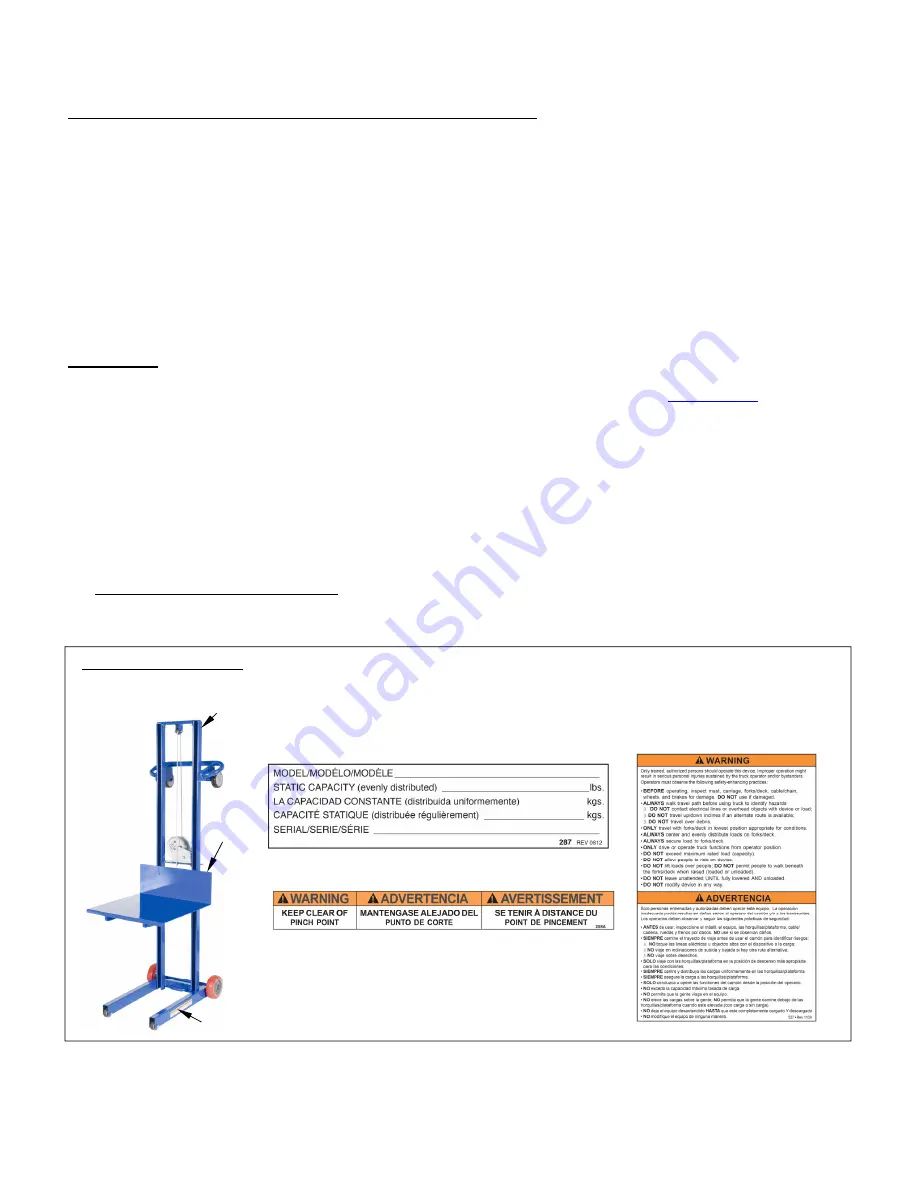
Rev. 6/26/2017
LLW, MANUAL
Copyright 2017 Vestil Manufacturing Co.
Page
15
of
16
conducting future inspections, compare those observations with the record to determine if a component requires
repair or replacement.
At least once every 2 weeks, visually inspect the following components
:
1. Winch, winch mounting bracket (see “Raising and lowering the deck”, p. 13), cable, and pulley: Cycle the deck up
and down. Listen for unusual noises and watch for binding or rough movement as the deck moves. Examine the
winch. Make sure that the spool is intact and rotates smoothly when the handle is turned. Inspect the mounting
bracket. The winch should be solidly attached to the bracket. Tighten all loose fasteners. Lower the deck and
examine the cable for reeving, stretching, thinning portions, etc. Confirm that the pulley rotates freely and is
securely fastened to the mast.
2. Frame (mast, base, deck, and deck rollers): examine the frame members for damaged welds, severe rusting,
cracks, bends, etc. Remove rust with steel wool. Clean the affected areas and apply touch-up paint.
3. Casters and wheels: check each caster and wheel for wobbling, damage, and severe wear. Wheels and casters
should roll smoothly. Clean the casters to remove grit from the surfaces, if necessary.
4. Hardware: examine the pins, bolts, nuts, etc. Tighten loose fasteners.
5. Floor lock: if your unit is equipped with the floor lock option confirm that it makes solid contact with the ground
when applied. Check the condition of the rubber pad. Replace the pad if wear or damage affects its function.
Maintenance:
Implement a maintenance program to ensure that the lifter functions properly. Page 9 of ANSI/ITSDF
standard B56.10-2006, “Manually propelled high lift industrial trucks”, describes recommended maintenance
procedures. A copy of the standard is downloadable for free from the ITSDF website (see
www.itsdf.org
). Apply those
recommendations in conjunction with the following steps.
U
1
U
. Tag the lifter, “Out of Service.”
U
2
U
. Inspect the lifter as described above. If deformity, corrosion, rusting, or excessive wear of structural
members is present, DO NOT use the lifter. If the deck does not move smoothly or makes noise as it
moves up or down the upright, apply a silicon wax or silicon spray to the inside of the mast frame.
U
3
U
. Remove any dirt or other matter from the cable and pulleys and other lifter surfaces.
U
4
U
. Perform all other necessary adjustments and/or repairs. DO NOT modify the lifter.
U
5
U
. Make a dated record of the repairs, adjustments and/or replacements made.
6. Platform, mast and platform rollers: cycle the platform up and down while listening for unusual noises and
watching for binding or rough movement.
Labeling diagram:
The lifter should always be labeled as shown below. Contact Vestil to order replacement
labels.
A: Label 287 (on back side of mast)
B: Label 527 (on back side of
mast)
B
A
C
C: Label 208 (on both legs)