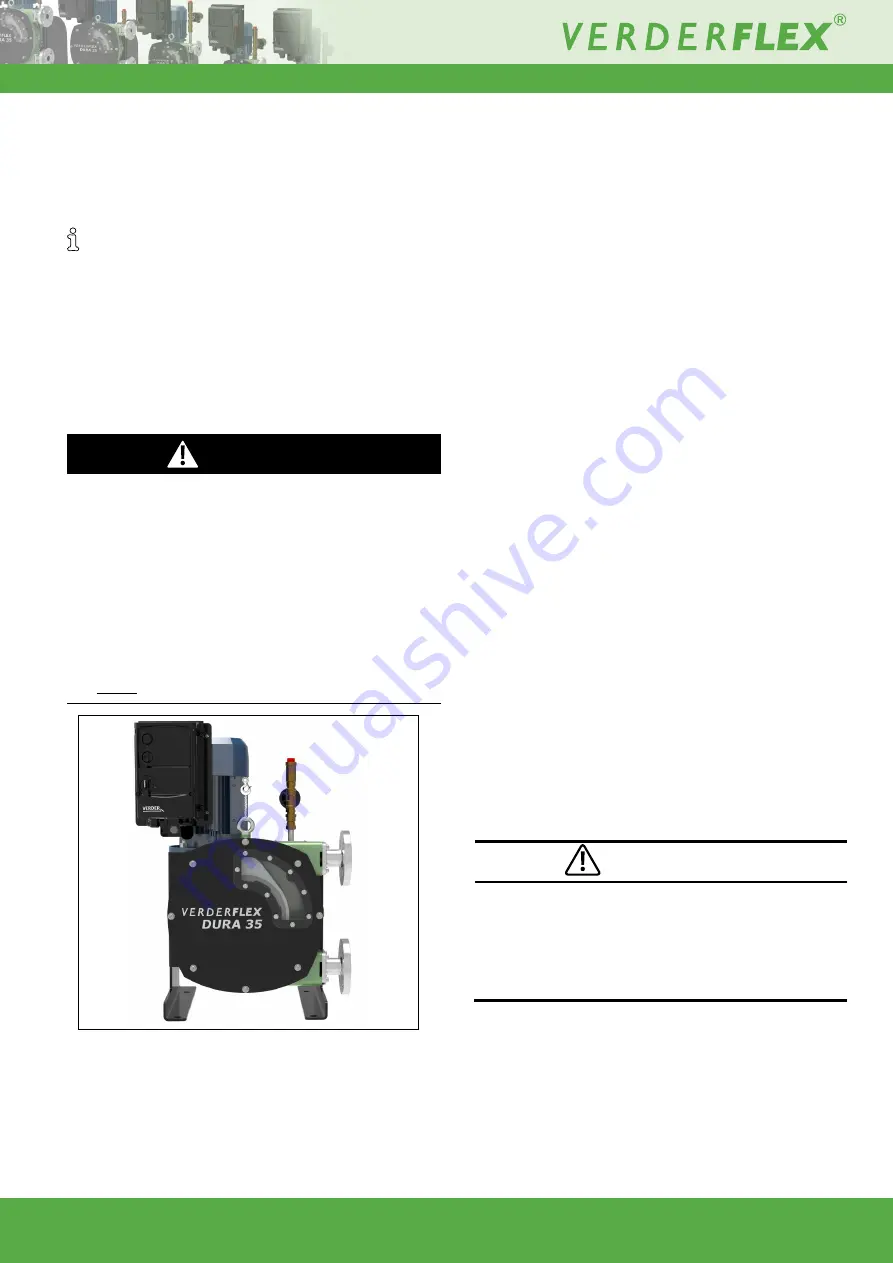
iDura 05-35
Version 1.0v-11/2020
© Verder International B.V
7 | Page
3 Transport, Storage and
Disposal
3.1 Transport
Always transport the pump in a stable position and ensure
that the pump is securely attached to the pallet.
3.1.1 Unpacking and Inspection on Deliv-
ery
1. Report any transport damage to the manufacturer/distribu-
tor immediately.
2. Retain the pallet if any further transport is required.
3.1.2 Lifting
Death or crushing of limbs can be caused by falling
loads!
1. Use lifting gear appropriate for the total weight to be trans-
ported.
2. Make sure the pump and accessories are lifted and moved
by qualified lifting personnel equipped with suitable lifting
gear.
3. Where lifting eye is available, fasten the lifting gear to the
lifting eye as shown in the following illustration. The lifting
eye is available for Dura 15, 25 and 35 only.
4. Do not stand under suspended loads.
DANGER
Figure 1 Fastening Lifting Gear to Pump
3.2 Storage Conditions
1. Make sure the storage location meets the following
conditions:
–
Dry, humidity not to exceed 85%, non-condensing
–
Out of direct sunlight
–
Frost-free; temperature range -5° to +45°C
– Vibration-free
– Dust-free
2. Depending on these conditions, it may be advisable to
place a moisture-absorbing product, such as Silica gel,
inside the pump’s housing or to coat the pump’s inner
surfaces with moisture-repelling oil, such as WD40,
whilst the pump is stored.
3. Hoses should be stored as supplied in their wrapper and
should be stored away from direct sunlight, flat without
any bends or kinks and at room temperature, with end
caps fitted.
4. Lubricants should be stored under normal warehouse
conditions with their caps securely fastened.
5. Gearboxes may require intermittent attention as indicated
by the gearbox manufacturer’s recommendations.
3.3 Interim Storage After Using the
Pump
u
The hose should be removed from the pump.
u
The pump housing lubricant should be drained.
u
The pump housing should be washed out, allowed to dry
and any external build up of product removed.
3.4 Interim Storage Before Using
the Pump
Pump damage caused by interim storage!
u
Allow the pump to reach ambient temperature before
use.
u
Please observe the storage recommendations and use
by dates which apply to hose you may wish to bring into
service after storage.
CAUTION