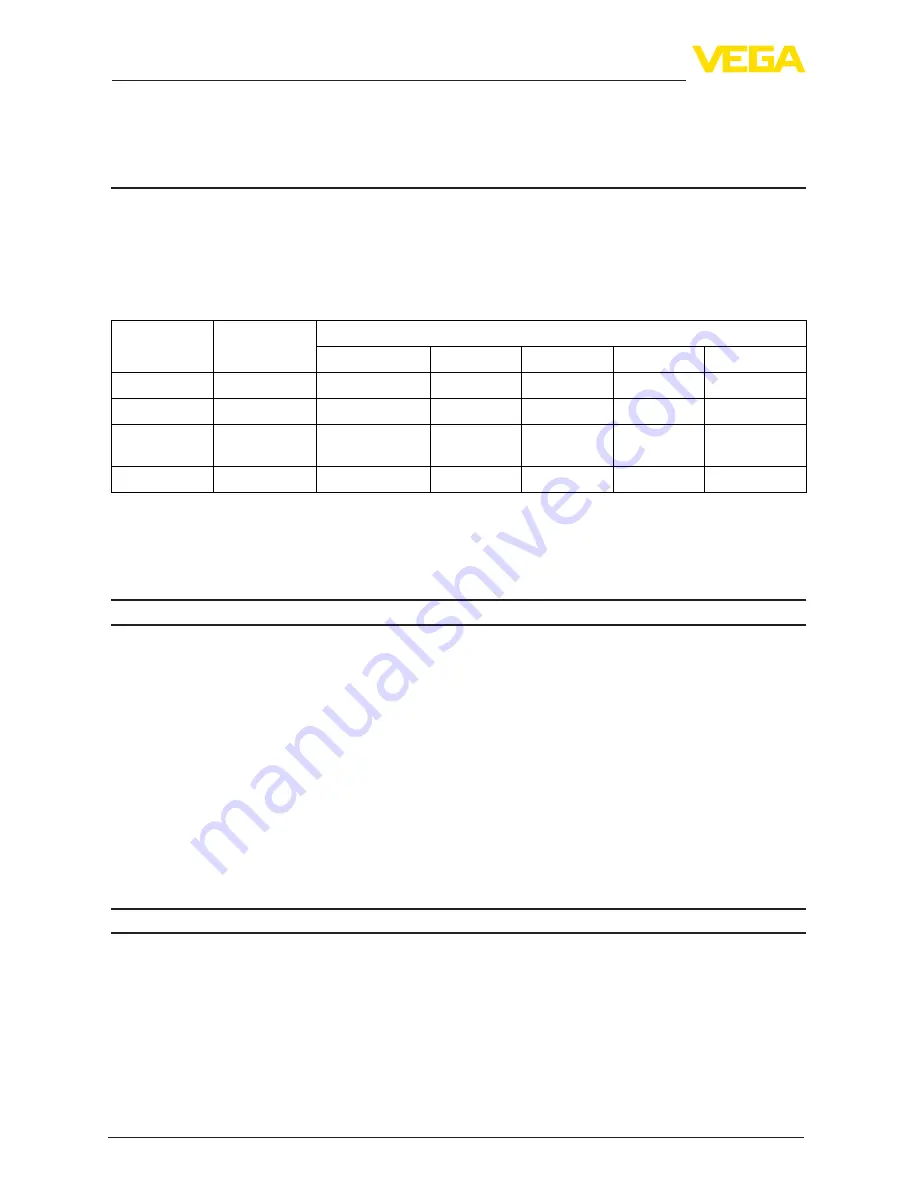
18
6 Supplement
VEGABAR 81 • Slave sensor for electronic differential pressure
48050-EN-160212
6 Supplement
6.1 Technical data
Electromechanical data - version IP 66/IP 67
Options of the cable entry
Ʋ
Cable entry
M20 x 1.5, ½ NPT
Ʋ
Cable gland
M20 x 1,5; ½ NPT (cable ø see below table)
Ʋ Blind plug
M20 x 1.5; ½ NPT
Ʋ Closing cap
½ NPT
Material cable
gland
Material seal
insert
Cable diameter
4.5 … 8.5 mm
5 … 9 mm
6 … 12 mm 7 … 12 mm 10 … 14 mm
PA black
NBR
–
●
●
–
●
PA blue
NBR
–
●
●
–
●
Brass, nickel-
plated
NBR
●
●
●
–
–
Stainless steel NBR
–
●
●
–
●
Wire cross-section (spring-loaded terminals)
Ʋ Massive wire, stranded wire
0.2 … 2.5 mm² (AWG 24 … 14)
Ʋ Stranded wire with end sleeve
0.2 … 1.5 mm² (AWG 24 … 16)
Interface to the Master sensor
Data transmission
Digital (I²C-Bus)
Connection cable to the master sensor
Ʋ Configuration
four wires, one suspension wire, one breather capillary,
screen braiding, metal foil, mantle
Ʋ
Wire cross-section
0.5 mm² (AWG 20)
Ʋ
Wire resistance
< 0.036 Ω/m (0.011 Ω/ft)
Ʋ
Standard length
5 m (16.40 ft)
Ʋ
Max. length
25 m (82.02 ft)
Ʋ Min. bending radius at 25 °C/77 °F
25 mm (0.985 in)
Ʋ Diameter approx.
8 mm (0.315 in)
Ʋ
Colour
Blue
Voltage supply for the complete system through Master
Operating voltage
Ʋ
U
B min
12 V DC
Ʋ
U
B min
- lighted display and adjustment
module
12 V DC
Ʋ
U
B max
Depending on signal output and version