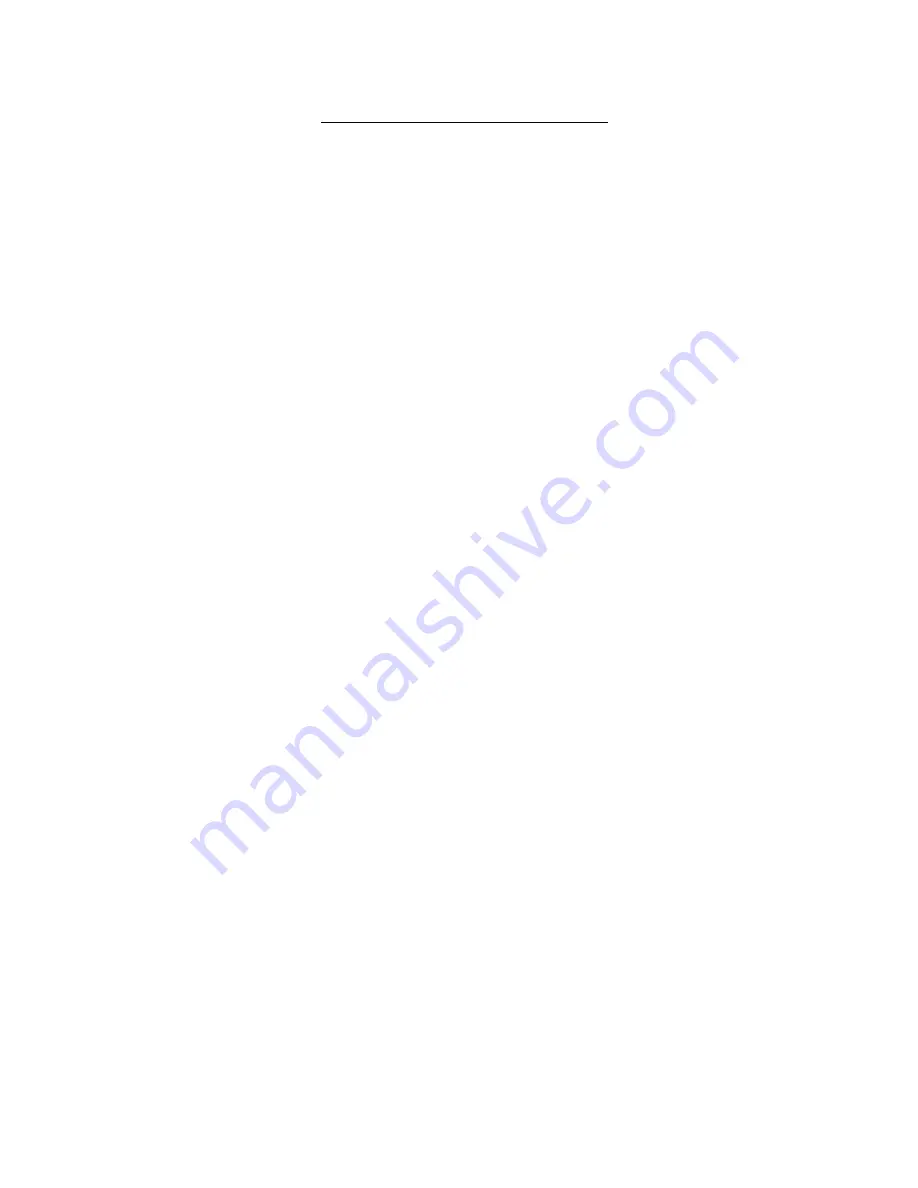
Chapter 9
Quick Connect Refrigerant Fittings
Each component of a Frigoboat system is fitted with one male and one female proprietary Quick
Connect fitting that connects to a corresponding fitting on other components of the system. The Keel
Cooler systems are comprised of three components, and special attention is required to avoid incorrect
connections. The refrigerant tubes are color coded with red, yellow, and blue tape, and matching the
colored tags will ensure correct connections. (The red plastic tubing on the Keel Cooler is to be
considered as a red marker). If a Keel Cooler is to be connected to an air cooled condensing system in
place of a K35 or K50, match the two blue tagged couplings first, then connect the red tagged tube on
the Capri to the yellow tagged tube on the Keel Cooler. Finally, connect the red plastic covered tube
from the Keel Cooler to the red tagged tube on the evaporator. All other air and water-cooled systems
have only two components, each with a male plus a female fitting, and therefore they cannot be
connected incorrectly.
The individual items are pre-charged with the correct amount of refrigerant at the factory. When the
Quick Connect fittings are joined together, they allow the refrigerant to flow through the system
without leaking out into the atmosphere
.
If needed, they can be uncoupled without loss of refrigerant
in order to re-run refrigerant lines, upgrade components or enable a faulty component to be removed
and replaced. When they are uncoupled, immediately install dust plugs, (removed when originally
installed and kept in a safe place) into the exposed female/male fittings.
Note: Never run compressor unless all components of system are correctly connected together.
9:1
Connecting the Quick Connect fittings
Leave the dust plugs installed until the very last moment when you are ready to connect the system
together. Once the dust caps have been removed, it is imperative that the exposed components and
surfaces be kept free of dust, dirt, construction debris, etc. After you have removed the plugs, keep
them in a safe place in case you need to remove or replace a component later.
Push the male and female fittings together and then carefully rotate the collar on the female fitting
until it starts to thread onto the male thread, making sure that the fitting is not cross-threaded, the male
end does not rotate, and the O-ring remains seated in its groove. Do not use any thread sealant or tape.
Continue rotating the collar of the female end, either by hand or with a 15/16" or adjustable wrench,
while preventing the male end from rotating by restraining it with a 13/16" or adjustable wrench
. It is
most important not to let the male end rotate at all during this whole process.
Tighten the collar until it completely covers the threads on the male fitting and then make it “snug”
with wrenches. Excessive tightening is not required, as the O-ring makes the seal and making up the
threads simply opens the internal valves and allows refrigerant to flow. If resistance is felt before the
threads are covered, back off the collar and ensure that the shaft in the female coupling has not been
mis-aligned. If it has, straighten it and re-make the coupling.
If there is a continuous hiss after the connection has been completed, quickly disconnect the fitting and
check that the O-ring has not been damaged or unseated. If it has, carefully re-seat it or replace it with
one of the spares provided that are taped to the compressor, and then re-make the fitting.
NOTE: The spare O-rings provided as a convenience for use if any get damaged during system
installation. They are NOT provided for use as routine replacements, and the original O-rings
should never require replacement if the systems are installed and operated as designed.