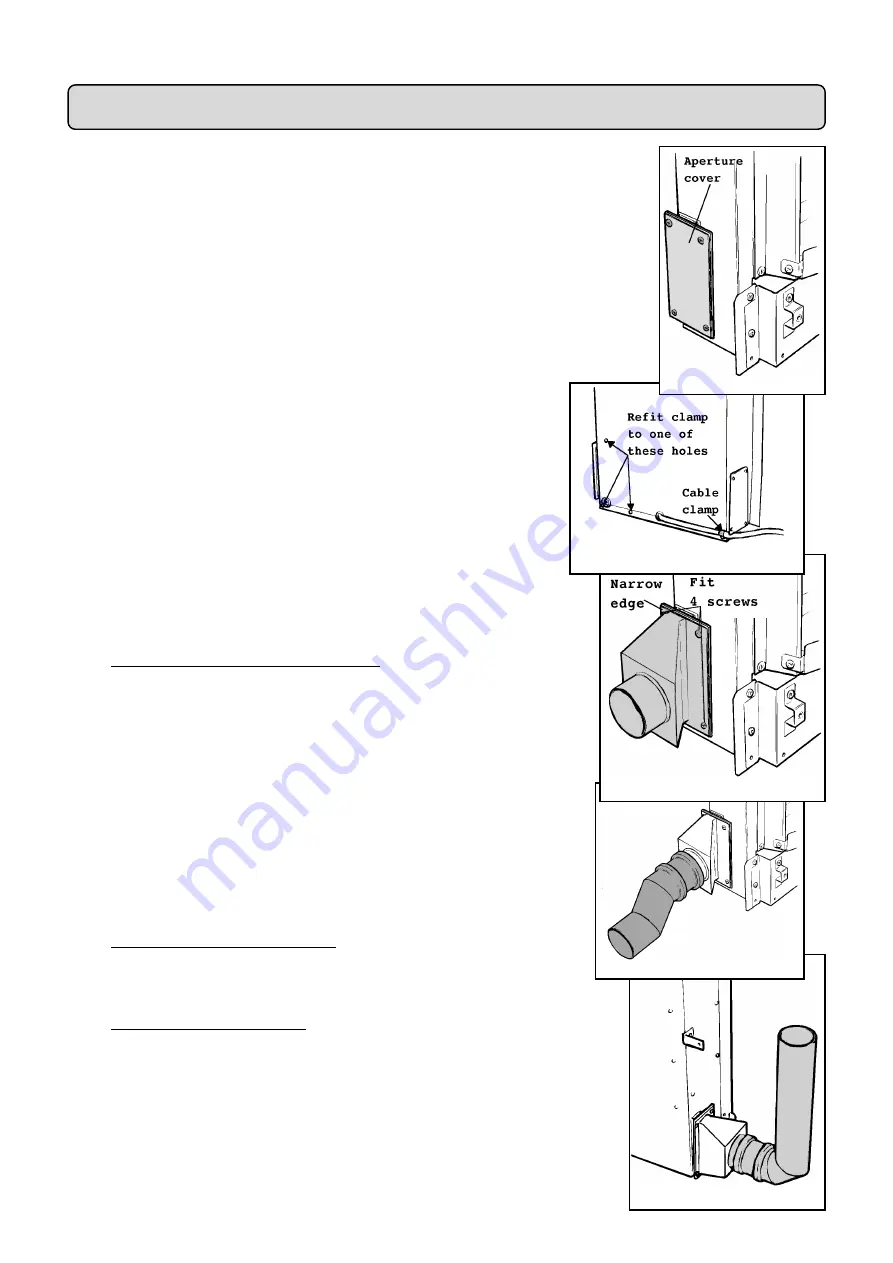
13
6.1
If the gas supply pipe is to enter through the concealed rear opening,
pierce the grommet. If the supply pipe is sleeved, trim the sleeve back where it
enters the appliance and seal the sleeve to the pipe.
If the supply pipe is to run from the side of the appliance and enter through the
concealed rear opening, the wall will usually have to be chased to accommodate
the pipe at the back of the heater.
6.2
An installation template is supplied which includes a diagram for forming
the pipe so that it avoids various components below the burner.
6.3
This appliance is designed for installation with a 114mm. (4.5in.) deep
fire surround or false chimney breast. For horizontal duct installations
the skirting board will have to be removed from behind the hearth and
along the total length of the flue duct run. If the skirting is not removed
the depth of the fire surround will need to be increased accordingly.
6.4
Place the hearth in its proper location. Place the appliance on the
hearth in its proper location. Mark the position of the wall fixing
brackets.
Note: If a surround deeper than 114mm is to be installed, spacers will
be needed behind the wall mounting brackets.
6.5
Remove the appliance. Drill holes at the marked positions using a
no.10 drill and plug.
6.6
For duct connection from the right side:
6.6.1
Remove the flue aperture cover and gasket and fit them to the left side
(see figure 11). Be careful not to damage the gasket.
6.6.2
Remove the fan cable clamp from the rear left of the convection box.
Replace the screw thus removed into the convection box. Clamp the cable
at one of the screws at the right side of the box (see figure 12).
6.7
Fit the flue duct connector to the open side of the convection box
with four tapping screws. The narrow edge of the connecting plate must be
at the back (see figure 13).
6.8
Place the appliance back in position. Secure it to the wall through the
two side brackets using two woodscrews provided.
6.9
For horizontal duct installations: Fit the “Z” shaped duct coupling to
the duct connector pushing firmly to ensure a good seal. Rotate the
coupling so that its open end is as low as possible (see figure 14).
6.10
For vertical duct installations: Fit an elbow bend duct to the duct
connector pushing firmly to ensure a good seal. (see figure 15).
6.11
Mark the wall at the centre line of the flue duct (54mm above the hearth
for horizontal installations, 200mm from the side of the convection box for
vertical installations). Draw a line at this position along the wall from the heater
to where the fan box hole will be drilled.
P A R T 6 :
G A S S U P P L Y & F L U E S I T I N G
Figure 15
Figure 14
Figure 13
Figure 12
Figure 11