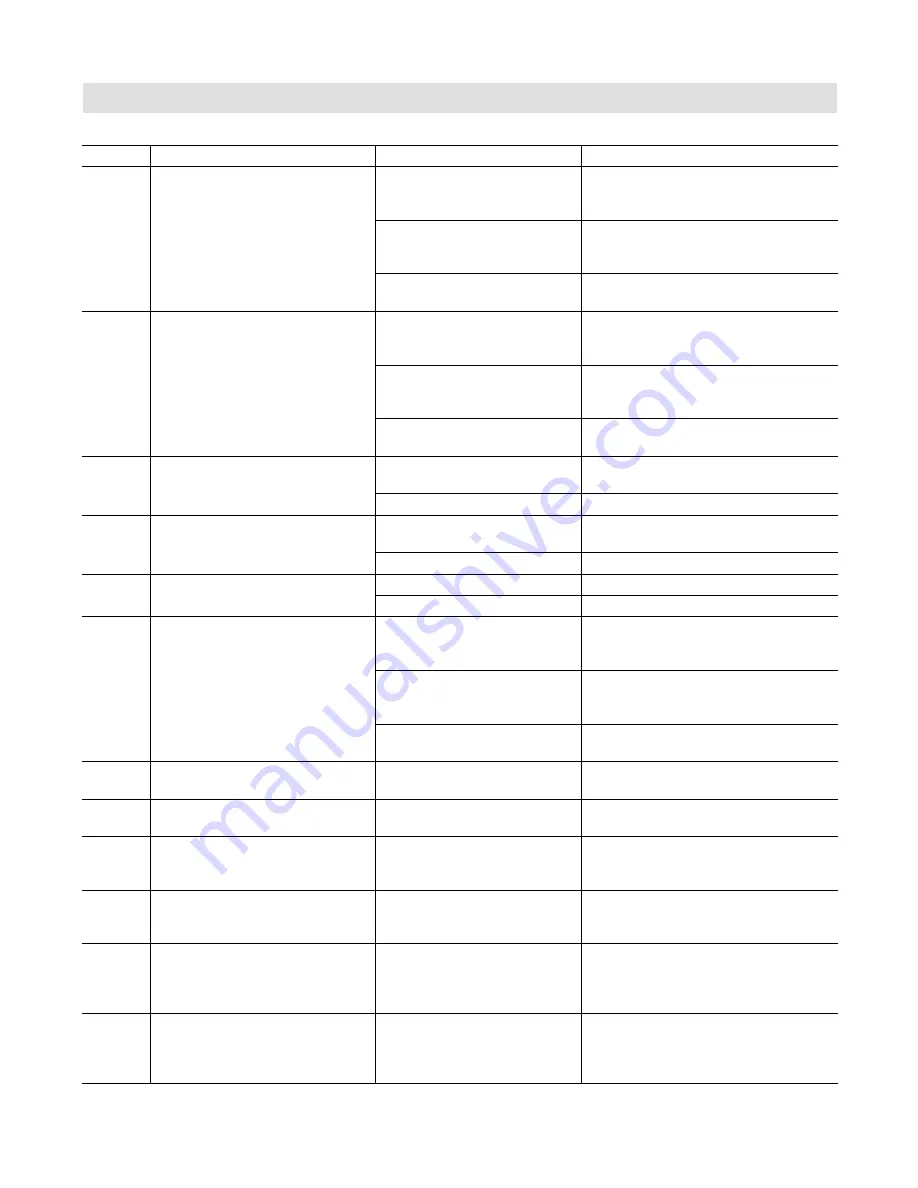
20
5797 342 - 01
Vitoflex 300-RF Service & Maintenance
Fault Message
(continued)
Troubleshooting
No.
Fault message
Cause
Remedy
012
Fault: Temperature level,
hydraulics, push floor
Loss of oil at the hydraulic unit - Check the fittings, lines and cylinders
for leaks
- Top up the oil
Pressure switch is incorrectly
set or faulty
- Replace pressure switch
- Readjust setting for changeover
pressure at pressure switch
Room temperature is too high
- Reduce room temperature
- Install oil cooler
013
Fault: Temperature level,
hydraulics, silo cover
Loss of oil at the hydraulic unit - Check the fittings, lines and cylinders
for leaks
- Top up the oil
Pressure switch is incorrectly
set or faulty
- Replace pressure switch
- Readjust setting for changeover
pressure at pressure switch
Room temperature is too high
- Reduce room temperature
- Install oil cooler
014
Fault: Reversal, discharge
Motor is overloaded due to
blockage (foreign body)
Remove foreign body
Bearing damage
Check for ease of operation
015
Fault: Reversal, conveyor device
Motor is overloaded due to
blockage (foreign body)
Remove foreign body
Bearing damage
Check for ease of operation
016
Fault: Motor protection,
hydraulics, container X
Electrical fault on drive motor
Consult a qualified electrician
Bearing damage
Replace bearing
017
Fault: Temperature level,
hydraulics, container X
Loss of oil at the hydraulic unit - Check the fittings, lines and cylinders
for leaks
- Top up the oil
Pressure switch is incorrectly
set or faulty
- Replace pressure switch
- Readjust setting for changeover
pressure at pressure switch
Room temperature is too high
- Reduce room temperature
- Install oil cooler
018
Fault: Container X, cover closed
Material cover of container is
not in end position “open”
Open container cover
019
Fault: No container available
All containers are empty or in
a fault state
Provide container with fuel
020
Fault: Changeover unit, time
monitoring
Changeover unit was running
for more than 5 minutes
- Check limit switch
- Check the setting for the
changeover unit
021
Fault: External charging
External charging reports a fault Check and remedy the fault in
accordance with message on charging
controller
022
Fault: Thermal contact, boiler pump - Electrical fault or motor
overloaded
- No water or too little water
in the system
- Check system pressure
- Consult a qualified electrician
023
Fault: CO CO
2
External detector reports CO
or CO
2
emission into the boiler
room
- Immediately leave the boiler
room and ensure ventilation
- Consult Viessmann Technical
Service