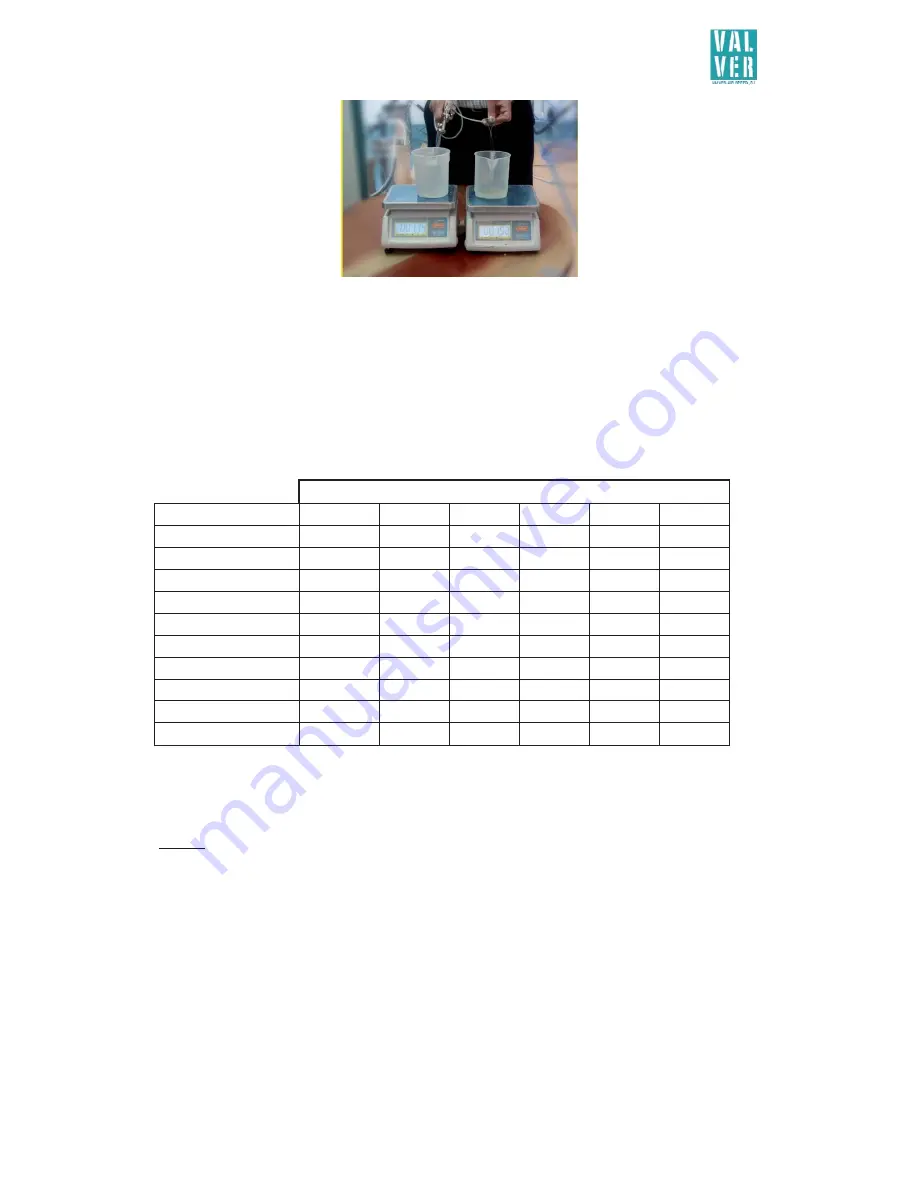
INSTRUCTIONS MANUAL
AIRBRUSH MANUAL EXTERNAL MIX EQUIPMENT
13
10. After that press the
gun trigger (18)
and fill the measuring cylinders up to the
desired quantity.
11. Check the volume proportion or the material weight with a balance and adjust
the proportion with the
catalyser pump air control (10)
at the pressure tank or
with the
catalyser regulator (24)
of the pistol. In case of two-component-
products application with a small mix ratio the machine is equipped with a
micrometric valve (21).
To adjust the mixture proportions directly with the
micrometric valve, please follow the guidance table and the advices:
PRESSUREINLETPRESSURETANK
VALVEROTATIONS
0,5
0,6
0,7
0,8
0,9
1
1
0
0
0
0
0
0
2
2,1
2,6
3,4
3,7
4,7
5,2
3
5,4
6,2
7,3
8,1
9,1
10
4
8,2
9,9
11,3
12,9
14,3
15,6
5
12,1
13,5
15,4
15,9
17,1
17,8
6
16,4
18,6
21,9
23,1
25,4
26,7
7
20,8
24,8
28,7
30,4
32
33,2
8
25,7
30,2
34
36,6
39,2
42,4
9
33,6
40,2
44,7
46,9
50,1
53,8
10
48,7
54,4
59,7
64,2
69,6
72,6
This table facilitates and orientates only for the start-up procedure. Attention! It is neither an
orientation nor an exact formula, because these flows always may vary depending on viscosities, hose
length and material losses.
Advices: After finishing step 6 and achieving the required quantity of
component A
it will be
proceeded to the final calibration of the catalyst or
component B.
Therefore the flow per minute of the component A has to be controlled by a balance removing the
spray air from the pistol.
When we know the resin flow per minute selected by the user, for example 150g/min, we
have to multiply this with the catalyst or component B mix percentage expressed by the application
product manufacturer, for example 5% means 150 x 0.05 = 8g/min. Looking to the table we have two
consistent adjustment options.
Option 1
. Feeding the pressure tank with the
catalyser air pump control (10
) with 0.5 bar and
turning the knob of the
micrometric valve (21)
4 times starting at 0
Opción 2
. . Feeding the pressure tank with the
catalyser air pump control (10
) with 0.8 bar and
turning the knob of the
micrometric valve (21)
3 times starting at 0
If we aim for option 2 we get the more balanced valve regulation option, where the catalyst
pressure is closer to the resin pressure.
Summary of Contents for AIRBRUSH MANUAL EXTERNAL MIX EQUIPMENT
Page 1: ......
Page 22: ...INSTRUCTIONS MANUAL AIRBRUSH MANUAL EXTERNAL MIX EQUIPMENT 21 APPLICATION GUN EXPLODED...
Page 23: ...INSTRUCTIONS MANUAL AIRBRUSH MANUAL EXTERNAL MIX EQUIPMENT 22...
Page 24: ...INSTRUCTIONS MANUAL AIRBRUSH MANUAL EXTERNAL MIX EQUIPMENT 23...
Page 25: ...INSTRUCTIONS MANUAL AIRBRUSH MANUAL EXTERNAL MIX EQUIPMENT 24...