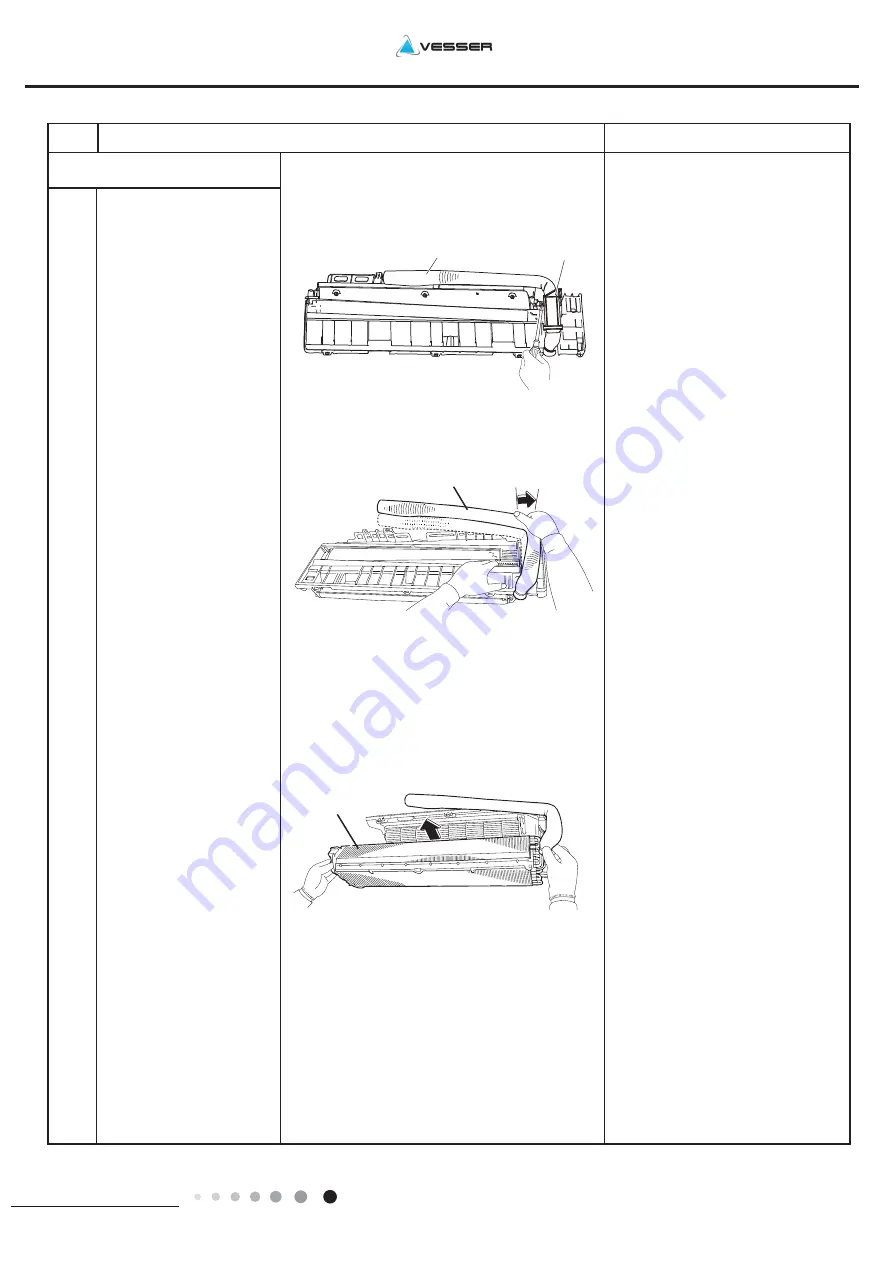
WGC-IT / GC-IT Model:
18
- 2
4
Installation and Maintenance
6HUYLFH0DQXDO
6WHSV
3URFHGXUH
3RLQWV
7. Remove piping fixture.
Remove Pipe Clamp
a
Loosen the screws,
in the right and the left,
which fix the Evaporator
Assy. Remove Evaporator
Assy
b
Auxiliary piping
Piping fixture
Adjust the pipeline slightly
c
Auxiliary piping
Heat exchanger