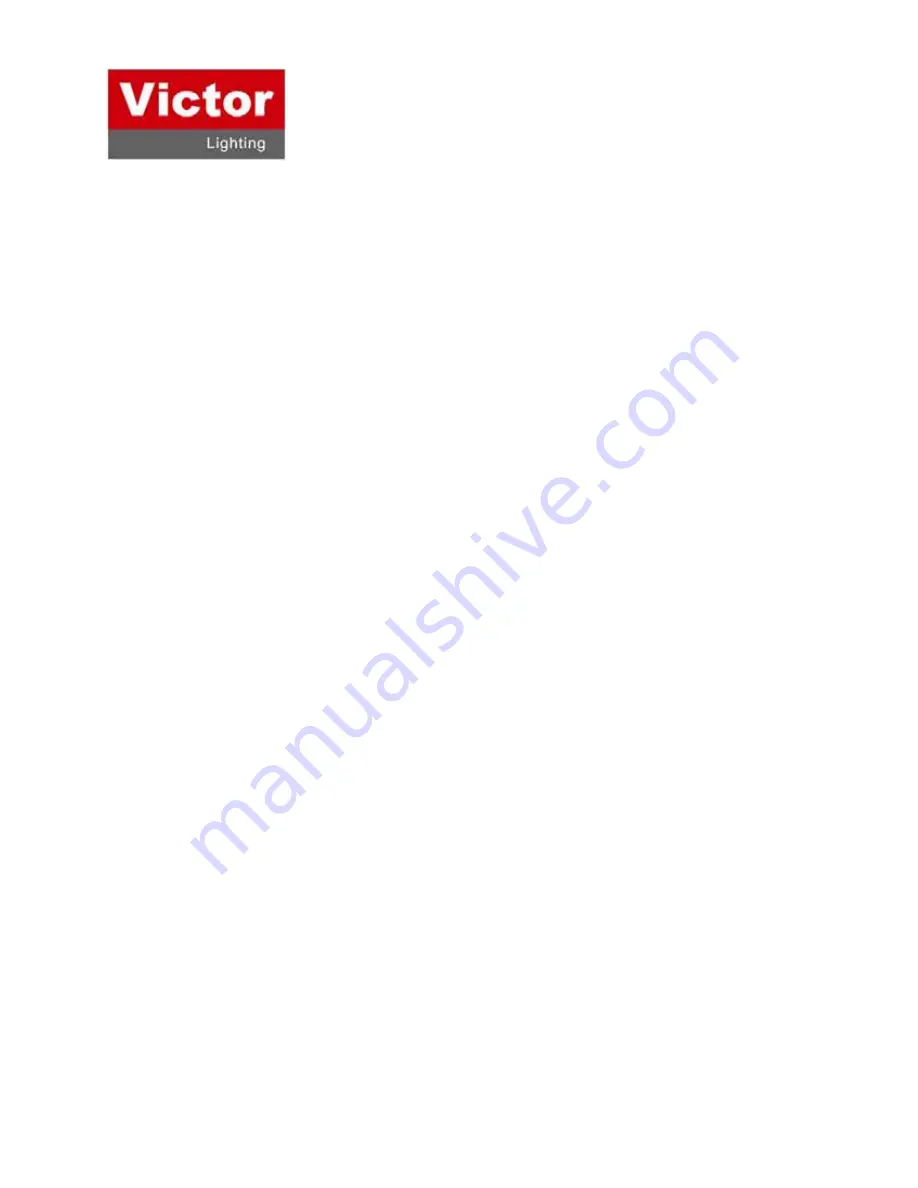
IOM – VL71 FLOODLIGHT
VL71 IOM
IECEx
ATEX
Issue 02
May 08
4
3.4
Lamps
The lamps used in this range are of a standardised type, and there is no preference between makes, or in the case of HPS
colour. Due to the need to control photometric performance and certification conditions, and avoid incorrect lamps being
fitted, the type of lamp and size is specified on the rating plate. If mixed installations are used, care must be taken to ensure
that the correct lamp is fitted on installation and replacement.
HPS and MBI lamps should be replaced shortly after they do not light
. One indication of the end of life for HPS lamps is
'cycling' where the lamp goes out then re-ignites after a minute or so interval. If discharge luminaires are burned continuously
they should be switched off occasionally, to allow old lamps to fail to re-ignite rather than possibly become diodes with
detrimental effects on control gear. The above information is current at the time of publication. The development of lamps
and control gear is ongoing and detailed advice on lamp performance can be obtained from the Technical Department or the
lamp supplier.
HPS and MBI circuits should not be energised without a lamp fitted
. HPS lamps without an internal
ignitor should be used. The current HPS control gear is incompatible with internal ignitor lamps.
3.5
Mounting
Floodlights should be installed where access for maintenance is practical and in accordance with any lighting design
information provided for the installation. This will usually consist of aiming points and aiming angles.
Mounting arrangements should be secured with lock washers or self-locking nuts and bolts.
3.6
Cabling and Cable Glands
3.6.1 Cable Glands
Cable glands and sealing plugs when installed must maintain the properties of the restricted breathing enclosure.
Rubber sealing washers and steel compression washers are provided with the unit.
The installer and user take responsibility for the selection of cables, cable glands and seals.
The product is certified for ATEX and to comply with the certification for installation and use within the EU, cable glands and
sealing plugs must have ATEX component approval.
For installation outside the EU, suitable cable glands in accordance with (IECEx) EN 60079-0 will meet the technical
requirements.
The cable and gland assembly when installed must maintain the IP66/67 rating of the floodlight.
The cable gland must withstand an impact value of 7Nm where the risk of mechanical damage is high or 4Nm where the risk
of mechanical damage is low.
Sealing plugs must be similarly rated and a tool must be used for their removal. Where the cable is not reliably clamped
externally to the apparatus, the cable gland must clamp the cable against a pull in Newtons of 20 x the cable OD in mm for
non-armoured cable and 80 x the cable OD for armoured cable. Where brass cable glands are used in a corrosive
environment cadmium or nickel plating should be used. Two tapped cable entries are provided, one with a plug and seal
suitable for permanent use, the other has a travelling plug. M20 x 1.5 entries are standard, other sizes are available on
request. A Hawke 501/453/RAC would be suitable for the above.
3.6.2 Cable
At maximum rated ambient temperature refer to rating table for minimum cable temperature rating. The luminaire is also
rated with the temperature rise at the cable entry. This allows the user to adjust the cable spec. for an
actual
T amb lower
than that for which the luminaire is certified. The standard looping conductor size is 6mm².
Internal and external earth points are provided.
Standard 300/500V rated cable is suitable. The cable make-up must be suitable to ensure the maintaining of the restricted
breathing enclosure when the cable gland assembly is fitted.
The selection of cable size will be suitable for the fuse rating. Some guidance on this is given below. When MCB's are used,
the type with the higher inrush current resistance, as used for motor starting and lighting, should be specified.
3.6.3 Cable Connection
The cable connections are made by removing the front cover. Before removing front cover check that the support chain is
sound. The cover is released by undoing the six toggle clamps, using a screwdriver or suitable metal rod. The reflector is