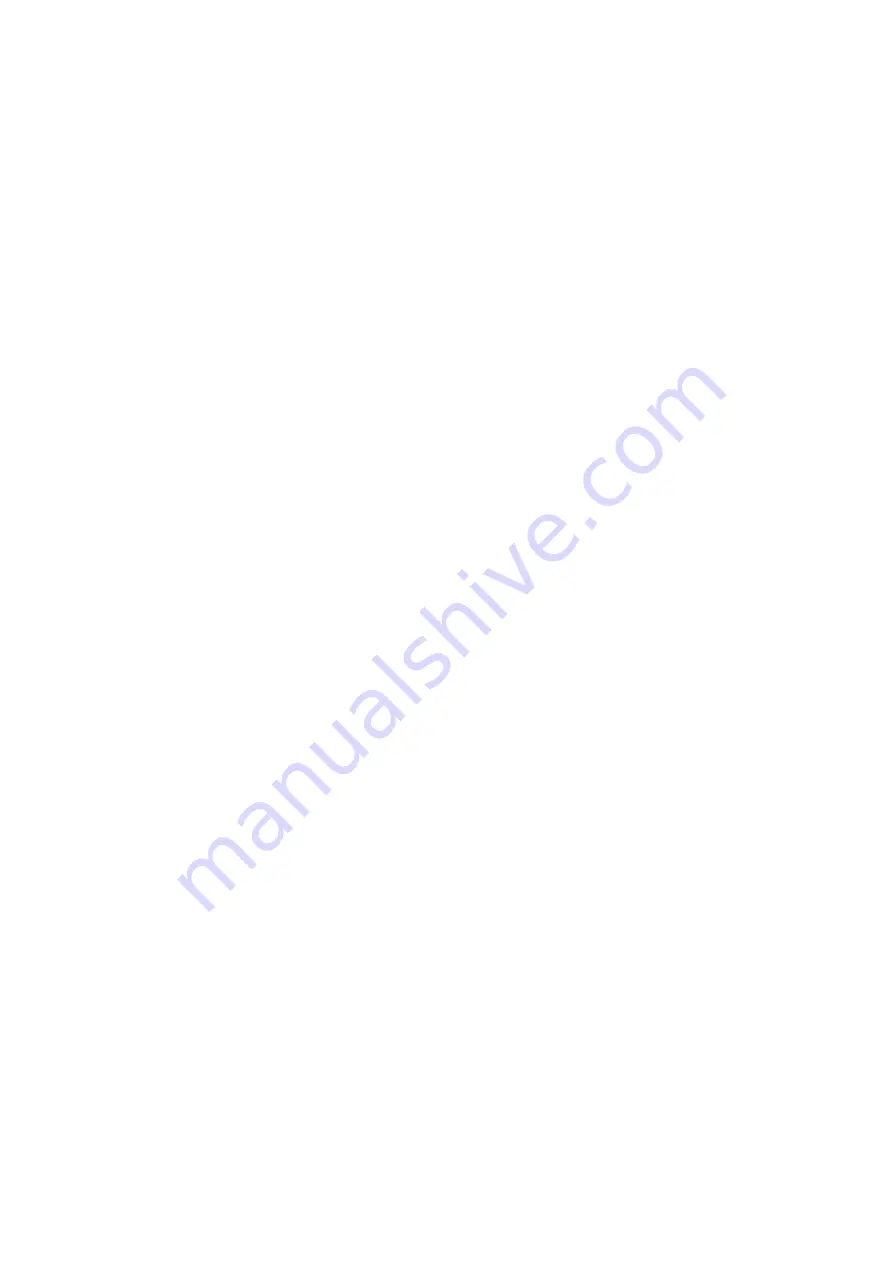
13
MAINTENANCE
Before maintenance is carried out, the pump must be stopped and the power supply disconnected. The supply must only be
switched back on by the operator performing maintenance.
Warning:
residual liquid may be found in the pump casing, head and suction line. Comply with safety procedures for the handling of
hazardous liquids (flammable, corrosive, poisonous, infected etc.).
13.1 Inspection and checks
Check the pump is working correctly at regular intervals. Use the instruments installed in the system (pressure gauge, vacuum gauge,
ammeter etc.) to check the pump is still fit for duty.
We recommend periodic maintenance of the various parts subject to wear, particularly the impeller and wear plate.
