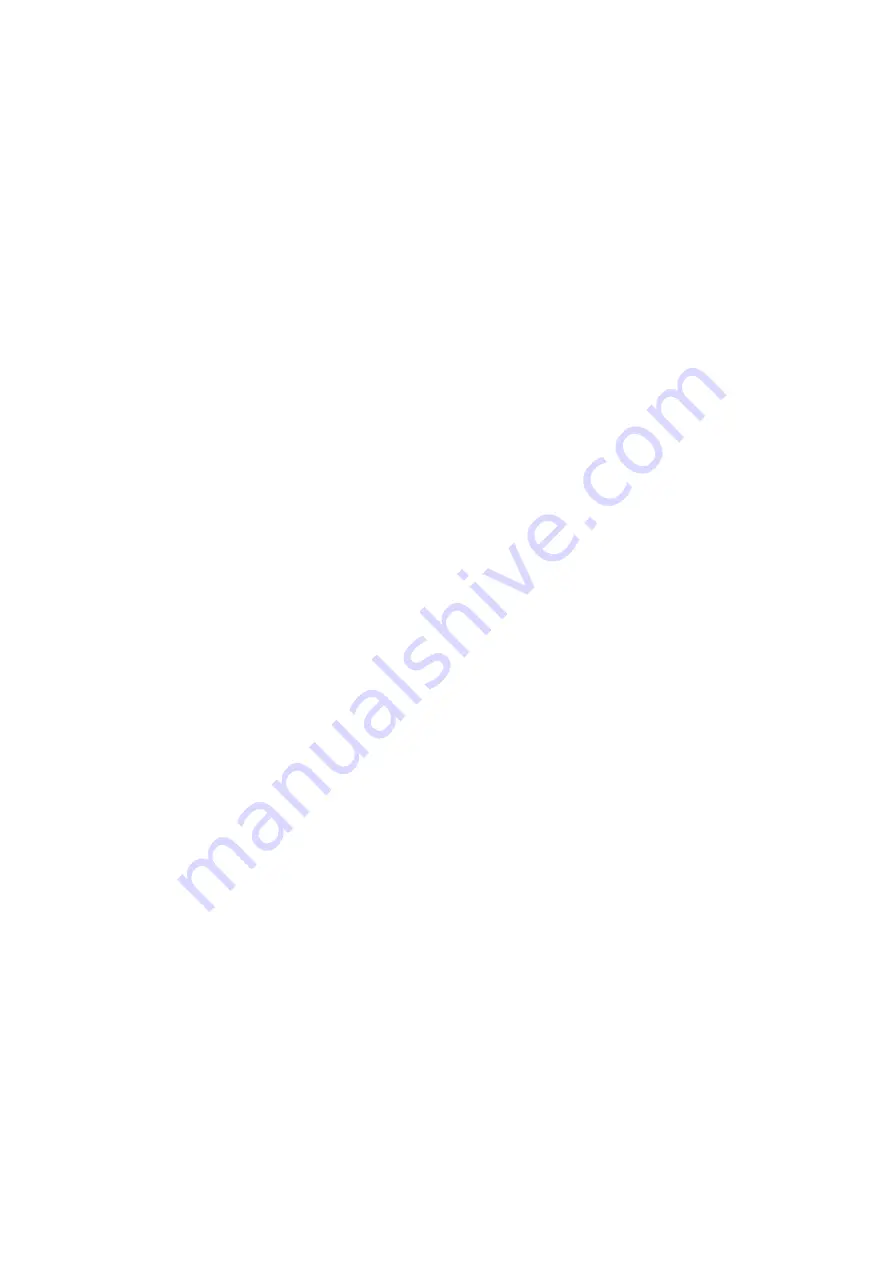
14.8 BEARINGS DO NOT LAST
33 lack of lubrication
lubricate bearings as described in section 13.8
34 foreign matter in bearings
replace bearings as described in section 13.9
35 bearings are rusted
replace bearings as described in section 13.9
14.9 THE SEAL LEAKS
36 poor lubrication
Check oil level.
If the pump leaks during operation, the seal must be replaced. (see section 13.6)
14.10 RUBBER PARTS OF COUPLING WEAR DOWN QUICKLY
Check unit is correctly aligned as described in section 10 and follow the replacement procedure given in sections 13.10, 13.11 and 13.12.
15
RESIDUAL HAZARDS
Residual risks are any risks that cannot be eliminated through pump design:
-
knocks
-
anomalous pressure rises
-
misuse
-
manoeuvring errors in the pump’s vicinity.
16 REPAIRS
Before carrying out repairs on the unit, it is essential to:
-
disconnect mains power (see section 13) or switch off the internal combustion engine
-
close the pump’s suction and delivery gate valves
-
if the liquid pumped is hot, allow the pump to cool down to ambient temperature
- drain liquid pumped from pump casing as indicated in section
-
remove and clean, removing any liquid pump still inside, complying with safety procedures for the handling of hazardous liquids
(flammable, corrosive, poisonous, infected etc.).
17
DISASSEMBLY
17.1 DISASSEMBLING PUMP FROM SYSTEM
Follow procedure given in section 16.
-
Remove nuts securing the suction and delivery flanges
-
Remove bolts fastening the pump to the base plate
-
Pull the pump from the coupling, if there is one, or remove it from the engine
-
Before lifting the pump using the lifting hook (83.1 fig. 9) with appropriate means, refer to the pump weights table.
18
ASSEMBLY
18.1 ASSEMBLING PUMP ON SYSTEM
-
Lift the pump using the lifting hook (83.1 fig. 9) with appropriate means
-
Place pump on the base plate
-
Restore connections with the coupling or engine, as applicable
-
Check alignment as described in section 10
-
Fasten pump to the base plate
-
Connect pump to pipework
-
Refit any coupling guards.
19
SPARE PARTS
To assure the pump's lasting efficiency, it is advisable, when ordering the unit, to purchase the spare parts recommended for the first
maintenance operation:
-
impeller
-
seal
-
front and rear wear plates
-
complete set of gaskets
-
check valve
-
self-locking impeller nut.
19.1 Ordering spare parts
To order spare parts, specify the following:
-
type of pump
-
the pump’s serial number
-
reference number and description of the part as shown in the exploded drawing.
20
DISPOSAL
-
Do not release to the environment.
-
Metal parts can be recycled as scrap.
-
Greases and oils should be recovered, stored and disposed of through approved agencies in accordance with the regulations in force.
-
Elastomer gaskets must be kept separate and disposed of through an authorized waste disposal agency.
12