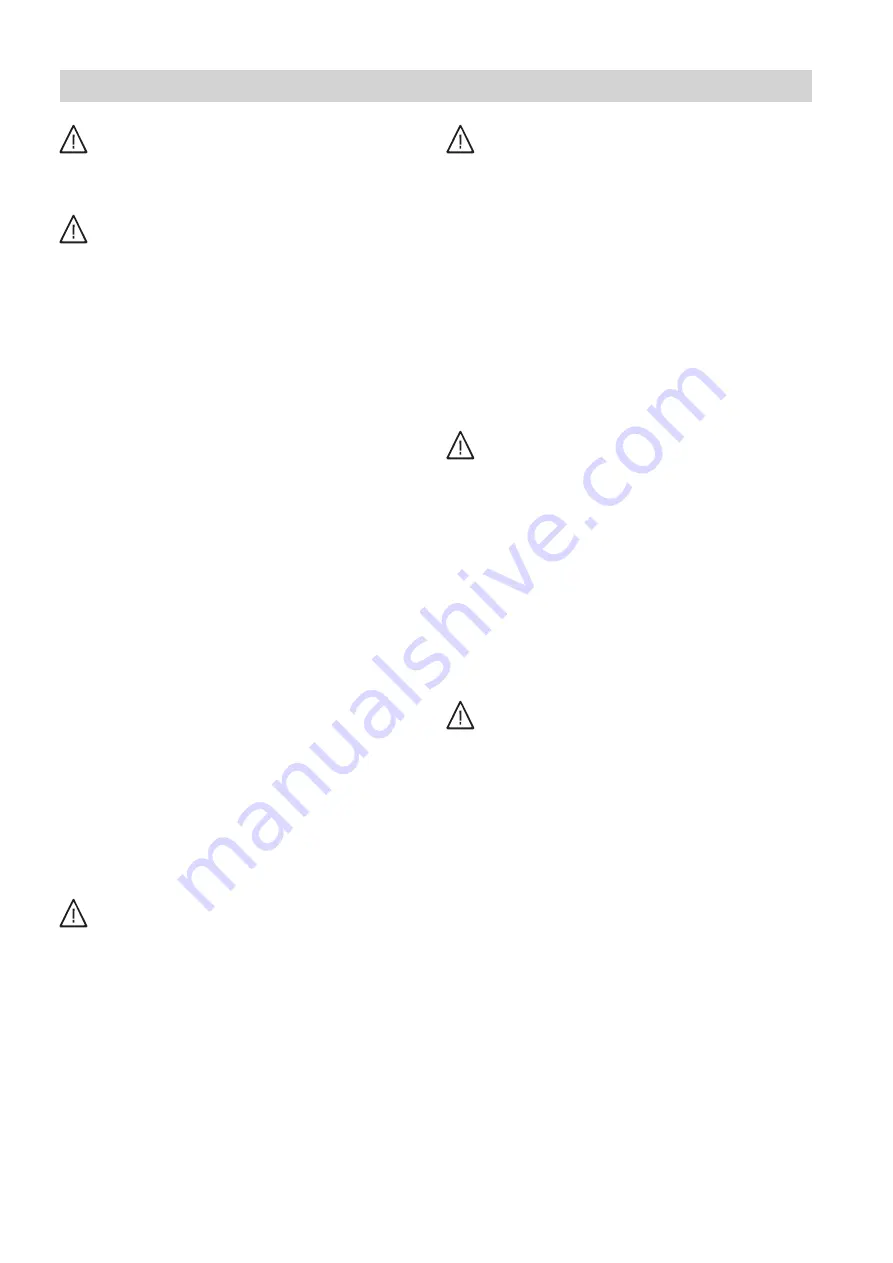
2
Please follow these safety instructions closely to
prevent accidents and material losses.
Safety instructions explained
Danger
This symbol warns against the risk of injury.
!
Please note
This symbol warns against the risk of material
losses and environmental pollution.
Note
Details identified by the word "Note" contain additional
information.
Target group
These instructions are exclusively intended for quali-
fied contractors.
■
Work on electrical equipment must only be carried
out by a qualified electrician.
■
The system must be commissioned by the system
installer or a qualified person authorised by the
installer.
Regulations
Observe the following when working on this system:
■
National installation regulations
■
Statutory regulations regarding the prevention of
accidents
■
Statutory regulations regarding environmental pro-
tection
■
The Code of Practice of relevant trade associations
■
All current safety regulations as defined by DIN, EN,
DVGW, VDE and all locally applicable standards
a
ÖNORM, EN and ÖVE
c
SEV, SUVA, SVTI and SWKI
If you smell flue gas
Danger
Flue gas can lead to life threatening poisoning.
■
Shut down the heating system.
■
Ventilate the installation site.
■
Close all doors in the living space.
Flue systems and combustion air
Ensure that flue systems are clear and cannot be
sealed, for instance due to accumulation of conden-
sate or other causes. Ensure a sufficient supply of
combustion air.
Instruct system users that subsequent modifications to
the building characteristics are not permissible (e.g.
cable/pipework routing, cladding or partitions).
Danger
Leaking or blocked flue systems, or an insuffi-
cient supply of combustion air can cause life
threatening poisoning from carbon monoxide in
the flue gas.
Ensure the flue system is in proper working
order. Apertures for supplying combustion air
must be non-closable.
Extractors
Operating appliances that extract air to the outside
(cooker hoods, extractors, air conditioning units, etc.)
can create negative pressure. If the boiler is operated
at the same time, this can lead to reverse flow of the
flue gas.
Danger
The simultaneous operation of the boiler and
appliances that extract air to the outside can
result in life threatening poisoning due to
reverse flow of the flue gas.
Fit an interlock circuit or take suitable steps to
ensure a sufficient supply of combustion air.
Working on the system
■
Isolate the system from the power supply (e.g. by
removing the separate fuse or by means of a mains
isolator) and check that it is no longer 'live'.
■
Safeguard the system against reconnection.
Danger
Hot surfaces can cause burns.
■
Before maintenance or service work, switch
OFF the appliance and let it cool down.
■
Never touch hot surfaces on the boiler, burner,
flue system or pipework.
!
Please note
Electronic assemblies can be damaged by elec-
trostatic discharge.
Before beginning work, touch earthed objects,
such as heating or water pipes, to discharge
static loads.
Repair work
!
Please note
Repairing components that fulfil a safety func-
tion can compromise the safe operation of the
system.
Faulty components must be replaced with origi-
nal Viessmann spare parts.
Safety instructions
Safety instructions
5548 462 GB