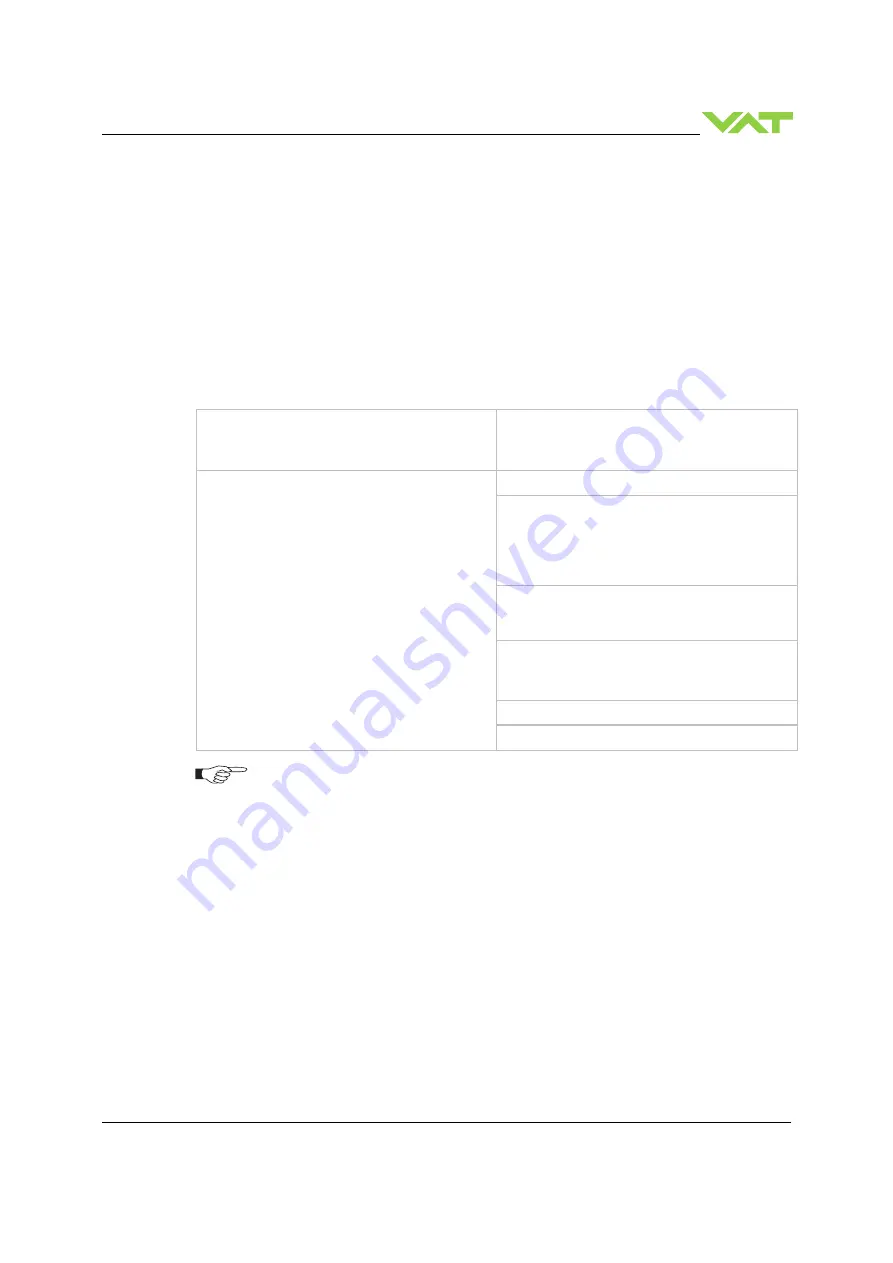
Series 642
INSTALLATION
605593EC
Edition 2017-11-24
37/113
4.6.7
LEARN (adaptive)
LEARN adapts the PID controller of the valve to the vacuum system and its operating conditions. LEARN
must be executed only once during system setup. The LEARN routine determines the characteristic of
the vacuum system. Based on this, the PID controller is able to run fast and accurate pressure control
cycles.
This characteristic depends on various parameters such as chamber volume, conductance and flow
regime. Therefore it must be performed with a specific gas flow according to instruction below.
The result of LEARN is a pressure versus valve position data table. This table is used to adapt the PID
parameters. The data table is stored in the device memory which is power fail save. The data table can
be up-/downloaded via ‘Control Performance Analyzer’ software or remote interface. Due to encoding the
data may not be interpreted directly.
By an OPEN VALVE, CLOSE VALVE, POSITION CONTROL or PRESSURE CONTROL command the
routine will be interrupted.
Local operation:
(‘Control View’, ‘Control Performance Analyzer’ or
‘Service Box 2‘)
Remote operation:
(Refer to chapter «Explicit messaging control
commands» resp. «Explicit messaging setup
commands» for details)
Go to ‘Learn / LEARN’ menu and follow
instructions.
Gasflow calculation according to
recommendation below is done automatically
based on inputs.
1. Send OPEN VALVE
2. Set specific gas flow according to calculation
below and wait until flow is stable.
LEARN does not need to be performed with
the process gas. Instead N
2
or Ar may be
used.
3. Set SETPOINT ( = pressure limit for learn) to
p
max
(max. pressure to control during
process)
4. Set LEARN
Alarm (VALVE STATUS) is set as long learn
is performed, if alarm is off, learn is finished.
5. Reset LEARN
6. Reset OPEN VALVE
Sensor signal must not shift during LEARN. Wait until sensor signal is stable before
LEARN is performed. Learn may take several minutes. Do not interrupt the routine as
a single full run is required to ensure fast and accurate pressure control. The
PID controller covers 5% to 5000% of the gas flow which was used for learn.