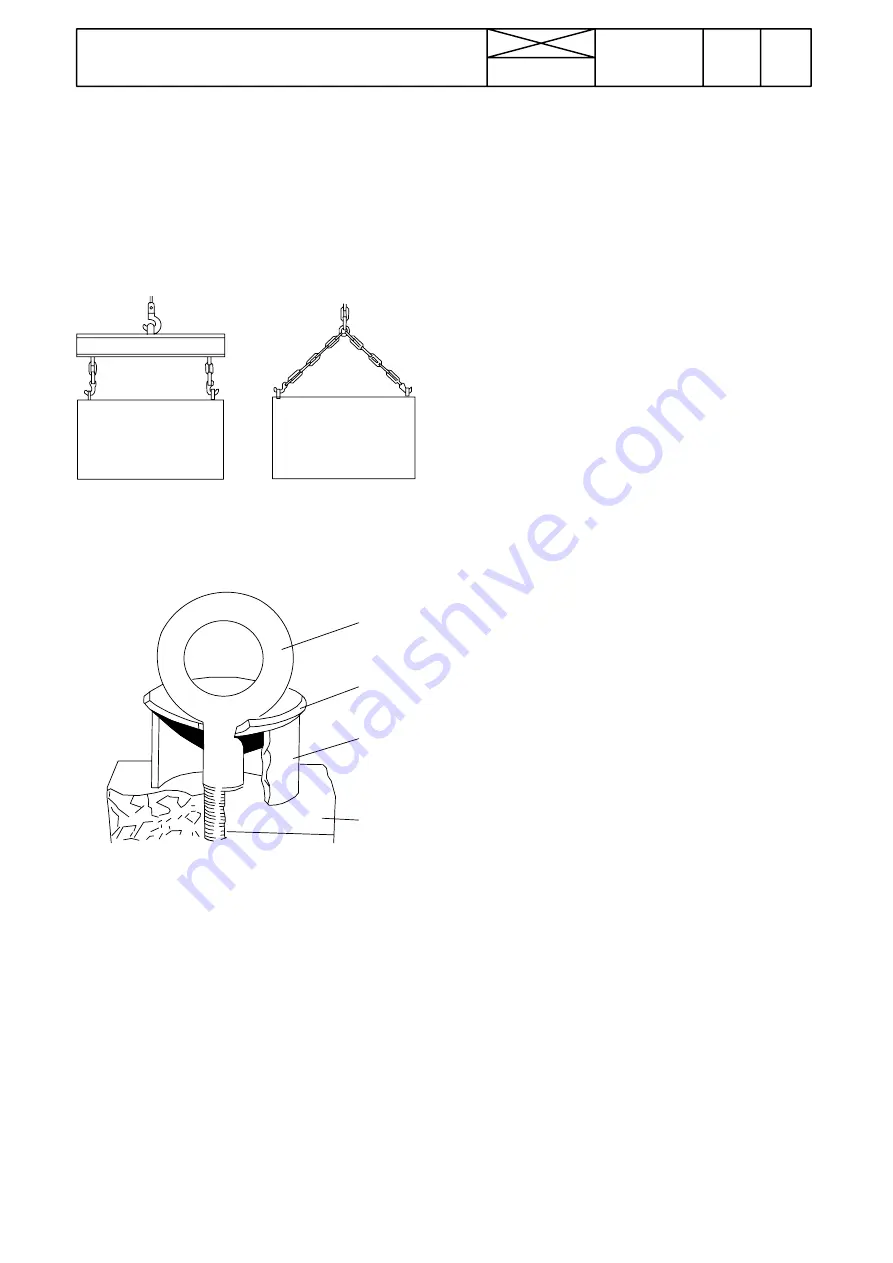
12
Model
Code
Page
12. Repairs
1. 11. 2000
120
2
95, 105, 115
X100-X120
Handling of heavy components
Unless otherwise specified, all removals should be accomĆ
plished using adjustable lifting equipment. All supporting
slings must be parallel to each other and as near vertical as
possible in relation to the object being lifted. However, where
slings are of a far greater capacity than the weight of the load
to be fitted, a triangular lifting arrangement may be used.
Oikein
Rätt
Right
Richtig
Giusto
Väärin
Fel
Wrong
Falsch
Sbagliato
Correct
Teisingai
Mauvais
NeteiĆ
singai
When removing a component at an angle, remember that the
capacity of an eyebolt is reduced when the angle between the
supporting members and the object becomes less than 90°.
B
C
D
A
Forged eyebolt support
A. Load
B. Lifting shackle
C. Shackle retaining plate ( 3 mm thick)
D. Sleeve
When necessary the forged eyebolt can be supported in the
way shown in figure above. Sleeve D may or may not be
welded to plate.
Warning!
If a part resists removal, check that all nuts and bolts
have been removed and that there is no interference from adĆ
jacent parts.
Cleanliness
To ensure long life of a machine, it is important to keep dirt and
foreign material out of its vital working components. PrecauĆ
tions must be taken to safeguard against this. Enclosed comĆ
partments, seals and filters have been provided to keep the
supply of air, fuel and lubricant clean. These protective deĆ
vices must not be removed.
Whenever hydraulic, fuel, lubricating oil or lines are disconĆ
nected, clean the point of disconnection and the surrounding
area. As soon as a line has been disconnected, cap, plug or
tape the line or opening to prevent the ingress of foreign maĆ
terial.
The same cleaning and covering precautions should be taken
when access covers or inspection plates are removed.
Clean and inspect all parts. Make sure that all passages and
holes are clear. Cover all parts to keep them clean. Make sure
parts are clean when they are reassembled. Leave new parts
in their wrapping until they are actually needed for reassembly
Assembly
When reassembling a machine, complete each step in seĆ
quence. never partially assemble one part then start to asĆ
semble another. Make all recommended adjustments. AlĆ
ways check the job on completion to ensure that nothing has
been overlooked. Recheck the various adjustments before
putting the machine back into service.
Note!
Before fitting new parts, remove rust preventative comĆ
pound from all machined surfaces (usually "peel-off subĆ
stances).
Lubrication
Where applicable, fill the compartments of repaired or reĆ
newed components with the quantity, type and grade of clean
lubricant recommended in the routine maintenance section of
the Operator's Manual.
Shims
When shims are removed, tie them together and identify their
location. Keep shims clean and take care not to bend them
before refitting them.
Gaskets
Make sure that the holes in gaskets line up with lubricating oil
passages in the mating parts. If gaskets have to be made, use
material of the correct type and thickness. Make sure that
holes are punched in the right places.
Incorrectly punched gaskets can cause serious damage.
Lip type rubber seals
Lubricate the lips of lip-type rubber seals with oil before fitĆ
ment. Do not use grease on seals, except for grease seals.
Summary of Contents for 95
Page 2: ...Order no 39 214 211 ENGLISH Find manuals at https best manuals com...
Page 3: ...10 General 11 Layout 12 Repairs 13 Maintenance Find manuals at https best manuals com...
Page 4: ...2 Find manuals at https best manuals com...
Page 6: ...4 Find manuals at https best manuals com...
Page 8: ...6 Find manuals at https best manuals com...
Page 18: ...16...
Page 24: ...22...
Page 25: ...20 Engine 21 Engine 22 Fuel system 23 Cooling system 21...
Page 26: ...22...
Page 41: ...This as a preview PDF file from best manuals com Download full PDF manual at best manuals com...