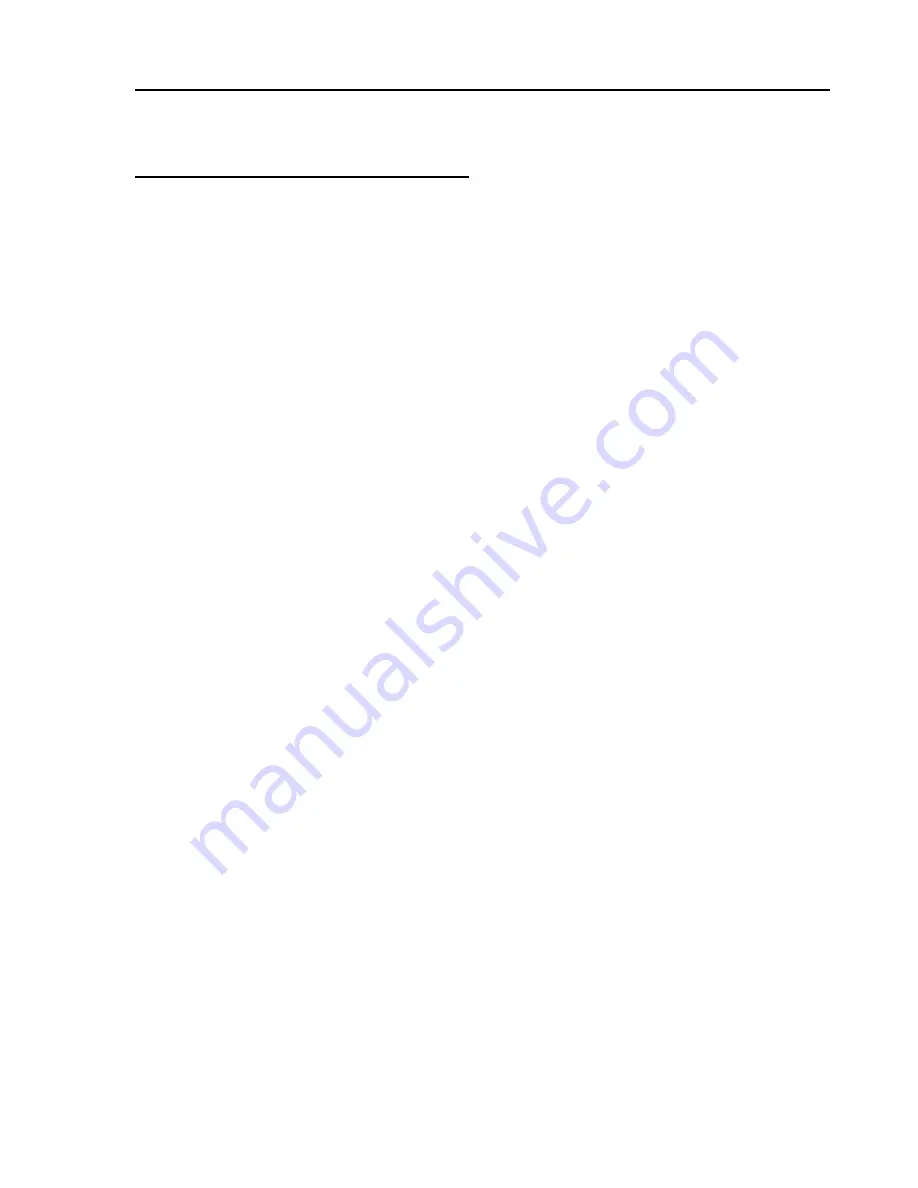
VANNER
Incorporated
OWNER’S MANUAL
Vanner High Voltage Distribution Module OWNER’S MANUAL
11
Operation
Distribution Module Start Up/Normal Operation
The following outlines the sequence of events that permit contact closure to power loads connected
to Channels 1 and 2 under normal conditions;
Standby Mode
1. HVDM is in "Standby" mode while aw24V and ignition inputs from vehicle.
Controller Power Up
2. After receiving an ignition signal and +24V inputs, the HVDM controller will power up and
perform a low voltage self test.
Note: the low voltage must be between 18 - 32VDC.
Ready State
3. After successful completion of power up and low voltage self test, the HVDM will enter a
"Ready" state.
4. After entering the "Ready" state, the HVDM will wait for a hardware enable command, active
low, from the TCM.
5. After receiving the hardware enable signal, the HVDM will perform a high voltage self test.
Note: the high voltage must be between 400 - 800VDC.
6. After successfully completing the high voltage self test, the HVDM will wait for a CAN
message from the hybrid controller to proceed with pre-charging the connected load(s).
Contact Closure
7. Upon successful completion of pre-charging the load(s), contact closure will occur. The
load(s) are now connected to the high voltage battery/traction system.
The HVDM is designed to pre-charge a maximum capacitive load of 6,800µF in 2.5S.
8. After contact closure, the HVDM enters a "Contactor Closed" state.
Contact Opening
9. The contactors are opened via CAN message or removal of the hardware enable signal.
10. The passive discharge board will discharge the capacitive load(s) after contactor opening.