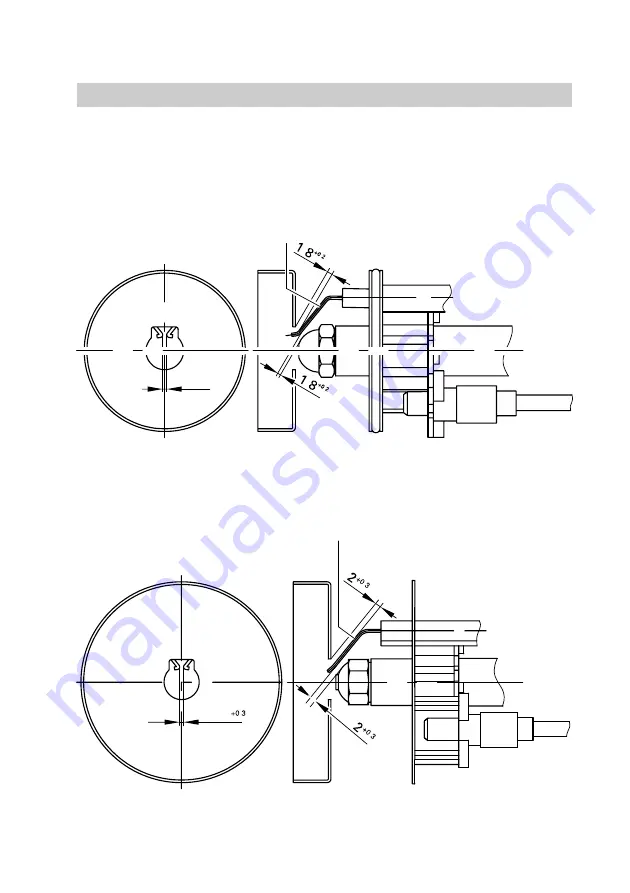
13
Initial start−up, inspection and maintenance
Further details regarding the individual steps
(cont.)
Checking and, if required, adjusting ignition electrodes
Check ignition electrodes
A
for
wear, contamination and size (see
fig.) and replace if necessary.
5692589GB
+0.3
1.5
A
15 to 33kW
.
.
.
.
40 to 63kW
1.5
A
.
.
.
Summary of Contents for VEK
Page 31: ...31 Parts list Parts list cont 5692 589 GB 002 001 017 005 049 009...
Page 33: ...33 Parts list Parts list cont 5692 589 GB 047 020 041 021 040 80o 80p 034 033 046 039 038...
Page 37: ...37 Appendix 5692 589 GB...
Page 39: ...39 Appendix Maint service Maint service Maint service Maint service 5692 589 GB...
Page 41: ...41 Appendix Maint service Maint service Maint service Maint service 5692 589 GB...
Page 42: ...42 Appendix 5692 589 GB...