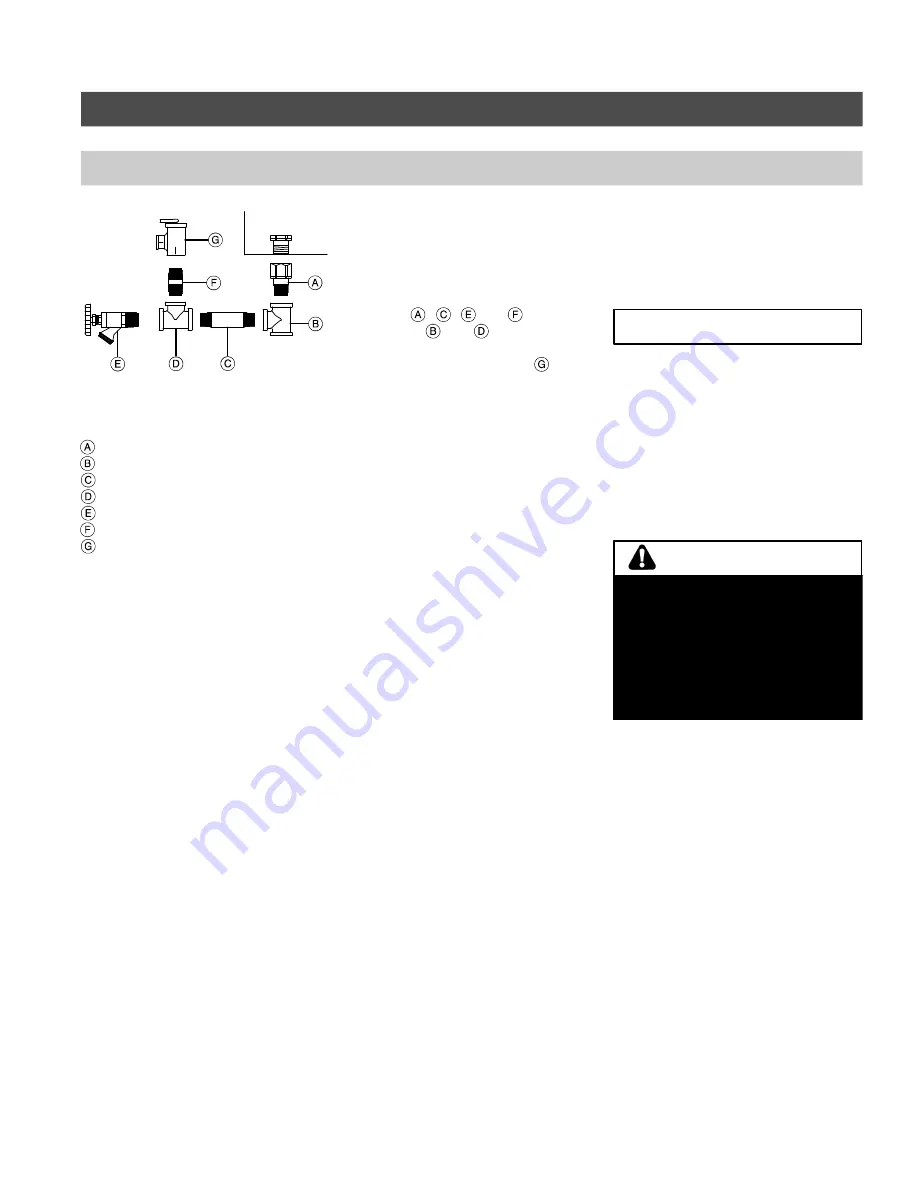
Boiler Connections
25
Safety Connections and Pressure Testing
Installing boiler safety devices
Legend
Extension, 2¼”x ¾”
Tee, ¾”
Brass nipple, length 3” x ¾”
Tee, ¾”
Drain valve connection, ¾”
Brass nipple, length 2” x ¾”
Pressure relief valve, ¾” NPT
1.
Remove loosely pre-assembled
combination pressure relief valve and
drain valve assembly.
2.
Apply sufficient amount of pipe
sealant to both ends of all pipe
fittings
,
,
and
, and install
onto tees
and
.
3.
Install pressure relief valve
and
tighten.
4.
Install discharge pipe on pressure
relief valve in such a way that...
H
the end of the pipe is not threaded.
H
the pressure relief discharge pipe
extends to a floor drain and ends
approximately 6” / 150 mm above
the drain.
Ensure that...
H
there is no shutoff valve
installed in the discharge pipe.
H
discharge pipe diameter is not
reduced.
H
discharge is not piped to
outdoors.
Minimum connection diameters:
Pressure relief valve
¾“
. . . . . . . . . . . . . . . . . . . . . . . . . . . .
Discharge pipe
¾“
. . . . . . . . . . . . . . . . . . . . . . . . . . . . . . . . . . . . . . . .
Piping to precharged
expansion tank
¾“
. . . . . . . . . . . . . . . . . . . . . . . . . . . . . . . . . . . . . .
Install the (approved) factory supplied
pressure relief valve.
Removal of air from the system must
occur via use of air vent(s) in the
system supply. To ensure the boiler
can be purged of all air, ensure
supply/return water lines do not
contain restrictive piping where air
could be trapped.
Low water cut-off
A low water cut-off may be required by
local codes. If boiler is installed above
radiation level, a low water cut-off
device of approved type (field supplied)
must be installed in all instances. Do
not install an isolation valve between
boiler and low water cut-off (see
subsection entitled “Boiler with low
water cut-off” on page 39 in these
instructions).
5
3
6
9
2
9
7
v
1
.6
Fig. 21
IMPORTANT
Do not install an isolation valve
between boiler and pressure relief
valve.
The discharge pipe for the pressure
relief valve must be oriented to
prevent scalding of attendants.
Pipe pressure relief valve discharge
pipe close to floor drain. Never pipe
discharge pipe to the outdoors.
WARNING