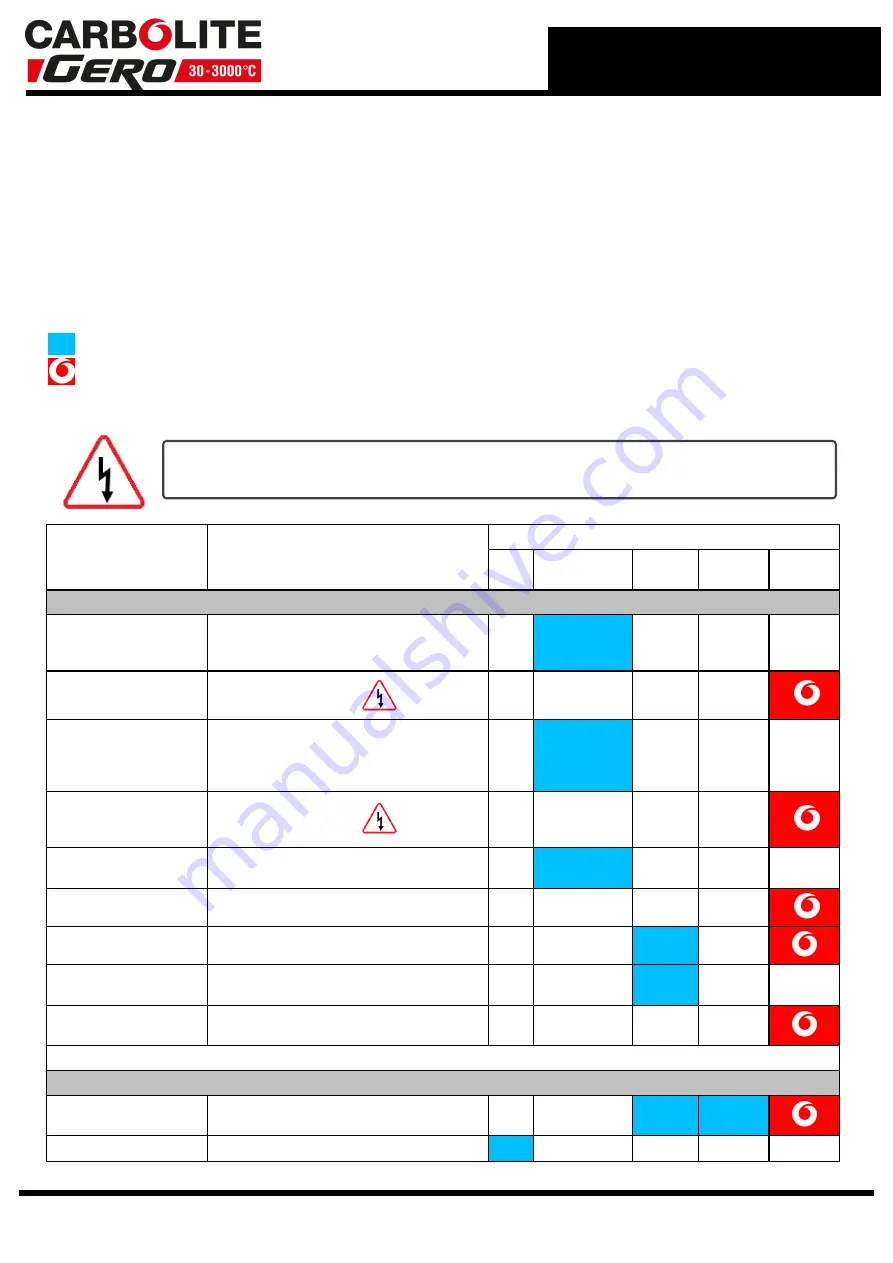
7.0
Maintenance
7.1
General Maintenance
Preventive rather than reactive maintenance is recommended. The type and frequency
depends on the product use; the following are recommended.
7.2
Maintenance Schedule
CUSTOMER
QUALIFIED PERSONNEL
DANGER! ELECTRIC SHOCK
. Risk of fatal injury. Only electrically
qualified personnel should attempt these maintenance procedures.
Maintenance
Procedure
Method
Frequency
Daily
Weekly
Monthly
Bi-
Annually
Annually
Safety
Safety Switch Function
Set a safe temperature above ambient, and
open the door to see if the heater light goes
out
Safety Switch Function
Electrical measurement
Over-Temperature
Safety Circuit
(if fitted)
Set an over-temperature setpoint lower than
the displayed temperature and check for an
over-temperature alarm as detailed in this
manual
Over-Temperature
Safety Circuit
(if fitted)
Electrical measurement
Door Plug
Visual inspection, checking the seal and
whether it is free of damage
Door Plug
Replacement where necessary
Chimney / Extraction
Check and clean if necessary
Electrical Safety
(external)
Visual check of external cables and plugs
Electrical Safety
(internal)
Physically check all connections and cleaning
of the power plate area
Function
Temperature Calibration
Tested using certified equipment, frequency
dependent on the standard required
Operational Check
Check that all functions are working normally
45
7.0 Maintenance
Summary of Contents for CARBOLITE GERO HTF 18/15
Page 36: ...4 0 3508 Dual Loop Cascade Power Limit View 36 ...
Page 55: ...Element Connections 1 phase Element Connections 3 phase 55 8 0 Repairs and Replacements ...
Page 58: ...10 0 Wiring Diagrams 10 0 Wiring Diagrams 10 1 239 4 5001 58 ...
Page 61: ...Notes Service Record Engineer Name Date Record of Work ...