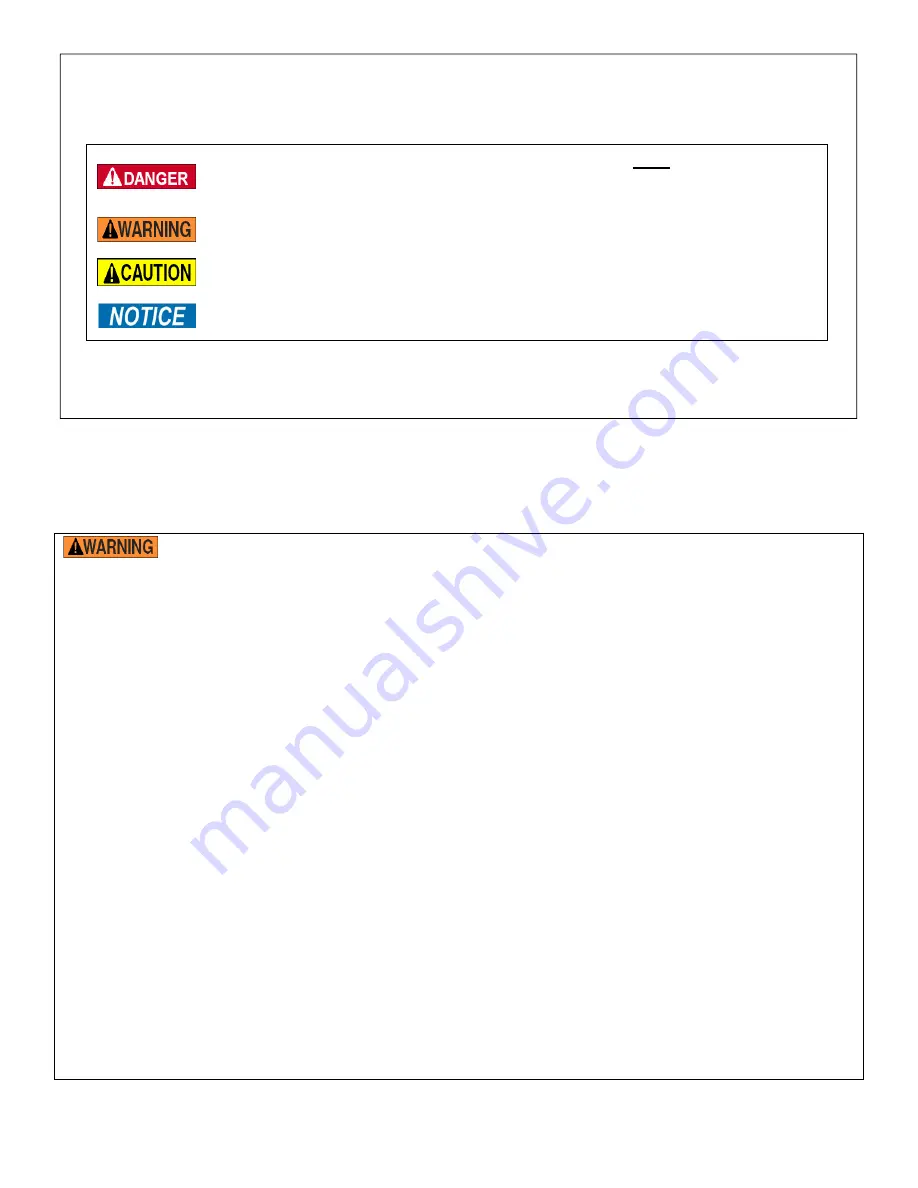
rev. 11/1/2016
CB-PMPS, manual.doc
Copyright 2016 Vestil Manufacturing Corp. Page 2 of 23
Hazard identification with signal words
This manual uses SIGNAL WORDS to identify dangers that might arise during use the probable seriousness of
those injuries, if the product is misused in the ways described. Other signal words call attention to uses of the
product likely cause property damage. Signal words used in this manual appear below along with their definitions.
Identifies a hazardous situation which, if not avoided, WILL result in DEATH or
SERIOUS INJURY. Use of this signal word is limited to the most extreme
situations.
Identifies a hazardous situation which, if not avoided, COULD result in DEATH or
SERIOUS INJURY.
Indicates a hazardous situation which, if not avoided, COULD result in MINOR or
MODERATE injury.
Identifies practices likely to result in product/property damage, such as operation that
might damage the product.
Each person who assembles, installs, uses, or maintains this product should read the entire manual
and fully
understand the directions in advance. If after reading the manual you do not understand an instruction, ask
your supervisor or employer for clarification, because failure to adhere to the directions in this manual
might result in serious personal injury.
Safe use recommendations:
Vestil diligently strives to identify foreseeable hazards associated with the use of its products. However, material
handling is inherently dangerous and no manual can address every conceivable risk. The end-user ultimately is
responsible for exercising sound judgment at all times.
Improper or careless use of this product might result in serious personal injuries or even death.
Read and understand the entire manual before assembling, installing, using or servicing the product
.
Read the manual to refresh your understanding of proper use and maintenance procedures.
DO NOT modify the product in any way UNLESS you first obtain written approval from Vestil. Unauthorized
modifications might make the lift unsafe to use and automatically void the Limited Warranty (see p. 23).
DO NOT exceed the maximum rated load (see “Specifications” table on p. 3; Label 287 on product).
Inspect the product before each use according to the instructions on p. 21.
A. DO NOT use this product if the inspection reveals structural damage. Examples of structural damage include,
but are not limited to, the following: 1) Cracked, broken or deformed load-bearing members (forks, fork
carriage, mast, wheels, and frame); 2) cracked welds; 3) corrosion or severe wear; 4) damaged, e.g. leaking,
hydraulic system (cylinder, hoses, reservoir, etc.). Remove the product from service if it fails any part of the
inspection. DO NOT use the product until it is fully restored to normal condition. In the event that part of the
hydraulic system is damaged, AVOID contact with pressurized hydraulic oil (leaking from a ruptured hose, for
instance). High pressure oil easily punctures skin which can cause injury such as gangrene.
B. DO NOT use the product if any unusual noise or movement is observed. If a malfunction occurs, remove the
unit from service and notify your supervisor & maintenance personnel about the issue.
C. ONLY use manufacturer-approved replacement parts.
DO NOT change the setting of the pressure relief valve.
Whenever using this product, carefully watch the lifter and the load.
DO NOT use this device UNLESS all product labels (see “Labeling Diagram” on p. 22) are readable and undamaged
AND all machine guards (i.e. the expanded metal mast guard and formed wheel guards) are in place.
This product is NOT a personnel lift. DO NOT use the pallet handler to lift people.
DO NOT walk or stand beneath the forks at any time.
DO NOT leave the pallet handler unattended while it is loaded. ALWAYS fully lower the forks and engage the floor
lock before leaving the pallet handler unattended.
ONLY transport loads with the forks no higher than is necessary to fully support the load and avoid obstacles.
To pick up a pallet with this lifter, insert the forks into the fork pockets of the selected pallet until it firmly contacts the
upright portion of both forks (i.e. the “heels”).
DO NOT continue to push the “UP” button on the controller if the forks do not rise. Remove the unit from service and
report the problem to maintenance personnel.