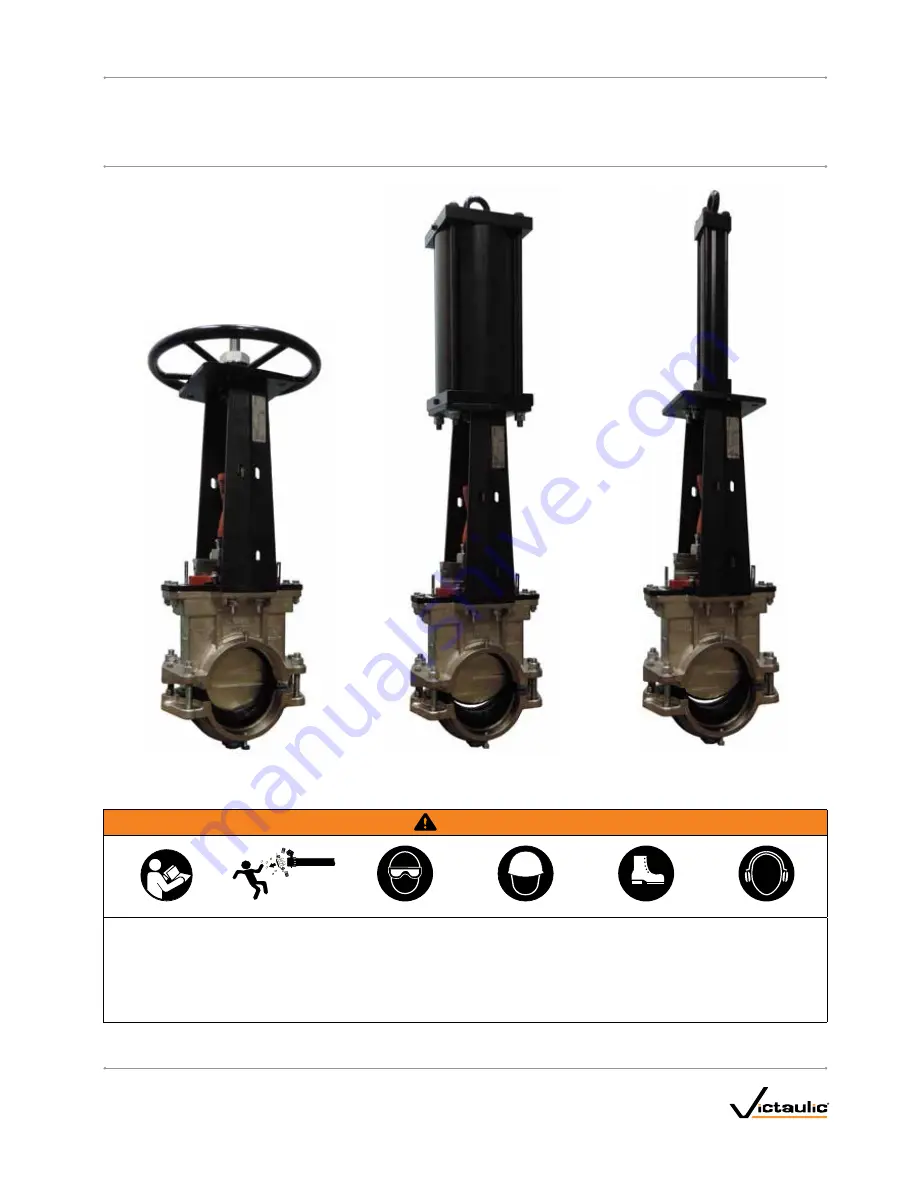
WARNING
• Read and understand all instructions before attempting to install, remove, adjust, or maintain any Victaulic piping products.
• Depressurize and drain the piping system before attempting to install, remove, adjust, or maintain any Victaulic piping products.
• Wear safety glasses, hardhat, foot protection, and hearing protection.
Failure to follow instructions and warnings could cause system failure, resulting in death or serious personal injury and property damage.
HANDWHEEL OPERATOR
PNEUMATIC OPERATOR
HYDRAULIC OPERATOR
I-795/906
REV_D
I-795/906
INSTALLATION AND MAINTENANCE INSTRUCTIONS
Series 795 and 906 Installation-Ready
™
Knife Gate Valves