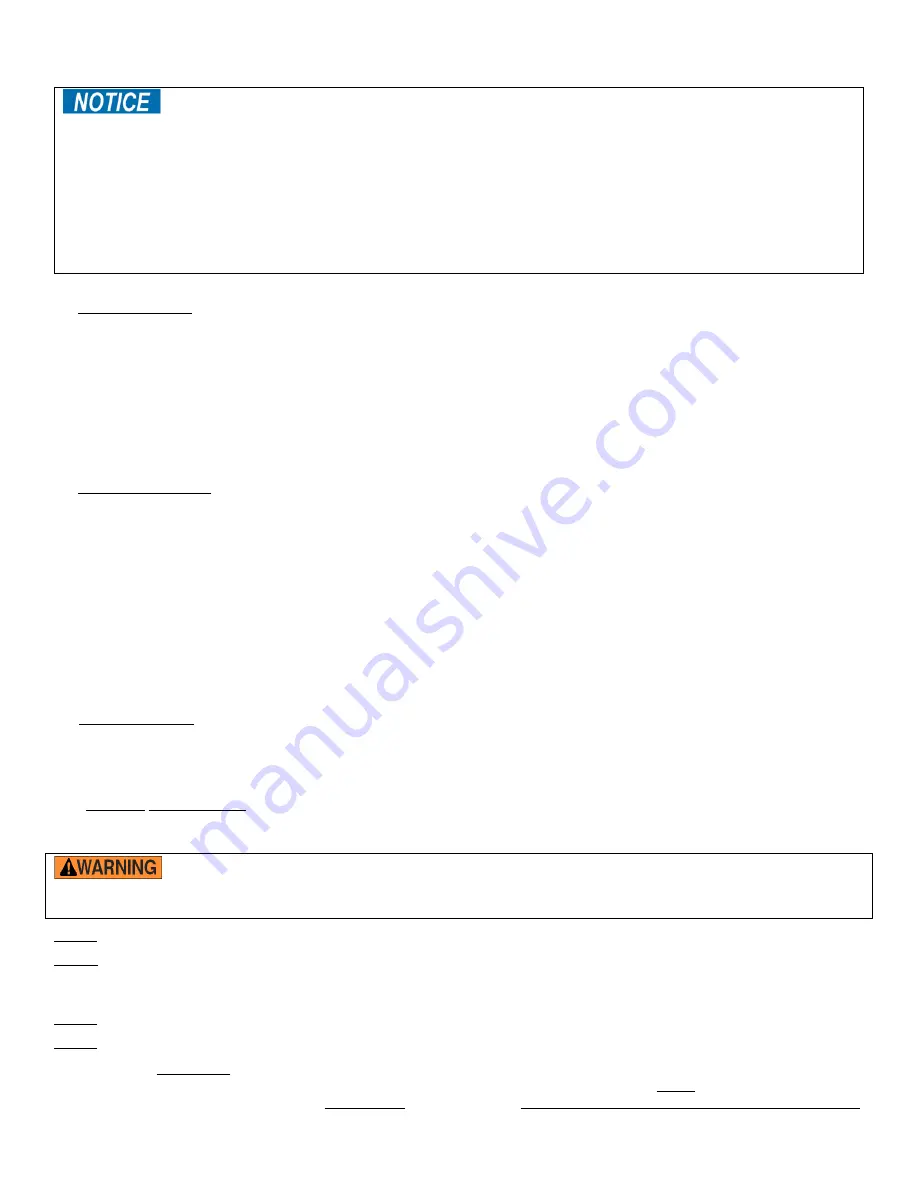
rev. 11/1/2016
CB-PMPS, manual.doc
Copyright 2016 Vestil Manufacturing Corp. Page 21 of 23
INSPECTIONS & MAINTENANCE:
Proper use, maintenance, and storage are essential for this product to function properly.
