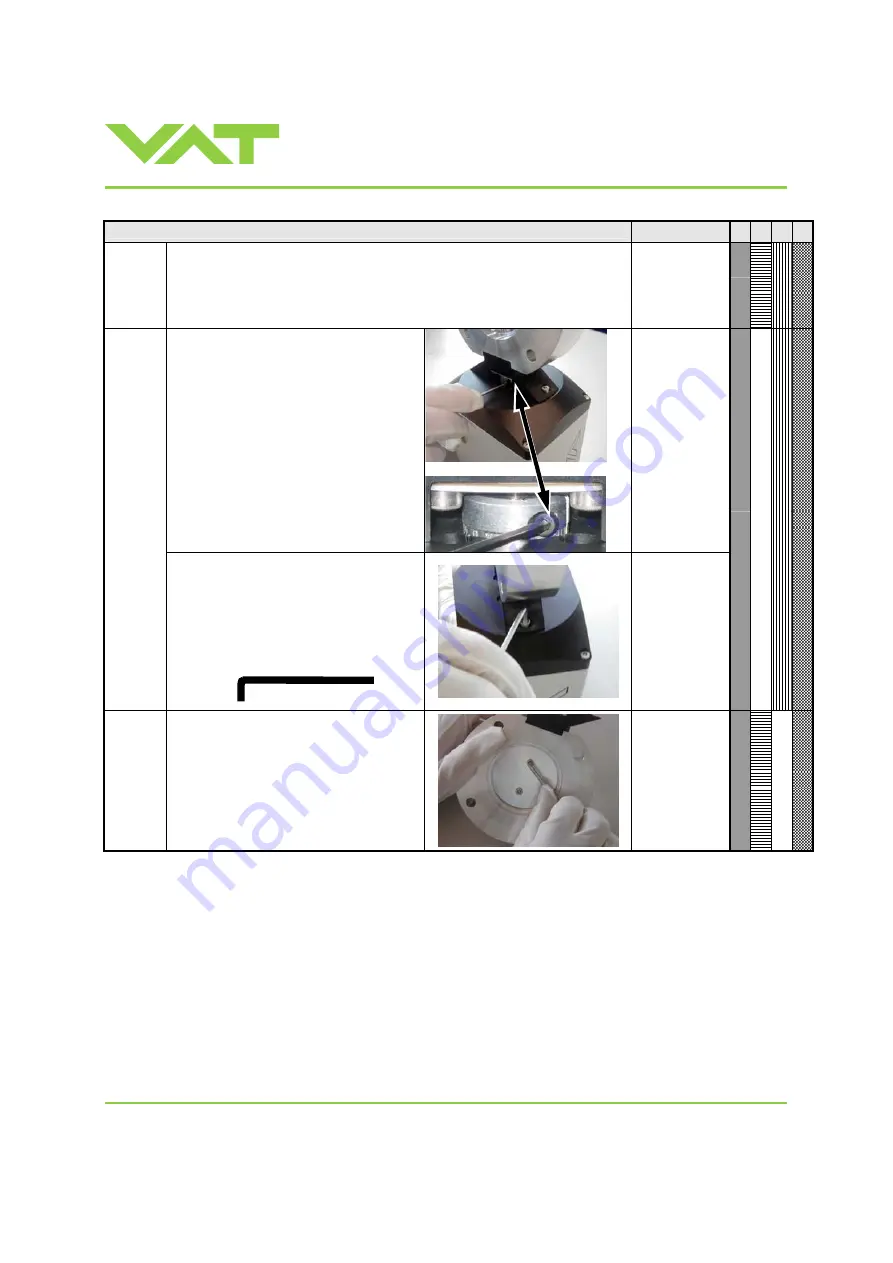
Installation, Operating & Maintenance Instructions
Series 612 DN 25 (I.D. 1”), Logic
VAT Vakuumventile AG, CH-9469 Haag, Switzerland
Tel +41 81 771 61 61 Fax +41 81 771 48 30 [email protected] www.vatvalve.com
289700EB
2011-10-21
44/57
Description
Required tool
Re
m
o
v
e
val
v
e fr
om
system
1. Vent vacuum system, disconnect electrical connections and remove valve
from vacuum system.
Note: You do not need to remove the valve from the vacuum system to
replace the control and actuating unit.
Depending on
flange screws
2. Unfasten clamp coupling.
Note: If you can not access the coupling
screw, turn plate by hand until you can
access the coupling screw with Allen
Wrench.
Allen Wrench
2mm
Re
m
o
ve
cont
ro
l and actua
ti
ng
un
it
fr
om val
v
e
uni
t
3. Unfasten the 2 connection bolts and
separate both parts.
Note: Valve size DN 160 (6”) and bigger
require a shortened wrench.
For ordering number refer to «Spare
parts and accessories».
Allen Wrench
3mm
R
e
move p
lat
e
4. Unfasten screws and remove plate
from shaft.
Allen Wrench
3mm
12 mm