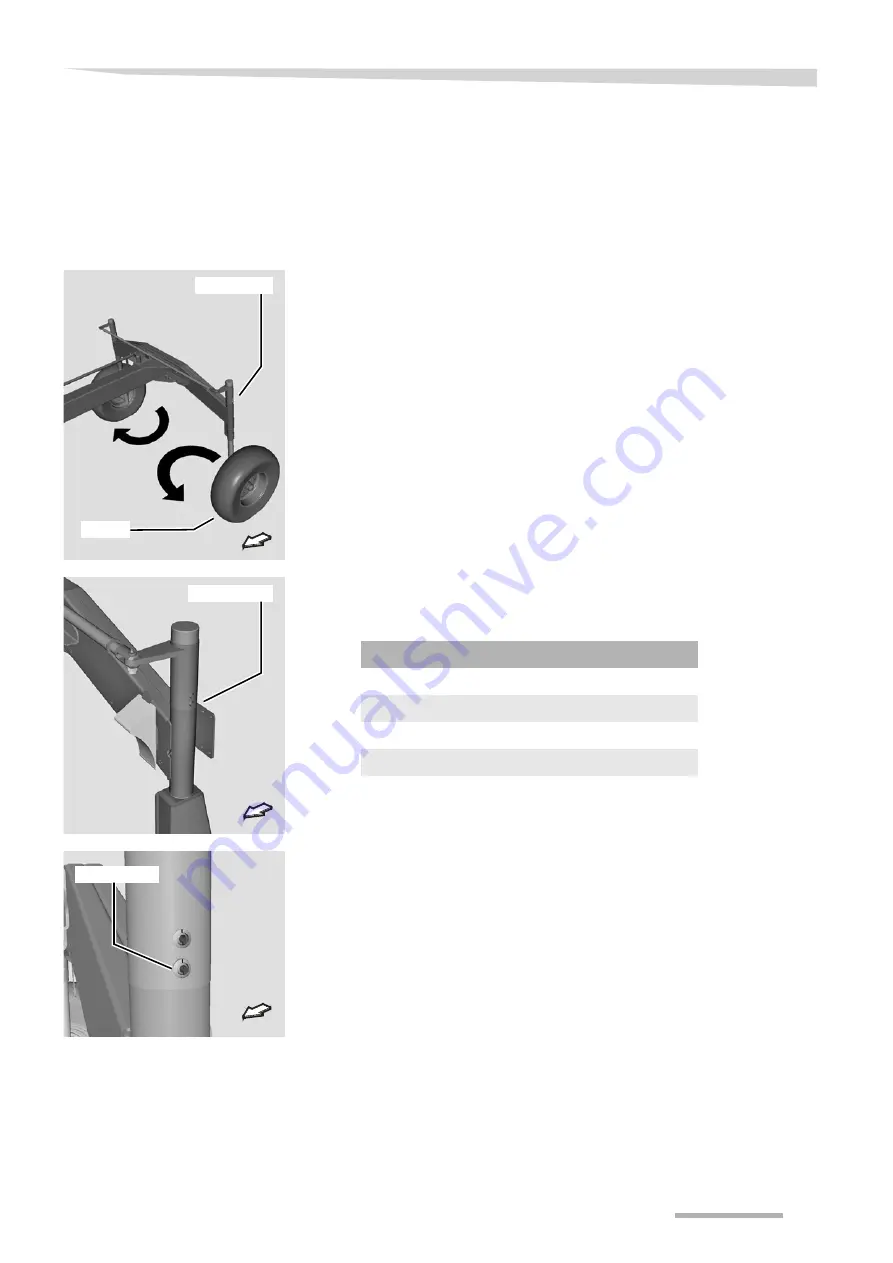
Quick Set assembly
19
Main frame
Use appropriate lifting accessories to remove the machine elements.
Loosen all fastenings (wires, lashing straps).
Turn axles
The main frame is preassembled. The wheels of the transport chassis
point inwards and turn outwards.
Secure the transport chassis using appropriate lifting accessories.
Release the dowel pins on the transport chassis.
Lift the transport chassis slightly using lifting accessories.
Turn the transport chassis axles outwards.
Lower the transport chassis using lifting accessories.
Drive in the dowel pins – contra-rotated by 90° – to secure the
transport axles.
Wheels
Dowel pins
Dowel pins
No.
Quantity
Part
1
1
Main frame
2
1
Transport chassis
3
4
Dowel pin, large
4
4
Dowel pin, small
Dowel pins