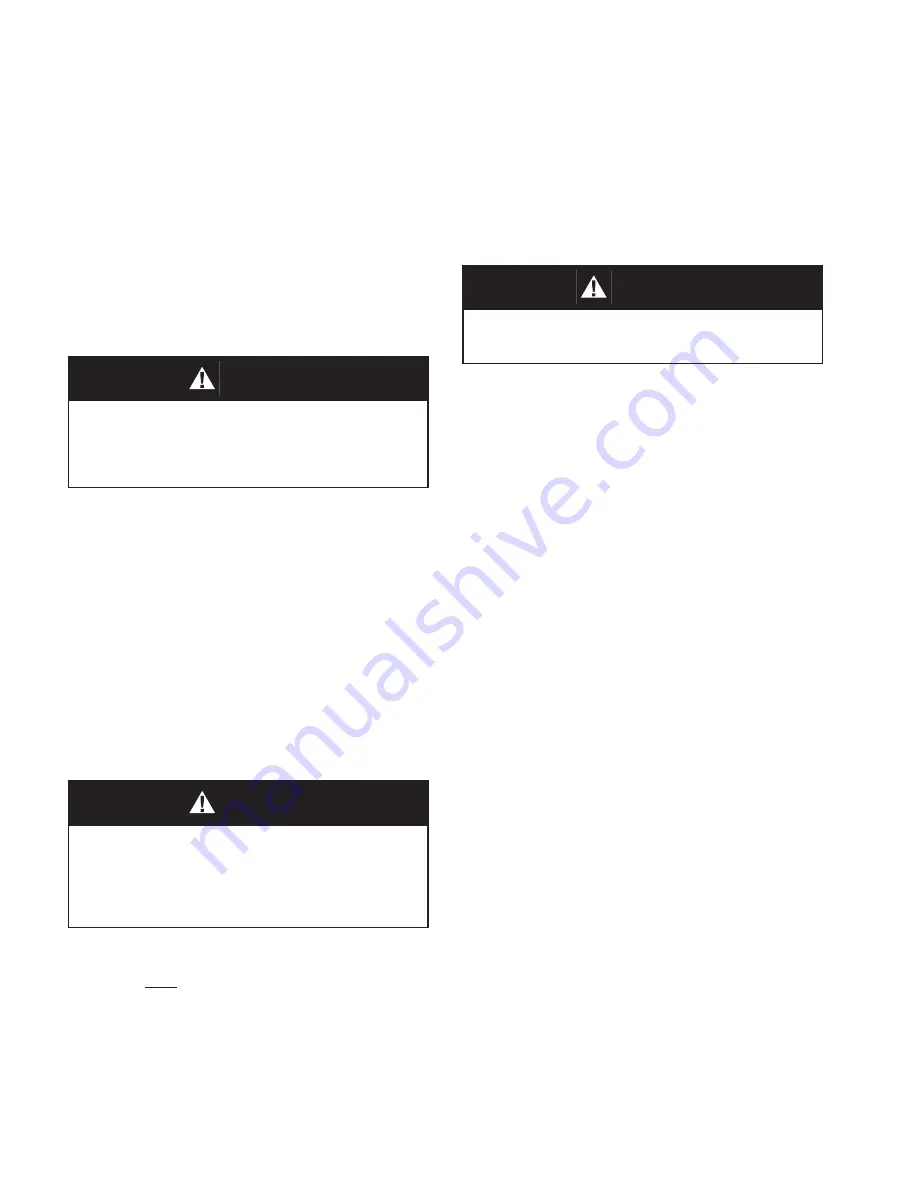
2
IOM-3600
CAUTION
DO NOT attempt to remove the vent from the tank
or process vessel without first bleeding all pressure
from the system. ALTERNATIVE MEANS OF VACUUM
RELIEF MUST BE PROVIDED WHEN THE VENT IS OUT
OF SERVICE.
III. INSPECTION AND STORAGE
The vacuum relief vent is carefully packaged to
prevent damage or contamination during shipping.
Inspect the equipment when it is received and report
any damage to the carrier immediately. The vent
should be stored with all the protective flange covers
CAUTION
DO NOT change vacuum setpoint by adding additional
weights to the pallet assembly without consulting
Cashco Inc. or your VCI representative.
The 3000 Series Vents are designed to mate to a
flange. Torque guidelines are provided in Table 1. The
Vents are
NOT
rated for full flange pressure and do
not require high bolting torque.
Before installing any 3000 Series Vent, remove all
packing materials from inside and outside the vent. If
loading weights were shipped separate from the vent,
make sure to install the weights. Tighten cover dome
cap screws to 15 ft.-lbs.
WARNING
The vent must be installed in a vertical position as
shown in Figure 1. The tank nozzle on which the vent
is mounted should have the same nominal diameter
as the venting device. It is recommended that the tank
nozzle flange face be within 1 degree of horizontal for
best performance of the venting device.
II. SAFETY WARNINGS
Tank or system protection is the primary function of
the weight loaded Vacuum Relief Vent. It must be
selected to meet the total pressure and vacuum flow
requirements within the Maximum Allowable Working
Pressure and Vacuum of the system on which it
is installed. Consult API Standard 2000 for tank
protection sizing procedures. Improperly specified
relief vents may result in structural damage to the
tank or system and can cause severe personal injury
or death.
When Pipe-Away relief vents are used, back
pressure in the header system will affect the set point
of weight loaded vents by the amount of the header
pressure. Maximum possible header pressure must
be considered when sizing the pressure relief vent.
SECTION II
SECTION III
in place. Make sure that any loading weights that
might have been shipped separately, to protect the
vent during shipping, are accounted for and stored
with the vent. These weights, when required, will be
installed during installation. See Section IV.
SECTION IV
IV. INSTALLATION
NOTE:
Wipe down the Seat Ring and Diaphragm
when all the packing materials have been removed.
Inspect the gasket seating surface of the tank nozzle
flange. It must be clean, free of scratches, corrosion,
tool marks and flat.
FRP and Aluminum vents are furnished with flat
faced flanges. It is recommended that they be
installed on mating flat face flanges with a full faced
gasket. If the flat face of the vent is sealing against
a raised face steel flange, a spacer or filler ring must
be used to fill the annular space of the raised face
steel flange.
Make sure the gasket is suitable for the application.