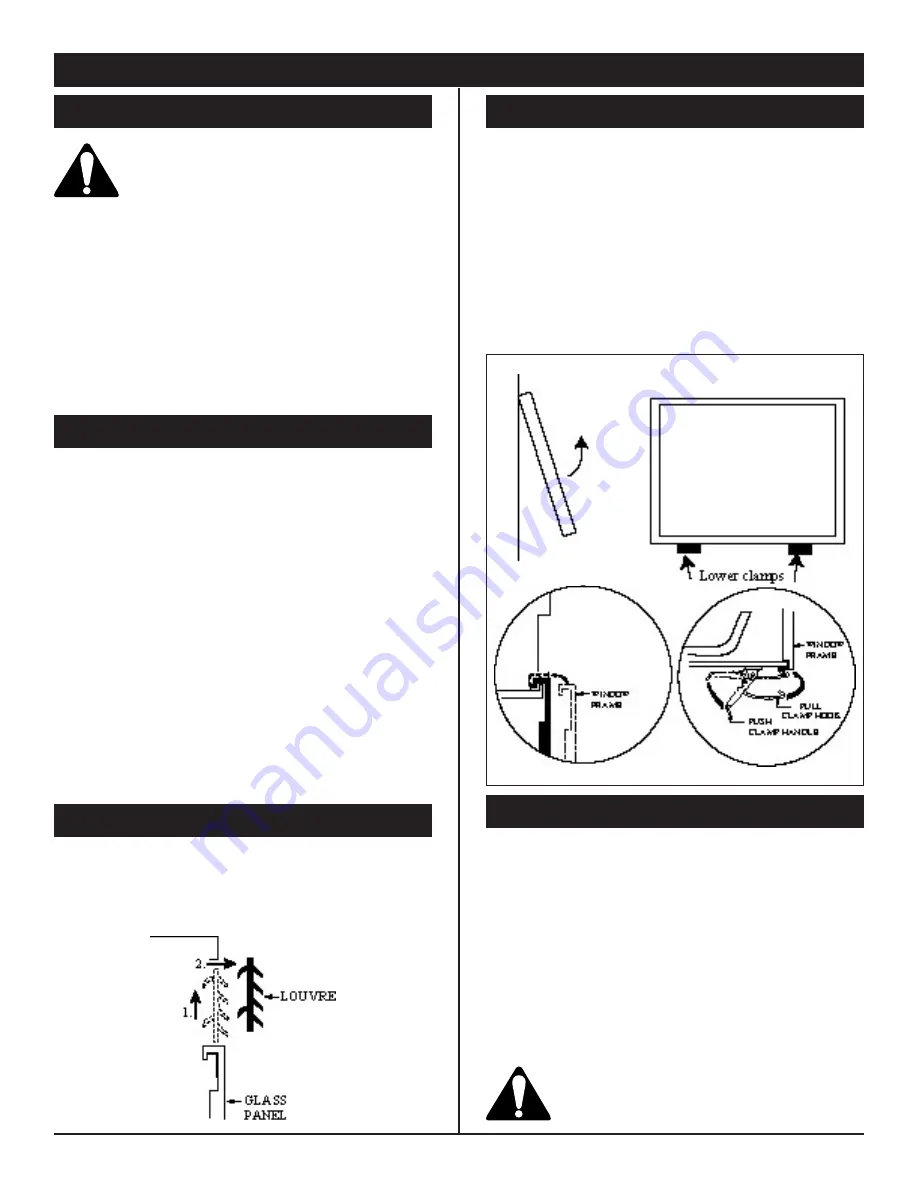
DBT33/DBT36/DBT39
-20-
10002789/0
G
ENERAL
O
PERATING
I
NSTRUCTIONS
G
LASS
I
NFORMATION
Only glass approved by CFM Majestic Inc.
should be used on this replace.
• The use of any non-approved replacement glass will void
all product warranties.
• Care must be taken to avoid breakage of the glass.
• Under no circumstances should this appliance be operated
without the front glass in place, or with the glass in a
damaged condition.
• Replacement glass (complete with gasket) is available
your dealer and should only be installed by a licensed
qualied service person.
G
ENERAL
M
AINTENANCE
Burner and Burner Compartment
It is important to keep the burner and the burner compartment
clean. At least once per year the logs and lava rock/ember
material should be removed and the burner compartment vacu-
umed and wiped out. Remove and ret the logs as per the
instructions in this manual.
Always handle the logs with care as they are fragile and may
also be hot if the replace has been in use.
FK24/FK12 Fan Assembly
The fan unit requires periodic cleaning. At least once per
month in the operating season open the lower louvre panels
and wipe or vacuum the area around the fan to remove any
build up of dust or lint.
Brass Trim
Clean the brass trim pieces using a soft cloth lightly dampened
with lemon oil. Do not use water or household cleaners on
any brass components.
L
OUVRE
R
EMOVAL
The top louvre panel is removed by lifting the panel vertically
and pulling it away from the appliance, Fig. 39.
The lower access door is hinged along the bottom edge and is
folded down to allow access.
G
LASS
/ F
RAME
R
EMOVAL
1. Turn the replace OFF (including the pilot).
2. If the unit has been operating allow time for the compo-
nents to cool.
3. Remove the top louvre assembly.
4. Open the lower louvre panel.
5. Release the two clamps securing the lower edge of the
frame by pulling down on the handles, Fig. 40.
6. Tilt the glass frame out slightly at the bottom, lift the
frame up and away rom the replace.
7. To replace the glass frame reverse the procedure.
G
LASS
C
LEANING
It is necessary to periodically clean the glass.
During start-up condensation, which is normal, forms on the
inside of the glass. This condensation causes lint, dust and
other airborne particles to cling to the glass surface.
Also initial paint curing may deposit a slight lm on the glass.
It is therefore recommended that the glass be cleaned two or
three times with a non-ammonia based household cleaner and
warm water (we recommend gas replace glass cleaner) within
the rst few weeks of operation.
After this initial cleaning process the glass should be cleaned
two or three times during each operating season depending on
the environment in the house.
Clean the glass after the rst two weeks of
operation.
Fig. 39
Fig. 40