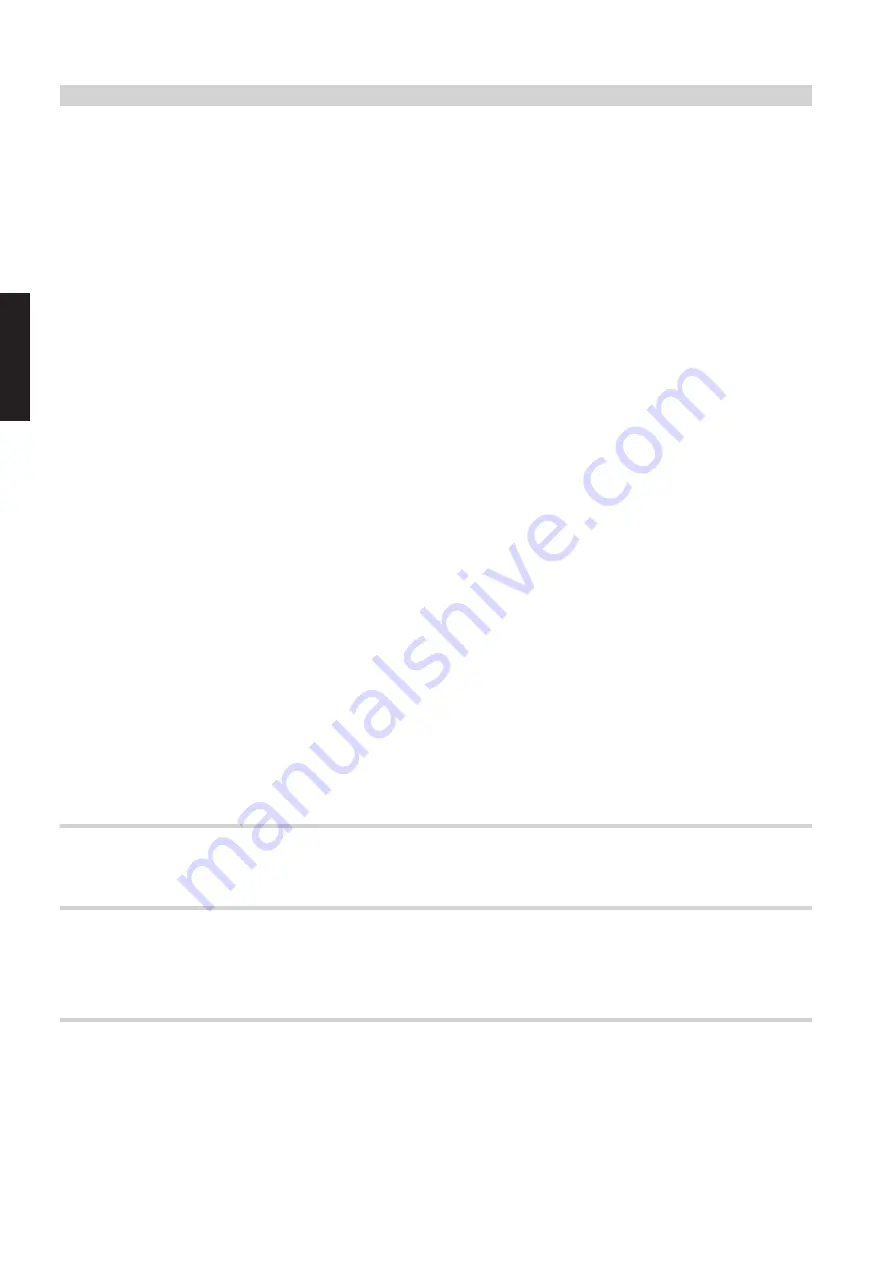
Burn-back protection device (RSE)
Note
See page 40.
Additional "material transport burn-back protection" depends on the
respective requirements (location, size of the fuel store, material,
pressure, regulations) and is a separate item from the standard
delivery ordered.
Available burn-back protection devices (RSE):
■ Shut-off gate valve
■ Rotary lock valve
Available extensions for burn-back protection devices (RSE):
■ Dual rotary lock valve
■ Drop chute
Note
In wood processing operations, 2 burn-back protection devices con-
nected in series are required.
For example 2 rotary lock valves or 1 rotary lock valve in combina-
tion with a shut-off gate valve.
Note
Ensure a sufficient minimum distance between the RSE and the fuel
charging system.
Shut-off gate valve
A shut-off gate valve is permitted in all non-pressurised fuel stores.
According to TRVB H-118 (test certificate BV 2979/89), it is deemed
a suitable burn-back protection device.
Rotary lock valve
Due to the pressure load, at least one rotary lock valve is required to
reduce pressure between the fuel store and the boiler if wood rem-
nants are blown into fuel storage rooms by fans. The rotary lock
valve is suitable for reducing pressure. It is deemed a suitable burn-
back protection device both in EN 303-5 and TRVB H-118 (test cer-
tificate BV 2979/89).
Dual rotary lock valve with pressure compensation
If, due to special circumstances, extremely high overpressure can be
expected in the fuel store, then in accordance with the relevant
project plan, 2 rotary lock valves with a pressure compensation line
to the open air must be installed in the material transport path.
The maximum pressures to be expected must be confirmed by the
supplier of the chip extraction system. Leaks may occur in the rotary
lock valve under the discharge system as a result of wear on the
sealing elements or due to larger pieces of wood that cannot be
transported. Such leaks may allow the back flow of low temperature
carbonisation gases from the combustion system into the fuel store.
A flue gas alarm must be installed between the rotary lock valve and
the discharge system which, when responding, switches off the sys-
tem causing the negative pressure.
■ Max. permissible positive pressure in the fuel store: + 1200 Pa
■ Max. permissible negative pressure in the fuel store: + 0 Pa
Drop chute
A drop chute may be required in order to provide a sufficient dis-
tance between the RSE and the charging device. This prevents com-
bustible material from being conveyed back (possibly by embers or
sparks).
Note
The drop chute must be used in conjunction with an additional RSE.
The design (diameter, profile) of the drop chute is matched to the rel-
evant project at the factory.
9.9 Fire safety
The fire safety regulations for wood combustion systems vary from
country to country.
The regulations applicable to the specific installation location must
be observed.
Fuel store fire safety
The measures required for this (such as for example, temperature
monitoring devices in the fuel store/hopper ("TÜB"); manually actu-
ated extinguishing device ("HLE")) are not part of the Viessmann
Holzheiztechnik GmbH standard delivery.
Note
In this regard, the conditions of the local planning office must be met
by the operator.
9.10 Commissioning
Initial commissioning of a newly installed system may only be carried
out by Viessmann or another heating contractor trained and author-
ised by Viessmann. Prior to commissioning, the system must be fil-
led with water, fuel must be provided for commissioning and the
installation must be checked.
Design information
(cont.)
94
Viesmann
VITOFLEX 300-UF
9
5682428