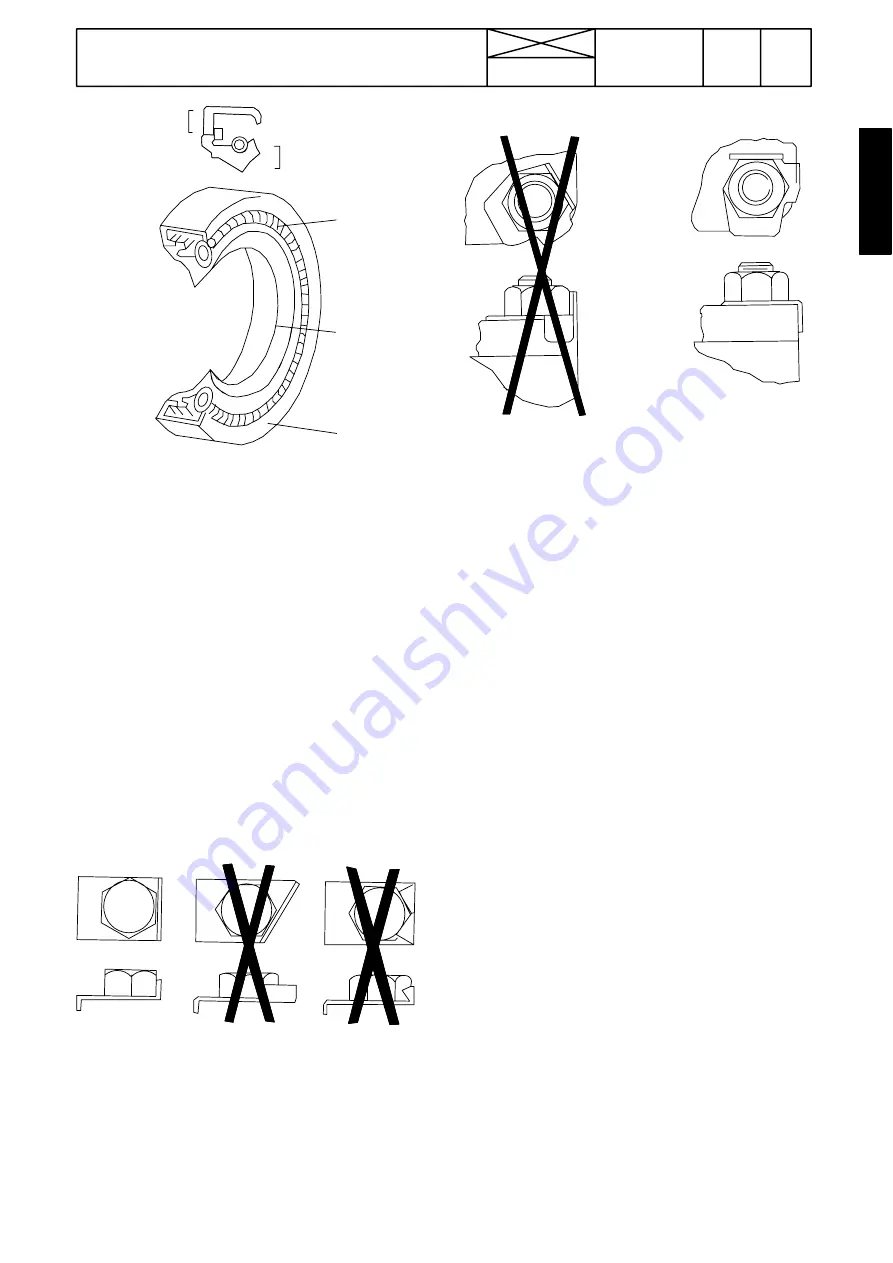
13
Model
Code
Page
12. Repairs
1. 11. 2000
120
3
95, 105, 115
X100-X120
É
É
ÇÇÇÇ
ÇÇÇÇ
ÉÉÉÉ
ÉÉÉÉ
ÉÉÉÉ
4
5
3
2
1
The main parts of lip-type seal:
1. Case
2. Sealing element
3. Ring spring
The figure above shows the construction of a simple lip-type
seal. The cross section shows the heel (4) and the toe (5),
used to identify the sides of a single element seal. With a few
exceptions, the toe of a single-lip is located on the lubricant
side. Some seals have a second auxiliary lip which has no
spring.
Cables and wires
When removing or disconnecting a group of cables or wires,
label each one to ensure correct refitment.
Locking devices
Correct and incorrect use of retainers
Correct and incorrect method of fitting and bending locking
tabs.
Slackening of nuts and bolts is prevented by mechanical
means such as lockwashers, tab washers and cotter pins, or
by Loctite-type locking agents.
Flat retainers must be installed properly to be effective. Bend
one end of the retainer against the edge of the part. Bend the
other end against one of the nut or bolt head.Always fit new
retainers in compartments which house moving parts. When
fitting lockwashers on aluminium housings, place a flat
washer between the lockwasher and the housing.
Note!
1) Never fit a lockwasher (Grower, fan, spring, etc.) under a nut
or bolt to which a specified torque has to be applied.
2) Always thoroughly degrease components before applying
Loctite type locking agents.
Bushes and press fits
Do not fit bushes with a hammer alone. Use a suitable fitting
tool and a hammer or, better still, a press if possible..
When using a press, ensure that pressure is applied directly
in line with the bore. If the ring has an oil hole, take care to align
it with the oil hole in the mating part. When press fitting a part
into another part, lubricate the mating surfaces. Tapered parts
should be assembled dry. Before assembly, check that the
tapers are dry and free from burrs.
Fitting bolts in blind holes
Use bolts of the correct length. A bolt which is too long may
"bottom" before the head comes into contact with the part it
is to hold: this will cause damage to the threads. If a bolt is too
short, there may not be enough threads engaged to hold the
part securely.
Summary of Contents for 95
Page 2: ...Order no 39 214 211 ENGLISH Find manuals at https best manuals com...
Page 3: ...10 General 11 Layout 12 Repairs 13 Maintenance Find manuals at https best manuals com...
Page 4: ...2 Find manuals at https best manuals com...
Page 6: ...4 Find manuals at https best manuals com...
Page 8: ...6 Find manuals at https best manuals com...
Page 18: ...16...
Page 24: ...22...
Page 25: ...20 Engine 21 Engine 22 Fuel system 23 Cooling system 21...
Page 26: ...22...
Page 41: ...This as a preview PDF file from best manuals com Download full PDF manual at best manuals com...