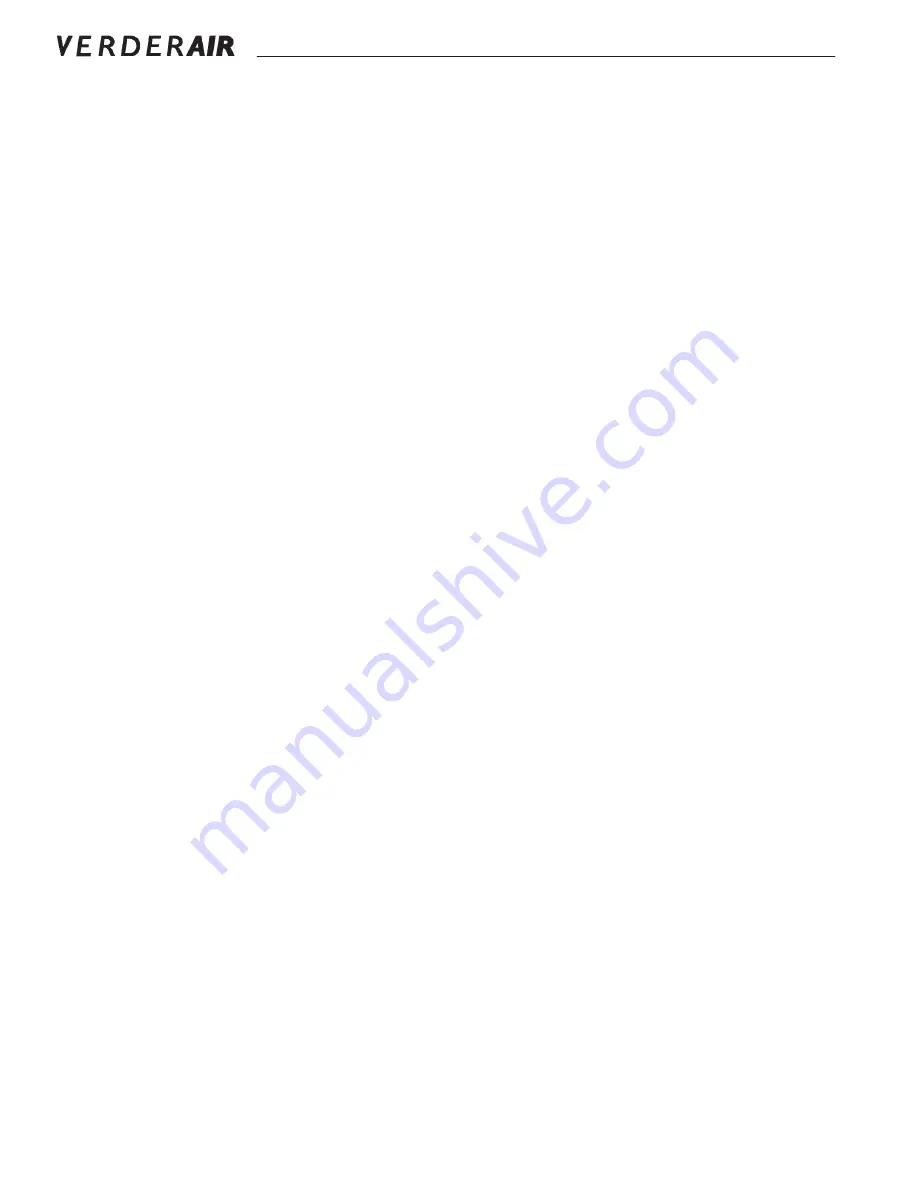
20
819.4496
Service
4.
Unscrew one outer plate (105) from the diaphragm shaft
(24). Remove one diaphragm (401), and the inner plate
(104). See F
For overmolded diaphragms: Grip both diaphragms
securely around the outer edge and rotate
counterclockwise. One diaphragm assembly will come
free and the other will remain attached to the shaft.
Remove the freed diaphragm and air side plate.
NOTE: Two–piece PTFE models include a PTFE diaphragm
(403) in addition to the backup diaphragm (401).
5.
Pull the other diaphragm assembly and the diaphragm
shaft (24) out of the center housing (1). Hold the shaft
flats with a 19 mm open–end wrench, and remove the
outer plate (105) from the shaft. Disassemble the
remaining diaphragm assembly.
For overmolded diaphragms: Pull the other diaphragm
assembly and the diaphragm shaft (24) out of the center
housing (1). Hold the shaft flats with a 19 mm open-end
wrench and remove the diaphragm and air side plate
from the shaft.
6.
Inspect the diaphragm shaft (24) for wear or scratches. If
it is damaged, inspect the bearings (19) in place. If the
bearings are damaged, refer to page 23.
7.
Reach into the center housing (1) with an o-ring pick and
hook the u-cup packings (402), then pull them out of the
housing. This can be done with the bearings (19) in
place.
8.
Clean all parts and inspect for wear or damage. Replace
parts as needed.
Reassembly – Standard Diaphragms
1.
Grease the shaft u-cup packings (402*) and install them
so the lips face out of the housing (1). See F
2.
Grease the length and ends of the diaphragm shaft (24)
and slide it through the housing (1).
3.
Assemble the inner diaphragm plates (104), diaphragms
(401*), PTFE diaphragms (403*, if present), and outer
diaphragm plates (105) exactly as shown in F
These parts must be assembled correctly.
4.
Apply medium-strength (blue) Loctite® or equivalent to
the threads of the fluid-side plates (105). Hold one of the
outer plates (105) with a wrench and torque the other
outer plate to 27 to 34 N•m at 100 rpm maximum. Do not
over-torque.
5.
Align the fluid covers (101) and the center housing (1) so
the arrows (A) on the covers face the same direction as
the air valve (B). Secure the covers with the screws (107
and 108), handtight. Install the longer screws (108) in
the top and bottom holes of the covers. See F
6.
First, torque the longer screws (108) oppositely and
evenly to 22–25 N•m, using a 13 mm socket wrench.
Then torque the shorter screws (107). See Diaphragm
Kits, page 29.
7.
Reassemble the ball check valves and manifolds as
explained on page 18.