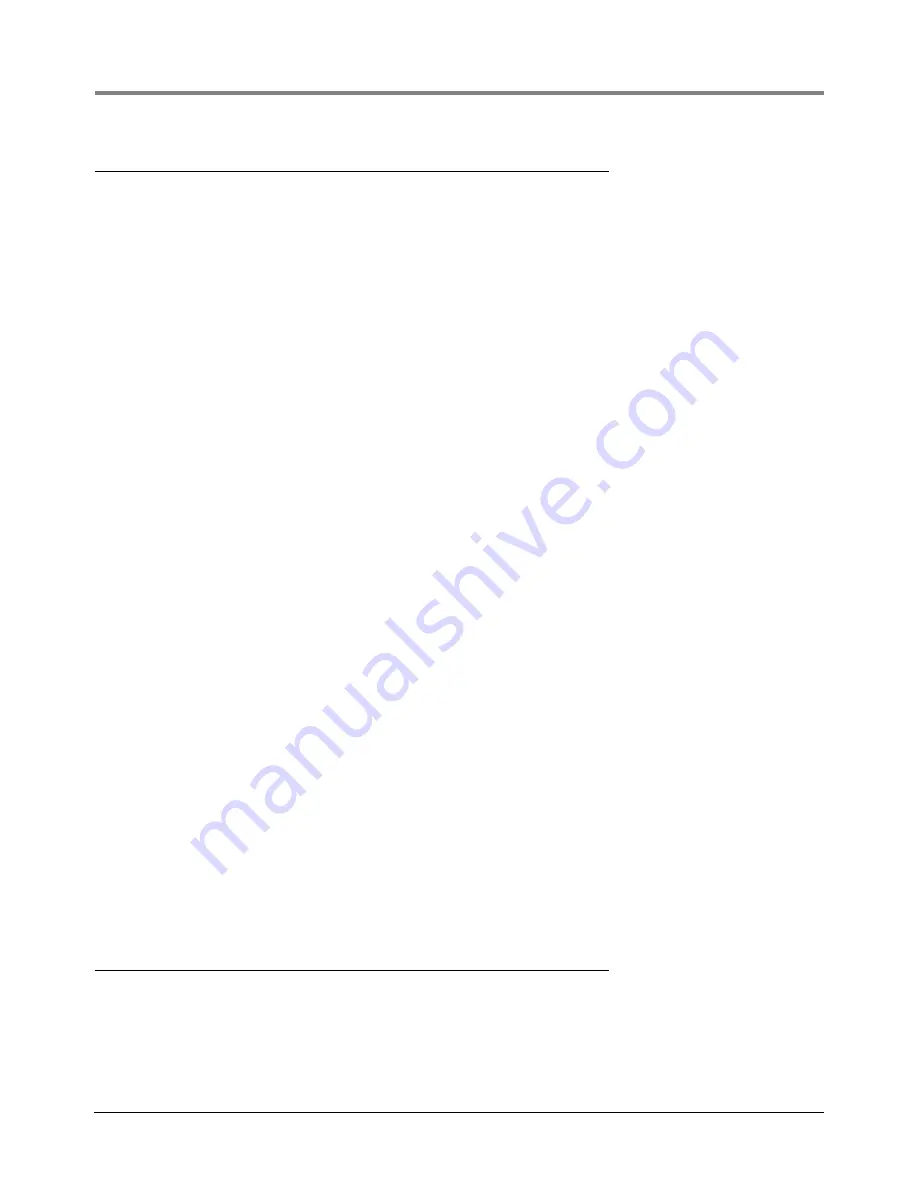
Testing Procedures
Thermal Contraction
12
Thermal Contraction
Each winter a condition may exist in which the LLD, in performing its intended purpose, reacts.
The LLD will trip and cause restricted flow when the dispenser nozzle is opened prior to the submersible pump
being turned on when line pressure is at zero. If the line pressure is above zero, the nozzle can be opened prior to
starting the submersible pump, and full flow will be received. The problem is most prevalent in self-serve ‘C’ store
type operations where the attendant is involved in the sale of various items and does not react to console requests
for operation before the nozzle is opened.
The line pressure will drop to zero every few minutes in the winter due to thermal contraction of the product in the
underground piping. Every time the line pressure drops to zero, the LLD resets to its relaxed position. The next time
the submersible pump is started, the LLD will perform a line test. The FX Series LLD takes 2-3 seconds to perform
a line test. The nozzle must be kept closed until the LLD has completed the test. The test cannot begin until the
pump is turned on. When the pump is turned on, the time interval required for the line test to begin will vary. A
mechanical dispenser may take anywhere from 7-9 seconds to reset its computer before a switch is actuated
which turns on the pump and allows the test to begin. In such cases, an electronic solenoid valve with time delay
should be installed on the flow valves of the dispenser. The delay must be set to exceed the dispenser’s reset
interval. When considering an electronic dispenser, the reset is accomplished almost instantaneously and a switch
is actuated which turns the pump on, allowing the test to begin. Even though the reset interval of an electronic
dispenser is considerably shorter than that of a mechanical dispenser, it also requires an electronic solenoid valve
installed on the flow valves to alleviate false tripping problems.
To put this in perspective, every time line pressure drops to zero, there will be an opportunity for someone to open
the nozzle prior to completion of a leak test. If this happens, the LLD will cause restricted flow because the LLD
will interpret an open nozzle as a line leak.
In the summer months, thermal contraction of the product throughout the day rarely occurs. The line pressure may
only drop to zero once a day; usually during the late night hours when the demand for product and the ambient
temperature outside are at their lowest level of the day. It should be noted that occasionally, a rain shower will cool
the pavement down enough to allow line pressure to drop to zero. However, there is usually only one opportunity
per day for someone to open a nozzle prior to starting the submersible. This usually will occur during the first
delivery of the morning.
The opportunity for the nozzle to be opened prior to completion of a line test occurs regularly in the winter,
subsequently causing the leak detector to trip, resulting in limiting flow (3 gpm [11 lpm]). This is due to the line
pressure constantly dropping to zero (which resets the LLD) throughout the day because of thermal contraction of
the product, therefore, requiring additional line tests by the LLD. Replacing LLDs, pump check valves, pump o-
rings or functional elements will not cure thermal contraction. The only cure is to be certain that the nozzle is
closed until the LLD completes the line test.
Thermal contraction is based upon a simple principle. Obviously, during the cold winter months, the temperature of
the product in the underground tank is warmer than the temperature of the underground piping, therefore, warm
product is continually pumped into cold piping. All product has a coefficient of expansion and contraction.
Gasoline has a very high coefficient of expansion and contraction. This means that a slight change in temperature
will result in a rapid volume increase or decrease. When the warm gas is allowed to sit idle in the cold piping, it
rapidly contracts, and line pressure quickly drops to zero.
Vacuum Test
At times, the effects of thermal contraction on gas are so extreme that low pressure areas are created within the
pressurized piping system. The FXT is equipped with a compound gauge which is capable of displaying psi and
inches of mercury. Therefore, if a station is experiencing slow opening times, the FXT can be used to troubleshoot
this problem by verifying the existence or non-existence of a vacuum in the piping system. This may occur
especially after long idle times in the facility such as overnight periods.