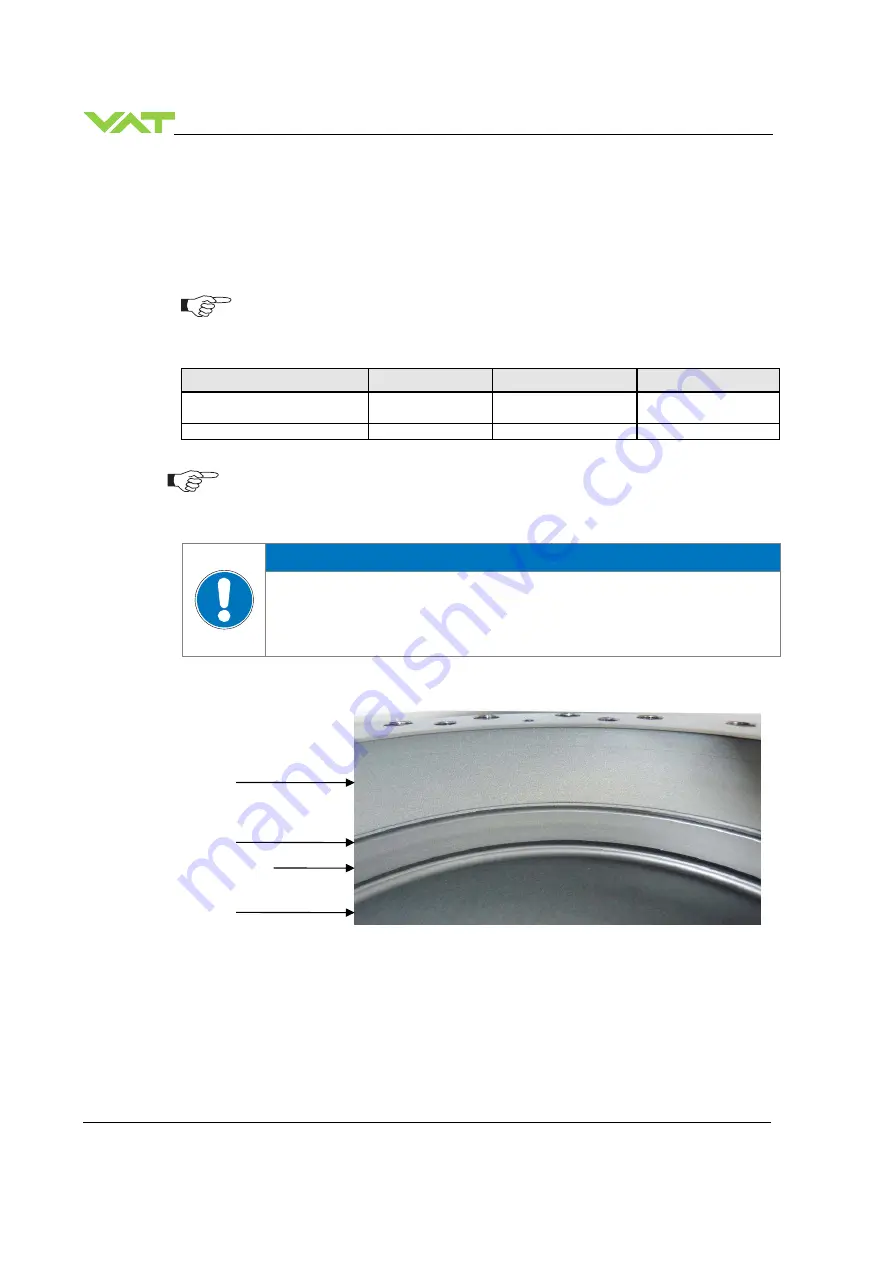
MAINTENANCE
Series 65
86/110
Edition 2019-06-05
982156EB
7.2
Maintenance procedures
Two maintenance procedures are defined for this valve. These are:
•
Replacement of isolation seals (gate and body seal of sealing ring) and valve cleaning
•
Replacement of actuator shaft seals
Required frequency of cleaning and replacement of seals is depending on process
conditions.
VAT can give the following recommendations for preventive maintenance:
Replacement of
unheated
1)
heated
≤
80 °C
1)
heated > 80 °C
1)
isolation seals (gate and
body seal of sealing ring)
12 month but max.
200’000 cycles
6 months but
max. 200’000 cycles
3 months but
max. 200’000 cycles
actuator shaft seals
1’000’000 cycles
6 months
3 months
1)
Those figures are reference values for clean conditions under various temperatures.
These values do not include any impact of the process. Therefore preventive
maintenance schedule has finally to be checked for the actual process conditions.
NOTICE
Vacuum grease
Vacuum grease may be distributed and contaminate the valve.
Prevent gap between body and sealing ring from air gun cleaning. Do not clean the
gap between body and sealing ring with compressed air.
See figure below:
Body
Gap
Sealing ring
Plate