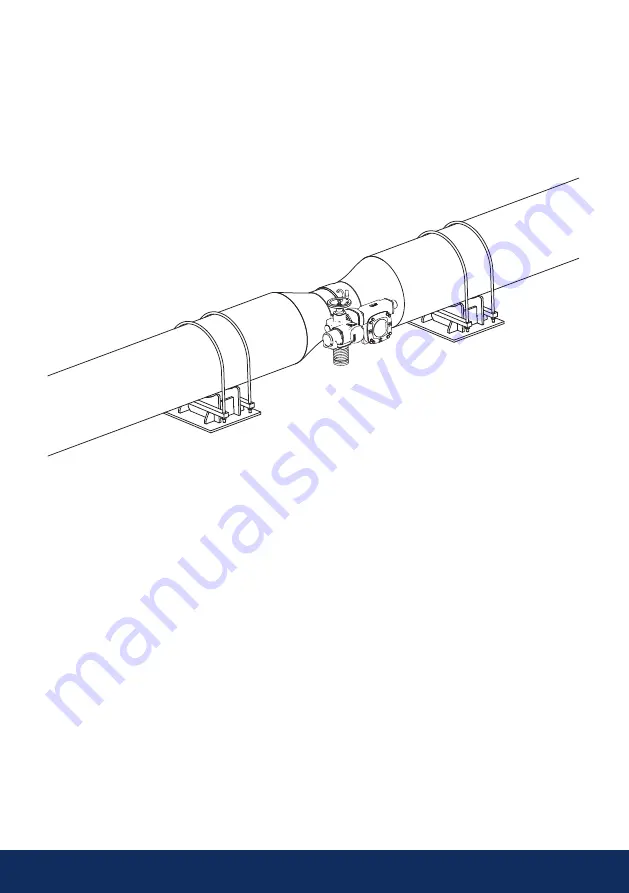
12
13
www.vexve.com
www.vexve.com
Figure 15. Pipeline supports.
4.3 Pipeline supports and pipeline reducers
Pipeline supports should not be installed under the valve!
If pipeline reducers are used in connection with the valve, additional pipeline supports must be used
because of the higher mechanical load on the valve (see figure 15).