o
Always use this product in accordance with the instructions in this manual and consistent with any training relevant
to machines, devices, etc. used in conjunction with this product.
o
Relieve hydraulic pressure whenever the unit is not in use by fully lowering the forks.
o
Keep the product clean & dry. Lubricate moving parts at least once per month.
o
ONLY use manufacturer-approved replacement parts. Vestil is not responsible for issues or malfunctions that result
from the use of unapproved replacement parts.
o
Do not use brake fluid or jack oils in the hydraulic system. If oil is needed, use an anti-wear hydraulic oil with a
viscosity grade of 150 SUS at 100°F, (ISO 32 cSt @ 40°C), or Dexron transmission fluid.
o
Contact the manufacturer for SDS information.
Inspections:
(A) Before Each Use—visually inspect the following:
1. Wiring: inspect the electrical wiring for cuts, frays etc.
2. Casters: examine each caster and confirm normal operating condition, i.e. rolls smoothly without wobbling, not
cracked, or severely worn,
3. Hydraulic hoses: check for pinches, punctures, and loose connections.
4. Structure: inspect the base and frame for deformations and cracked welds.
5. Forks, carriage and mast: cycle the forks up and down while listening and watching unusual noise, motion, or
binding.
6. Pushbutton controller: inspect the controller and look for damage that exposes wiring inside the controller
housing.
(B) Monthly Inspections--at least once per month check the following:
1. Oil level. Oil should be 1" to
1-1/2"
below the top of the tank with the lift in the fully lowered position. Add as
necessary. Look for oil leaking from hoses, the cylinder, or the reservoir. See “Troubleshooting” (p. 21-22) and
correct as necessary.
2. Battery: check the water level in the battery
.
(DC models only)
3. Clevis and pivot points: inspect for excessive wear.
4. Hydraulic system, wiring, and pushbutton controller: Check for worn or damaged hydraulic hoses, electrical wires,
and cords. Repair as necessary.
5. Carriage rollers (see diagrams on p. 4-7): check rollers and retaining hardware for normal condition.
6. Forks, carriage and mast: cycle the forklift function up (to the top) and back down while listening and watching for
unusual noise, motion, or binding.
7. Labels (see “Label placement diagram; p. 23): confirm that all labels are in place and in good, readable condition.
8. Surfaces: remove dirt and debris
.
(C) Yearly Inspection
Hydraulic oil should be changed at least once a year or sooner if the oil darkens or becomes gritty. Flush the reservoir
before refilling. Similarly, if the oil appears milky, water is present and the oil should be changed.
Maintenance:
The end-user/your employer should implement a maintenance program to ensure the proper function and safety of the
device. ANSI/ITSDF standard B56.10 describes some recommended maintenance procedures. The following steps
should be utilized in conjunction with those recommendations.
The end-user is responsible for selecting and training employees to work on the lifter. “Work on” refers to
operating, loading, cleaning, servicing, maintaining, or repairing the product. ONLY trained, authorized maintenance
personnel or contractors should perform inspection, maintenance, or repair work.
Step 1: Tag the unit, “Out of Service.”
Step 2: Conduct a “Before each use”. If deformity, corrosion, rusting, or excessive wear of structural members is present,
DO NOT use the pallet handler. Contact Vestil for instructions. If the carriage does not move smoothly or makes noise as
it moves up or down the mast, apply a silicon wax or silicon spray to the inside of the mast frame.
Step 3: Remove any dirt or other matter from the forks and other surfaces.
Step 4: Perform all other necessary adjustments and/or repairs. DO NOT modify the CB-PMPS.
NOTE:
An adjustment is a simple correction that restores the lifter to normal operating condition, such as tightening
loose fasteners, or removing dirt or other debris from the surface of the dumper. A repair refers to replacing worn
parts with new replacement parts. A modification is a change that alters the machine from normal operating condition,
like bending the structural members or removing a part or several parts. DO NOT modify the lifter in any way.