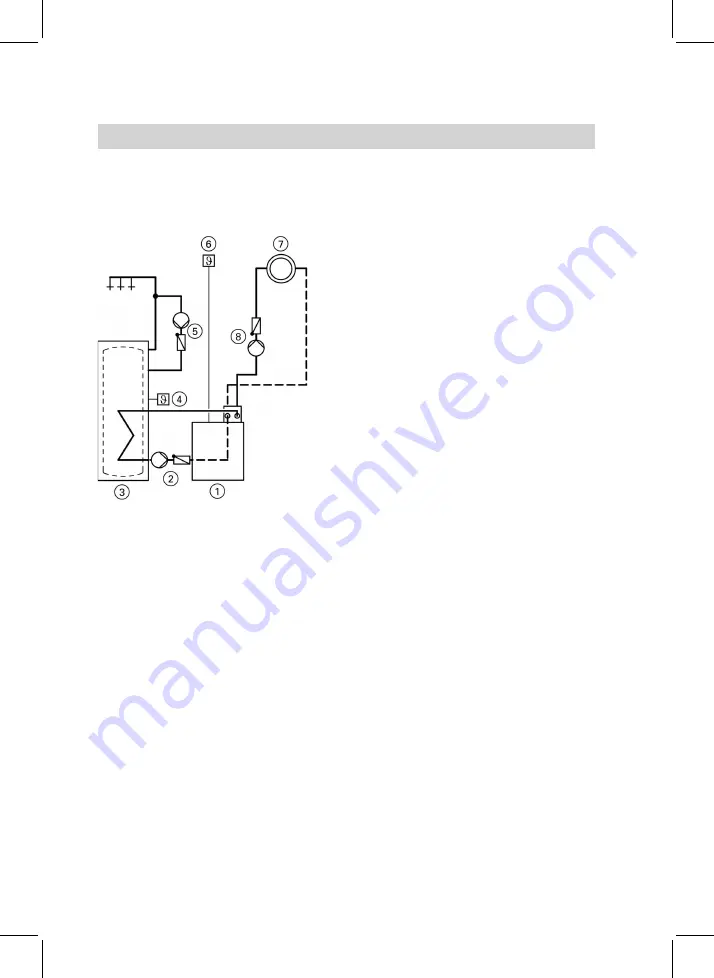
System version 1
One heating circuit without mixer A1 (with/without DHW heating)
1
Vitoladens 300-C
2
Cylinder primary pump
3
DHW cylinder
4
Cylinder temperature sensor
5
DHW circulation pump
6
Outside temperature sensor
7
Heating circuit without mixer A1
8
Heating circuit pump A1
Further details regarding the individual steps
(cont.)
28
Commissioning, inspection, maintenance
5692
745
GB
Summary of Contents for VC3
Page 96: ...Parts lists cont 96 Parts lists 5692 745 GB ...
Page 97: ...Parts lists cont 97 Parts lists 5692 745 GB ...
Page 98: ...Parts lists cont 98 Parts lists 5692 745 GB ...
Page 99: ...Parts lists cont 99 Parts lists 5692 745 GB ...
Page 100: ...Parts lists cont 100 Parts lists 5692 745 GB ...
Page 101: ...Parts lists cont 101 Parts lists 5692 745 GB ...
Page 109: ...109 5692 745 GB ...
Page 110: ...110 5692 745 GB ...
Page 111: ...111 5692 745 GB ...