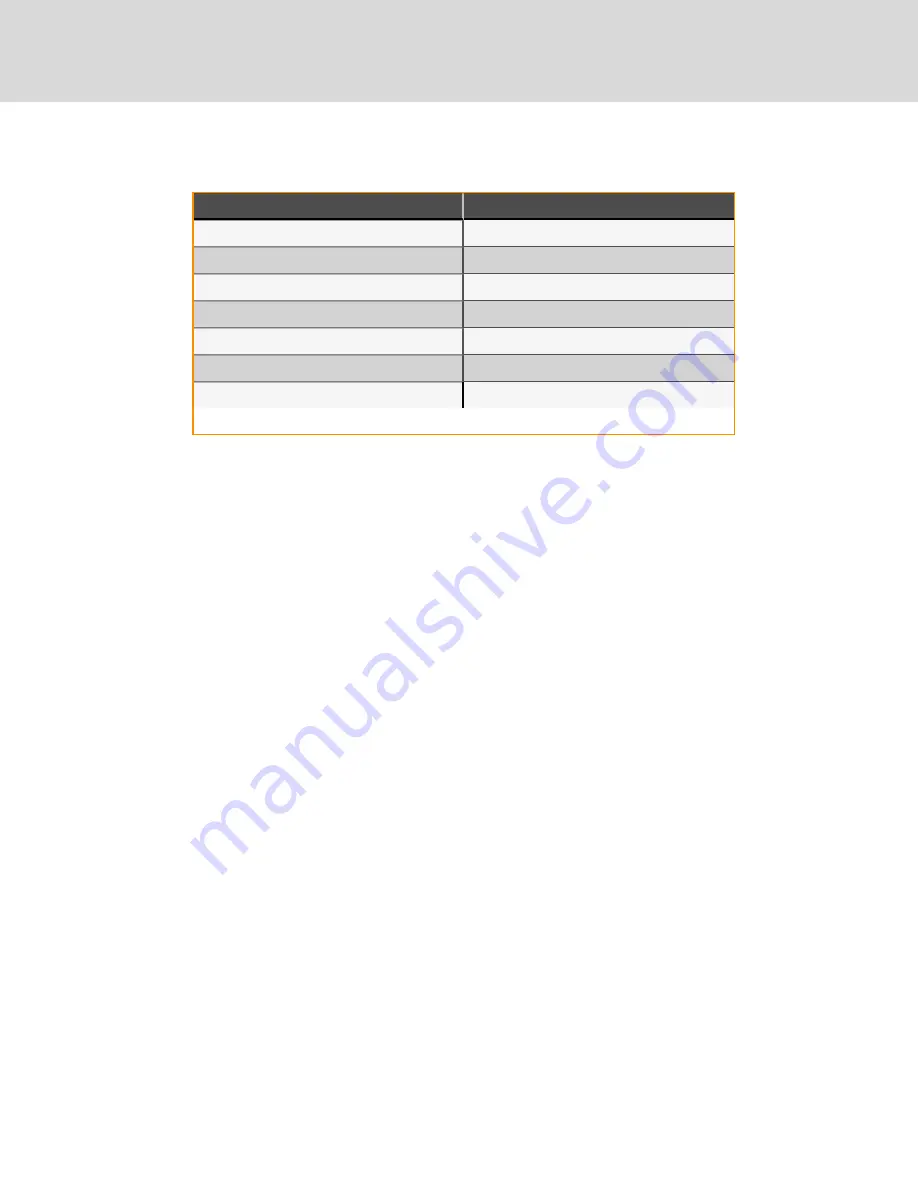
Pipe diameter, in.
Oil volume, oz (ml)
1/2
0.2 (5.9)
5/8
0.4 (11.8)
3/4
0.6 (17.7)
7/8
0.9 (26.6)
1-1/8
1.8 (53.2)
1-3/8
3.3 (97.6)
1-5/8
5.5 (162.7)
Source: DPN003950, Rev. 6
Table 6.11 Volume of Oil in Standard Form Trap by Pipe Diameter
6.2.6 Evacuation, Leak Testing, and Charging Air Cooled Systems
Two discharge lines and two liquid lines must be field installed between the indoor unit and the outdoor condenser.
NOTE: Keep the evaporator unit, receiver (if equipped), and condenser closed with their factory charge of dry
nitrogen while all field piping is installed. Keep the field piping clean and dry during installation. Do not allow it to
stand open to the atmosphere. When all the field interconnecting piping is in place, vent each outdoor unit’s dry
nitrogen charge and connect to the field piping. Finally, vent the evaporator unit's dry nitrogen charge and make its
piping connection last. Follow all proper brazing practices, including a dry nitrogen purge to maintain system
cleanliness. The condenser connection pipes must be wrapped with a wet cloth to keep the pressure and temperature
sensors cool during any brazing.
Evacuation and Leak Testing Air Cooled Systems
For proper leak check and evacuation, you must open all system valves and account for all check valves.
NOTE: The system includes a factory installed check valve and an additional downstream Schrader valve with core in
the compressor discharge line. Proper evacuation of the condenser side of the compressor can be accomplished only
using the downstream Schrader valve. See the appropriate piping schematic for your system in
.
1.
Starting with Circuit #1, open the service valves and place a 150 PSIG (1034 kPa) of dry nitrogen with a tracer
of refrigerant. Check the system for leaks with a suitable leak detector.
2.
With pressure still in Circuit #1, open the compressor service valves in Circuit #2.
•
If pressure increases in Circuit #2, the system is cross-circuited and must be re-checked for proper
piping.
•
If there is no pressure increase, repeat step 1 on Circuit #2.
3.
After completion of leak testing, release the test pressure, (observe local code) and pull an initial deep vacuum
of 500 microns on the system with a suitable pump.
4. After four hours, check the pressure readings and, if they have not changed, break vacuum with dry nitrogen.
Pull a second and third vacuum to 500 microns or less. Re-check the pressure after two hours.
When the three checks are complete, remove the jumper hose from the service valve fitting and the condenser,
and proceed to
Charging DA250 Air Cooled Systems (Liebert® MCV440 with Receivers)
Vertiv | Liebert® DSE Thermal Management System Installer/User Guide
32