13.2 Replacing the impeller (fig. 9)
- Drain the pump casing as indicated in section 7.1
-
Warning:
residual liquid may be found in the pump casing, head and suction line. Comply with safety procedures for the handling of
hazardous liquids (flammable, corrosive, poisonous, infected etc.).
- Drain the seal’s oil by unscrewing drain plug 5 (fig. 7a).
- Unscrew the screws (47) and remove the rotating unit made up of the impeller (03), head (19), support (06) and shaft (07)
- Block the impeller (03), unscrew the screw (33) and remove the ogive piece (66) for series ST-R2, R3 and R8; for ST-R4 and R6, remove
the Belleville washer (33.1).
- Remove the impeller and replace it with a new one
- To reassemble, repeat the procedure in reverse
- Make sure the impeller is positioned accurately with respect to the wear plate, as indicated in point 13.7.
13.3 Replacing rear wear plate (fig. 9)
- Drain the pump casing as indicated in section 7.1
-
Warning:
residual liquid may be found in the pump casing, head and suction line. Comply with safety procedures for the handling of
hazardous liquids (flammable, corrosive, poisonous, infected etc.).
- Drain the seal’s oil by unscrewing drain plug 5 (fig. 7a).
- Remove the impeller (03) as described in section 13.2
- Unscrew the screws (57.1) securing the head (19)
- Replace the plate (02.1)
- To reassemble, repeat the procedure in reverse.
13.4 Replacing front wear plate (fig. 9)
-
Drain the pump casing as indicated in section 7.1
-
Warning:
residual liquid may be found in the pump casing, head and suction line. Comply with safety procedures for the handling of
hazardous liquids (flammable, corrosive, poisonous, infected etc.).
-
Unscrew the bolts (53.2) and remove the cover (26)
-
Unscrew the nuts (57.2)
-
Remove and replace the wear plate (02)
-
To reassemble, repeat the procedure in reverse.
-
Make sure the impeller is positioned accurately with respect to the wear plate, as indicated in point 13.7.
13.5 Replacing the valve (fig. 9)
- Drain the pump casing as indicated in section 7.1
-
Warning:
residual liquid may be found in the pump casing, head and suction line. Comply with safety procedures for the handling of
hazardous liquids (flammable, corrosive, poisonous, infected etc.).
- Unscrew the bolts (53.2) and remove the cover (26)
- Grip the valve (14.1) with your hand inside the pump casing and unscrew the supporting screw
- Slip off the valve (14.1) and replace it
- To reassemble, repeat the procedure in reverse.
13.6 Replacing the seal (figs. 9-10)
- Drain the pump casing as indicated in section 7.1
-
Warning:
residual liquid may be found in the pump casing, head and suction line. Comply with safety procedures for the handling of
hazardous liquids (flammable, corrosive, poisonous, infected etc.).
- Drain the seal oil by unscrewing drain plug 5 (fig. 7a).
- Unscrew the screws (47) securing the mount (06)
- Remove the mount (06) complete with impeller and head from the pump casing (01)
- Remove the impeller (03) as described in section 13.2
- Slip off the rotating part of the seal (40) with the shaft sleeve (31) (fig. 10)
- Unscrew the nuts (57.2) and remove the head (19) with the fixed part of the seal fitted (38-39) (fig. 10)
- Slip the seal’s stationary seal (38-39) (fig. 10) off the head (19)
- Wash the seal’s seat in the head (19) and in the shaft sleeve (31) (fig. 10) with solvent
- Fit the stationary seal (39) complete with gasket (38). To make the operation easier, grease the seat and gasket. If necessary, use a
wooden plunger or similar tool to push the stationary seal (39) into the seat in the head (19)
- Secure the head (19) to the mount (06) using the nuts (57.2)
- Smear the seal (40) and shaft sleeve (31) with oil and slip the rotating part of the seal onto one end of the shaft sleeve
-
Slip the whole assembly onto the shaft and push to overcome the slight resistance offered by the lip seal (41).
-
Be careful the seal does not slip off the shaft sleeve.
-
Slip on the seal support ring (25.1). Push it forward until the key (60) can be reassembled
-
Refit the impeller (03), ogive piece (66) and tighten the screw (33) for series ST-R2, R3 and R8; for ST-R4 and R6, refit Belleville washer
33.1 (fig. 9)
-
Make sure the impeller is positioned accurately with respect to the wear plate, as indicated in point 13.7.
-
Refit the casing and fasten the nuts, making sure the impeller is free to turn.
8