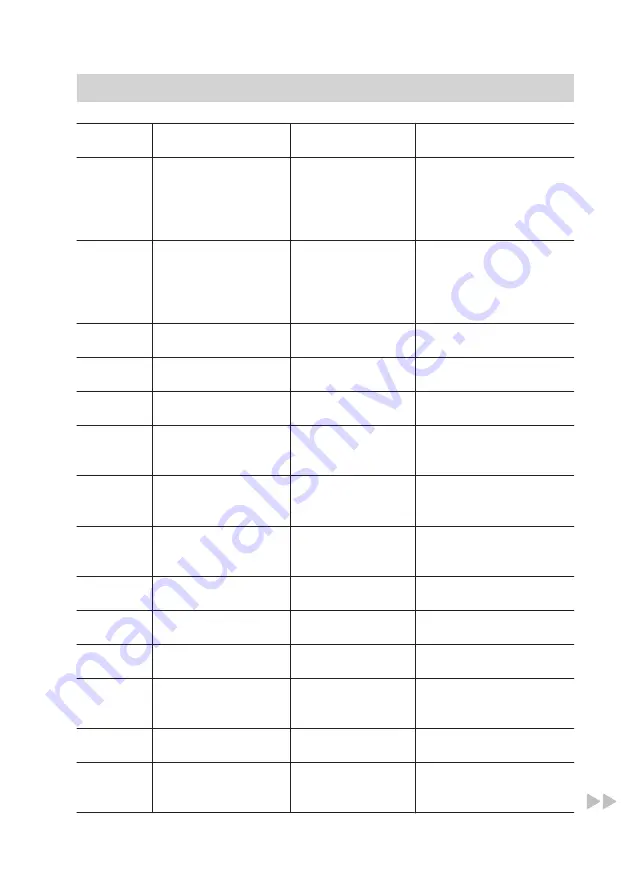
31
Fault code System characteris-
tics
Cause
Measures
26
Ionisation flame mon-
itor reports external
light ingress during
start-up or after post-
purge
Gas train leaks
Replace gas train
26
Ionisation flame mon-
itor reports external
light ingress during
start-up or after post-
purge
Incorrect parame-
ter set selected
Adjust the parameter set
(see page 24 to 25)
27
Flame extinguishes
during operation
Incorrect gas type
selected
Adjust the gas type (see
page 7)
27
Flame extinguishes
during operation
Burner gauze
assembly faulty
Replace burner gauze
assembly
27
Flame extinguishes
during operation
Incorrect parame-
ter set selected
Adjust the parameter set
(see page 24).
27
Flame extinguishes
during operation
Combustion char-
acteristics not
ideal
Adjust burner (see from
page 12).
29
Burner control unit
fault
Internal fault of gas
pressure switch
input
Replace burner control
unit
2A
Burner control unit
fault
Internal fault of air
pressure switch
input
Replace burner control
unit
2b
Burner control unit
fault
Internal flame
monitor fault
Replace burner control
unit
2C
Burner control unit
fault
Fault during test of
safety inputs
Replace burner control
unit
2d
Burner control unit
fault
Internal low volt-
age monitor fault
Replace burner control
unit
2E
Burner control unit
fault
Internal voltage
failure monitor
fault
Replace burner control
unit
2F
Burner control unit
fault
Internal heat
demand fault
Replace burner control
unit
2H
Burner control unit
fault
Lead break, strap-
ping plug
fJ
,
safety chain
Check strapping plug
fJ
Troubleshooting
Diagnosis
(cont.)
5692 488 GB