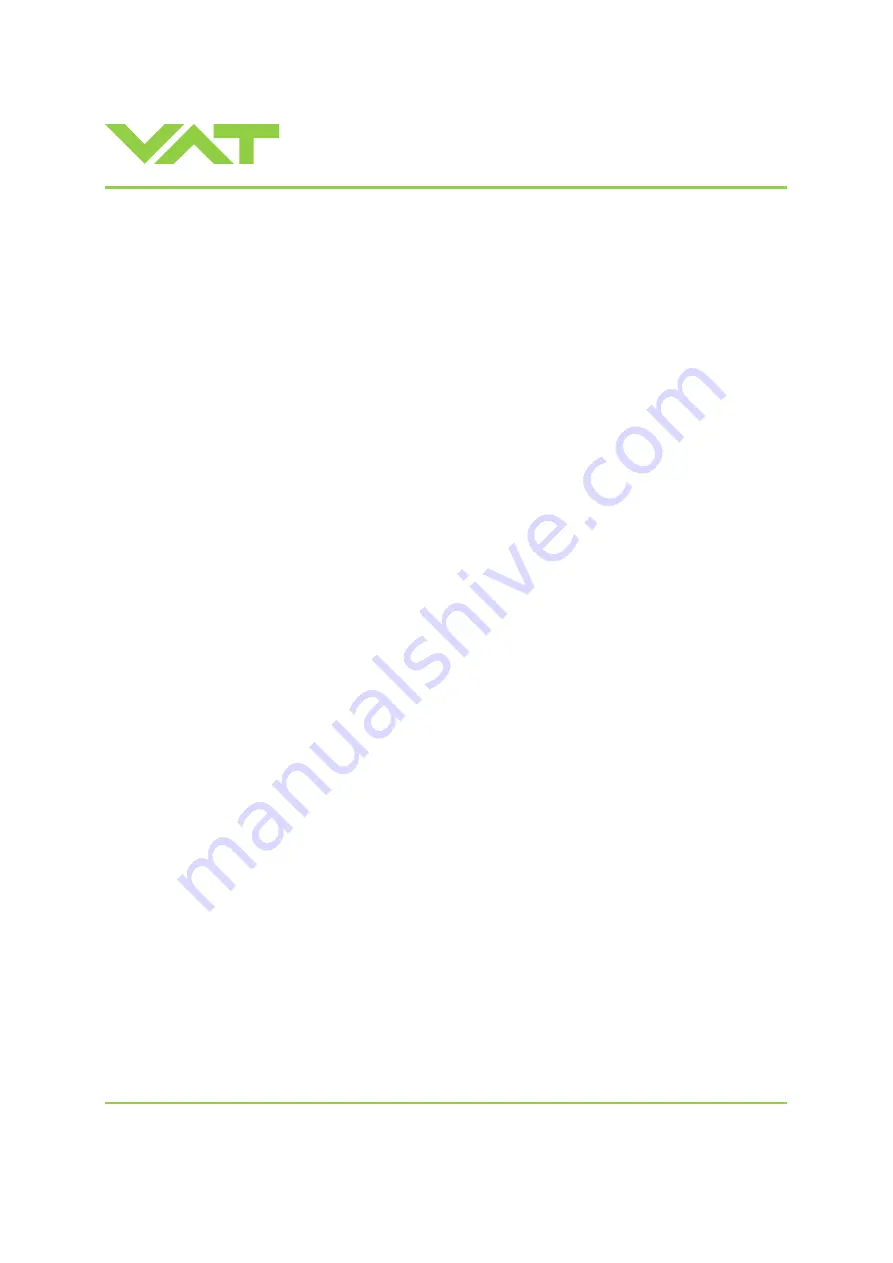
Installation, Operating & Maintenance Instructions
Series 612 DN 63-250 (I.D. 2.5“ - 10”), RS485
VAT Vakuumventile AG, CH-9469 Haag, Switzerland
Tel +41 81 771 61 61 Fax +41 81 771 48 30 [email protected] www.vatvalve.com
289857EA
2011-07-13
4/76
5
Maintenance & repairs ............................................................................................................................................ 60
5.1
Maintenance procedures ............................................................................................................................... 61
5.2
Option board .................................................................................................................................................. 66
5.2.1
Durability of power fail battery ........................................................................................................... 66
5.2.2
Retrofit / replacement procedure ....................................................................................................... 67
6
Drawing................................................................................................................................................................... 70
7
Spare parts ............................................................................................................................................................. 71
7.1
Control and actuating unit.............................................................................................................................. 71
7.2
Seals and grease ........................................................................................................................................... 71
7.3
ISO-F valve unit - aluminum blank, without heating....................................................................................... 72
7.4
Accessories ................................................................................................................................................... 73
7.4.1
Centering ring with Viton o-ring ......................................................................................................... 74
8
Warranty ................................................................................................................................................................. 75