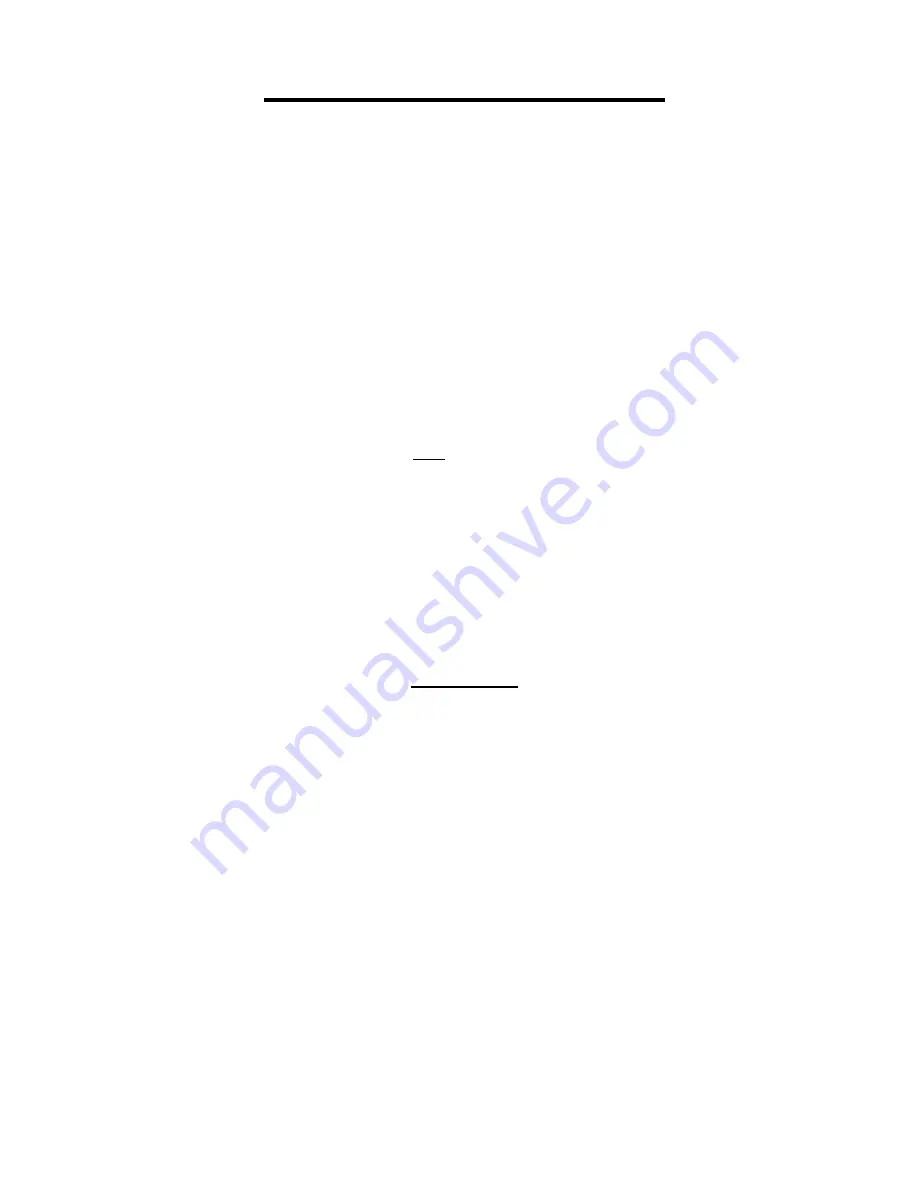
Cautions! - Warnings!
Frigoboat refrigeration systems are designed to preserve foodstuffs, drinks, and other
consumables intended for human consumption, and at normal refrigerator and freezer
temperatures. Any use other than that specified above invalidates the warranty and releases
Veco NA LLC of any liability for consequent damage, failure, malfunction, injury, illness, or
death.
Never install items containing electrical or electronic components in an area where there is the
potential for liquids to splash onto them or drip down onto them.
In the unlikely event that servicing is required, never inject anything but unadulterated pure
refrigerant R134a into any Frigoboat system. The addition of even a small amount of leak
detecting fluid, leak sealer, extra refrigerant oil, “conditioner”, flushing fluid, Thawzone, or other
substances may cause irreversible damage.
Never operate a Keel Cooled system while the boat is out of the water without having first
rigged some form of temporary water cooling on the Keel Cooler. If a Capri air cooled
condensing unit or an Air Add-On air cooled condenser is installed together with a Keel
Cooler, ensure that the fan is operated only when the boat is out of the water, and then
switched off when the boat is launched.
Never defrost an evaporator using a hard or sharp object like an ice pick, knife, or screwdriver.
Never defrost using an appliance that generates high heat, like a heat gun or hairdryer. Natural
defrosting is safest, but mild heat may be used if absolutely necessary.
With a Keel Cooler installation, it is vital that the Keel Cooler be electrically connected
to a
point that is at the same potential as the boat’s battery negative,
with no switch in the circuit
between the Keel Cooler connection and the battery negative.
Contents
Chapter 1 Frigoboat Systems
Chapter 2 Paris 35F, Capri 35F, Capri 50F - Air cooled
Chapter 3 W35F, W50F - Water cooled with pump
Chapter 4 K35F, K50F - Water cooled with Keel Cooler
Chapter 5 Danfoss or Secop Electronic Controller for Frigoboat systems
Chapter 6 Aluminum H-, F- and B-Type Evaporators (Horizontal, Flat, Bin)
Chapter 7 Mechanical thermostat for H-, B-, and F-evaporators
Chapter 8 Spillover Kit Installation Instructions
Chapter 9 Quick Connect Refrigerant Fittings
Chapter 10 Electrical
Chapter 11 Troubleshooting Guide