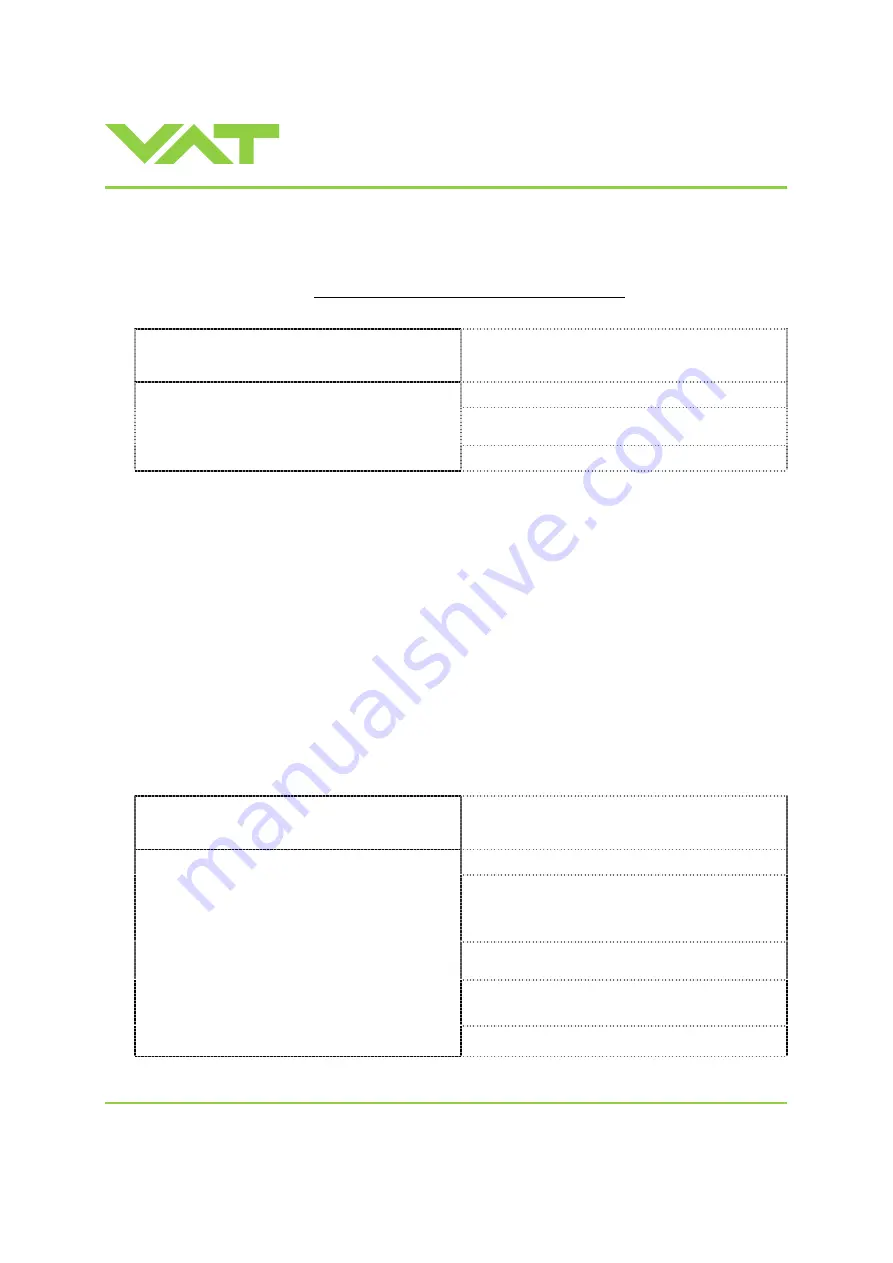
Installation, Operating & Maintenance Instructions
Series 612 DN 25 (I.D. 1”), Logic
VAT Vakuumventile AG, CH-9469 Haag, Switzerland
Tel +41 81 771 61 61 Fax +41 81 771 48 30 [email protected] www.vatvalve.com
289700EB
2011-10-21
25/57
3.6.3 ZERO
ZERO allows for the compensation of the sensor offset voltage.
When ZERO is performed the current value at the sensor input is equated to pressure zero. In case of a 2 sensor system
both sensor inputs will be adjusted. A max. offset voltage of +/-1.4V can be compensated. The offset value can be read
via local and remote operation.
Local operation
:
(‘Control View’, ‘Control Performance Analyzer’ or
‘Service Box 2‘)
Remote operation
:
(Refer to chapter: «Functions and Wiring» > «Digital
inputs» for details)
1. Send
OPEN
VALVE
2. Wait until process chamber is evacuated and
sensor signal is not shifting anymore.
Go to menu ‘Zero / ZERO’ and follow instructions.
3. Send
ZERO
Note: Do not perform ZERO as long as pressure gauge voltage is shifting otherwise incorrect pressure reading is the
result. Refer to manual of sensor manufacturer for warm up time.
Note: Do not perform ZERO, if the base pressure of your vacuum system is higher than 1‰ of sensor full scale. We
recommend disabling ZERO function in this case; refer to «Valve configuration» of the setup procedure. Otherwise
incorrect pressure reading is the result.
3.6.4 LEARN
LEARN adapts the PID controller of the valve to the vacuum system and its operating conditions. LEARN must be
executed only once during system setup.
The LEARN routine determines the characteristic of the vacuum system. Based on this, the PID controller is able to run
fast and accurate pressure control cycles.
This characteristic depends on various parameters such as chamber volume, conductance and flow regime. Therefore it
must be performed with a specific gas flow according to instruction below.
The result of LEARN is a pressure versus valve position data table. This table is used to adapt the PID parameters. The
data table is stored in the device memory which is power fail save. The data table can be up-/downloaded via ‘Control
Performance Analyzer’ software or remote interface. Due to encoding the data may not be interpreted directly.
By an OPEN VALVE, CLOSE VALVE, POSITION CONTROL or PRESSURE CONTROL command the routine will be
interrupted.
Local operation
:
(‘Control View’, ‘Control Performance Analyzer’ or
‘Service Box 2‘)
Remote operation
:
(Refer to chapter «Digital inputs» for details)
1. Set OPEN VALVE
2. Set specific gas flow according to calculation
below and wait until flow is stable.
Autolearn does not need to be performed with
the process gas. Instead N
2
or Ar may be used.
3. Set SETPOINT ( = pressure limit for learn) to p
max
(max. pressure to control during process)
4. Set
LEARN
Note: Alarm is set as long learn is performed, if
alarm is off, learn is finished.
Go to ‘Learn / LEARN’ menu and follow instructions.
Note: Gasflow calculation according to
recommendation below is done automatically based
on inputs.
5. Reset
LEARN
6. Reset
OPEN
VALVE