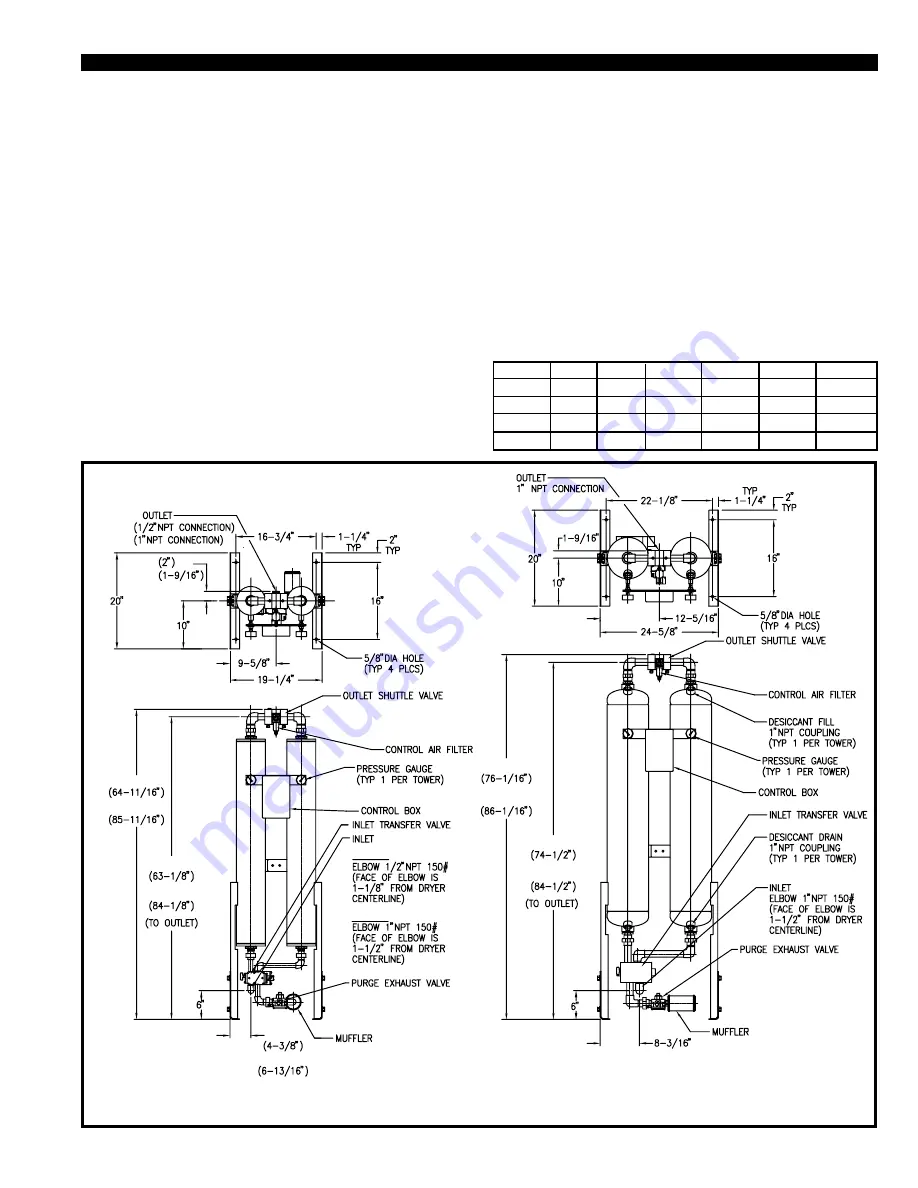
PRINTED IN THE U.S.A.
PAGE 3
DIMENSIONS AND SPECIFICATIONS
SECTION 3
3.1 DRYER SPECIFICATIONS
WEIGHT
(with desiccant installed)
HLS-55 ....
230 lbs
HLS-80....
280 lbs
HLS-120....
385 lbs
HLS-150....
445 lbs
DIMENSIONS
See SECTION 3.2
IN/OUT CONNECTION
HLS-55....
1/2"NPT
HLS-80....
1"NPT
HLS-120....
1" NPT
HLS-150....
1"NPT
VESSELS (desiccant towers)
Design Pressure ............ 150 PSIG
Design Temperature ...... -20
O
F TO 200
O
F
PIPING
Threaded pipe fittings: ANSI B16.3
Threaded union fittings: ANSI B16.39
Pipe: Carbon Steel, Schedule 40
VALVES
Inlet ............... 4-Way, solenoid piloted
Outlet ............. Shuttle valve
Purge .............. 3-Way Valve (run as a 2-Way Valve), solenoid piloted
CONTROL AIR FILTER
Construction
...
Zinc housing
3.2 DIMENSIONS Models HLS-55 through HLS-150
HLS-55 & HLS-80
HLS-120 & HLS-150
ELECTRICAL
Nema 4 Electrical enclosure
Standard 115V ...... 115V/1PH/50-60Hz
Optional 230V: ....... 230V/1PH/50-60Hz
DESICCANT
Material .............. Activated Alumina, 1/8" (2-5 MM) Bead type
Quantity Per Tower (LBS)
HLS-55....
30.5 lbs
HLS-80....
43.5 lbs
HLS-120....
67.5 lbs
HLS-150....
82.5 lbs
OPERATING CONDITIONS
Inlet Air Pressure ............... MIN 60 PSIG ......... MAX 150 PSIG
Inlet Air Temperature ......... MIN 40
O
F ............... MAX 120
O
F
Ambient Air Temperature .. MIN 40
O
F ............... MAX 120
O
F
RATED INLET CONDITIONS
Inlet Air Pressure ................................ 100 PSIG
Inlet Air Temperature .......................... 100
O
F
Relative Humidity (saturation) ............ 100% RH
* (ROTATED TO BACK ON HLS-150)
HLS-55
HLS-80
HLS-55
HLS-80
HLS-55
HLS-80
HLS-55
HLS-80
HLS-80
HLS-55
HLS-55
HLS-80
HLS-120
HLS-150
HLS-120
HLS-150
FLOW CAPACITIES (SCFM) at various pressures (100
0
F)
60
PSIG
75
PSIG
90
PSIG
100
PSIG
125
PSIG
150
PSIG
HLS-55
36
43
50
55
61
66
HLS-80
52
63
73
80
88
96
HLS-120
78
94
110
120
132
144
HLS-150
98 117 137 150
166
180