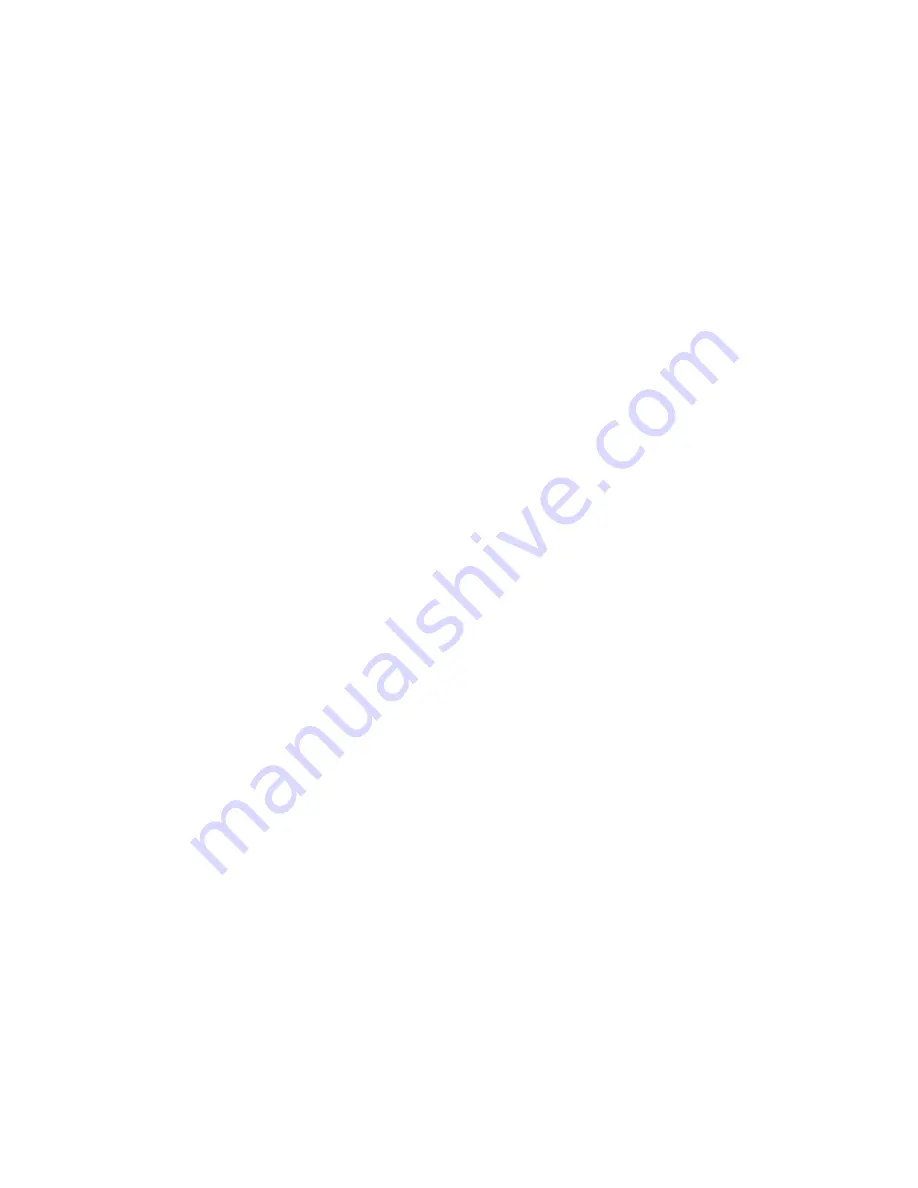
49
7. With the CS-1’s switch in the “OFF” position turn on the power supply to the
unit. Turn the “Off-On” switch to “ON”.
8. Switch the “Man-O-AUTO” switch on the unit control panel to “Man”. Liquid
will begin to fill the selected system.
9. As the system fills, monitor the system vent/bleed valves. Close each valve
when liquid leaks from it.
10. When the liquid leaks from the uppermost vent/bleed valve, close the vent
valve. The system pressure switch will close that system’s solenoid valve.
The pump pressure switch will turn the pump off.
11. If another system is to be filled, turn the “Man-O-AUTO” switch to OFF and
select the next system using switches A and B.
12. Turn the “Man-O-AUTO” switch to “Man” and repeat steps 8 through 10.
13. After filling all systems and the CS-1 tank, close the supply isolation valve.
14. All air must be out of the system before switching the unit to maintenance
mode. Follow the system manufacturer’s recommendations to ensure all air
is removed.
16.0 SYSTEM AND SOLUTION TEST AND MAINTENANCE
Field mixing of propylene glycol and site water is strictly prohibited, as the control of the
mixture cannot be assured. Improper field mixing of solution can result in reduced
capability to prevent freezing or to control a fire. Firefighter Eliminator F is already
premixed and ready to use.
Filling the System
In the main drain line between the valve and primary check valve inlet, a tee is provided
with a 1” NPT connection for supply and maintenance of the antifreeze solution to the
system above the check valve. A suitable portable pump can be utilized to fill the system
to the static water pressure. (The CS-1 pump can be used for filling the system initially at
15 GPM (56 l/min) to 100 ft. head pressure or system static pressure. However, it is a
less efficient pump for filling the system because of the duration of time required to do
so. The CS-1 pump is to be utilized to bring the solution to maintenance pressure
[recommended 50 PSI (344 kPa)] and is designed to maintain supervisory pressure
once the system is initially filled. When filling the system with antifreeze solution, all air
must be bled from the system (as described in data page 45 a-j) in order to make final
and maintained antifreeze solution pressure non-compressible.
16.1
Testing the Solution
Antifreeze solution shall be checked quarterly (for gridded systems), or semi-
annually (for tree type configurations) with a refractometer to detect the
concentration of antifreeze solution and effectiveness against freezing. Sampling
shall be taken from multiple points within the freezer system (refer to the
instructions on data pages 45 e and 45 i for fluid sampling). When draining
sample antifreeze solution from the system, be sure to shut off the system control
valve directly upstream of the deluge valve so that water doesn’t enter the
system. After the CS-1 pump has restored the antifreeze solution pressure,
ensure that the water supply control valve is returned to the fully open position
once fluid sampling is completed. Multiple propylene glycol/water solution test
Summary of Contents for ESFR
Page 5: ...5 Figure 1 Straight Through Configuration...
Page 6: ...6 Figure 2 Angle Style Configuration...
Page 10: ...10...
Page 35: ...35...