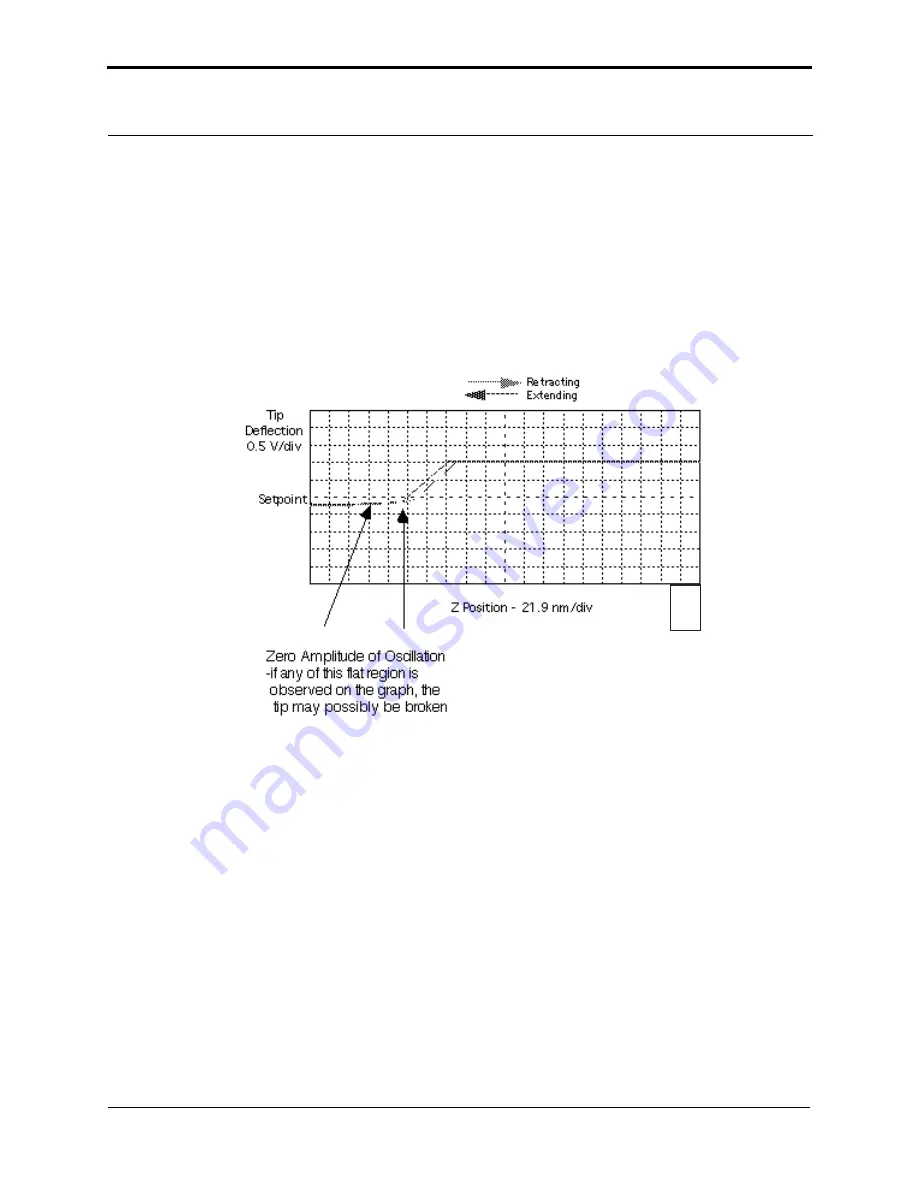
Force Imaging
Force Calibration (TappingMode)
232
Dimension 3100 Manual
Rev. D
13.5.3 High Contact Force
shows a curve produced when the tip pushes too far into the sample. The flat portion
on the left side of the amplitude curve in
occurs because the tip is so close to the
surface that it no longer vibrates. As the piezo extends the tip further, the amplitude of vibration
does not change because the tip is always in contact with the sample surface. The contact force is
very high due to the stiffness of the TappingMode cantilevers. The tip may shatter if deflection
continues.
Figure 13.5c
Amplitude Force Plot with High Contact Force
You can avoid this situation by using triggers (see
) or by reducing the value of
Z
scan start
until there is no flat portion on the left side of the curve. Rapidly increasing the value of
Z scan start
is dangerous because the total oscillation amplitude of the cantilever is small relative
to the total Z travel of the long-range scanner.
13.5.4 Tip Selection
You may use virtually any TappingMode tip to obtain TappingMode force plots; however, the
ultimate choice depends upon the delicacy of the sample and the magnitude of the forces to be
gauged. Longer cantilevers have lower spring constants (i.e., they are more pliant) and therefore
offer greater sensitivity for most samples. Shorter cantilevers afford better control when gauging
strong attractive forces and are less prone to entrapment by surface tension forces. Sharper tips are
more likely to plastically deform the sample, and are less sensitive to adhesive forces, than tips that
are more blunt. Experiment to determine the tip that best meets your needs.
3536
Summary of Contents for Dimension 3100
Page 12: ...xii Dimension 3100 Manual Rev D ...
Page 20: ...List of Figures xx Dimension 3100 Manual Rev D ...
Page 72: ......
Page 106: ......
Page 118: ......
Page 214: ...Scanning Tunneling Microscopy STM Etching Tungsten Tips 194 Dimension 3100 Manual Rev D ...
Page 222: ......
Page 266: ......
Page 274: ......