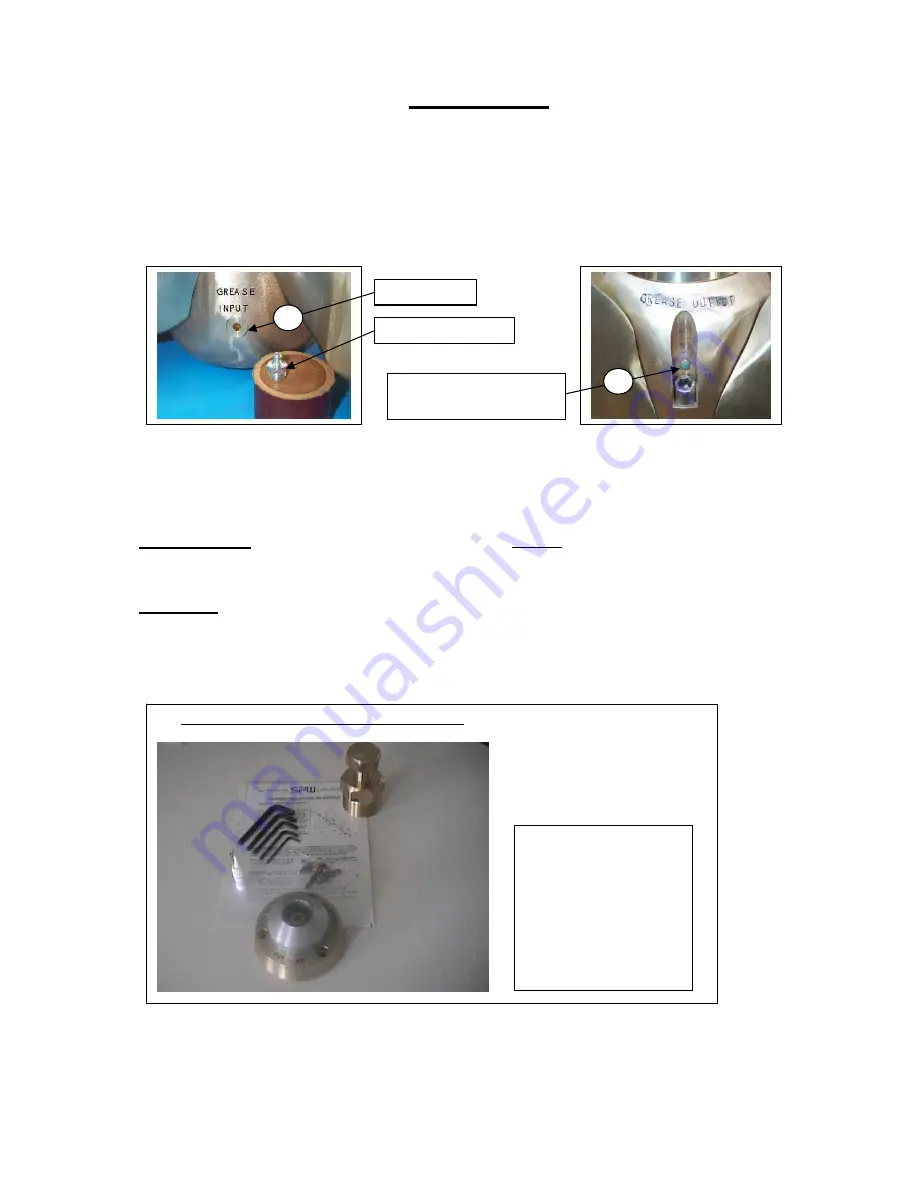
Formular-Nr.:71 Rev.-Nr.:07 03/18
-9-
SERVICING
The VARIPROP needs to be greased up a minimum of every 2 – 3 years, depending on the engine hours
run, or whenever the boat is hauled. The VARIPROP body should always be completely filled with a high
viscosity
grease
of a hydrophobic nature. Remove the cap screw
(5)
and screw in the lubricating nipple
which is supplied with the tools. Remove the “grease out“ screw
(6)
. During filling with grease rotate the
propeller from forward stop to reverse stop to allow the grease to work through the propeller. Stop to pump
when grease comes out at the opened “grease out “ port.
Factory supplied special grease EP/SAL is recommended and available from your VARIPROP distributor.
Avoid regular white grease (sterntube-grease ) !
Shock-absorber:
The integrated hydraulic shock-absorber reduces unpleasant operating noises. The pitch
stops are substantially protected against wear. At rotating the blades by hand, you can feel the shock-
absorber function. This “heavy” turning at the absorber area is normal and necessary for the function !
Zinc anode:
Make sure that you always keep the zinc anode in good condition. The VARIPROP must be
protected by a lot of zinc, so also use a zinc anode onto the shaft if possible. Use fine sandpaper to clean the
aft of the end boss and the forward face of the Variprop-anode to give the zinc good contact with the
propeller.
Cap - screw
Stop greasing if grease
comes out here!
Tools supplied with your VARIPROP DF-160:
lubrication nipple
1x Manual
1x puller system
1x allen key 3mm
1x allen key 4mm
1x allen key 6mm
1x allen key 8mm
1x grease nipple G1/4”
1x small plastic bottle
with Loctite low (pink)
6
5