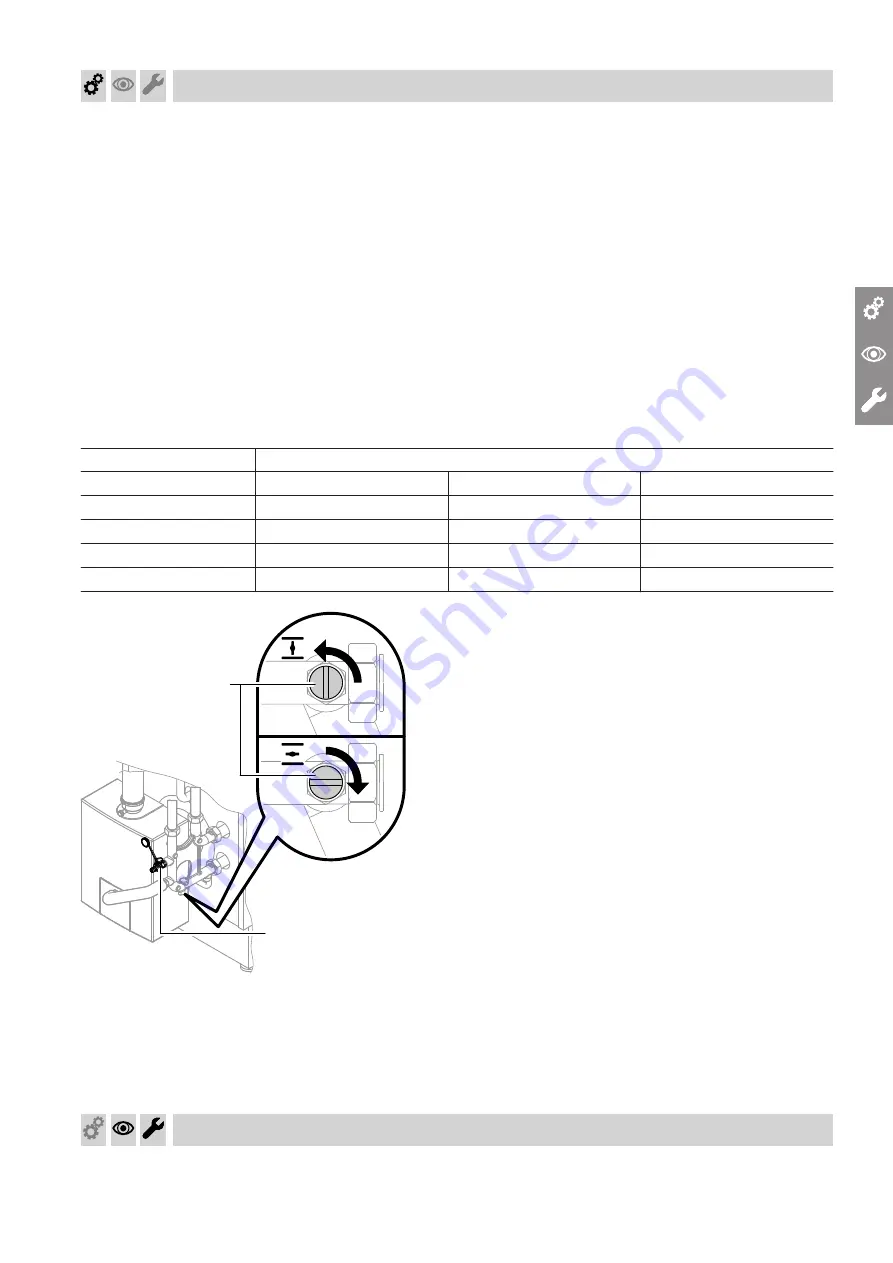
9
Fill water
According to EN 1717 with DIN 1988-100, as a heat
transfer medium for DHW heating, the heating water
must meet fluid category ≤ 3. This requirement is met if
water of potable quality is used as heating water. For
example, if additives are used, the additive manufac-
turer must specify which category the treated heating
water comes under.
!
Please note
Unsuitable fill water increases the level of
deposits and corrosion and may lead to appli-
ance damage.
■
Flush the heating system thoroughly before
filling.
■
Only use fill water of potable water quality.
■
Special antifreeze suitable for heating systems
can be added to the fill water. The antifreeze
manufacturer must verify its suitability.
■
Fill and top-up water with a water hardness in
excess of the following values must be soft-
ened, e.g. with a small softening system for
heating water.
Total permissible hardness of the fill and top-up water
Total heating output
Specific system volume
kW
< 20 l/kW
≥
20 l/kW to < 50 l/kW
≥
50 l/kW
≤
50
≤
3.0 mol/m
3
(16.8 °dH)
≤
2.0 mol/m
3
(11.2 °dH)
< 0.02 mol/m
3
(0.11 °dH)
>
50 to
≤
200
≤
2.0 mol/m
3
(11.2 °dH)
≤
1.5 mol/m
3
(8.4 °dH)
< 0.02 mol/m
3
(0.11 °dH)
>
200 to
≤
600
≤
1.5 mol/m
3
(8.4 °dH)
≤
0.02 mol/m
3
(0.11 °dH)
< 0.02 mol/m
3
(0.11 °dH)
>
600
< 0.02 mol/m
3
(0.11 °dH)
< 0.02 mol/m
3
(0.11 °dH)
< 0.02 mol/m
3
(0.11 °dH)
A
B
Fig. 1
1.
Close shut-off valve
B
in the return line.
2.
If using a top-mounted Divicon (accessories):
Set the mixer lever to "OPEN" (red).
3.
Fill the system via fill valve
A
on the heating water
return until it is fully vented.
4.
Reopen shut-off valve
B
.
Shutting down the system
Commissioning, inspection, maintenance
Filling the heating system on the heating water side
5671704