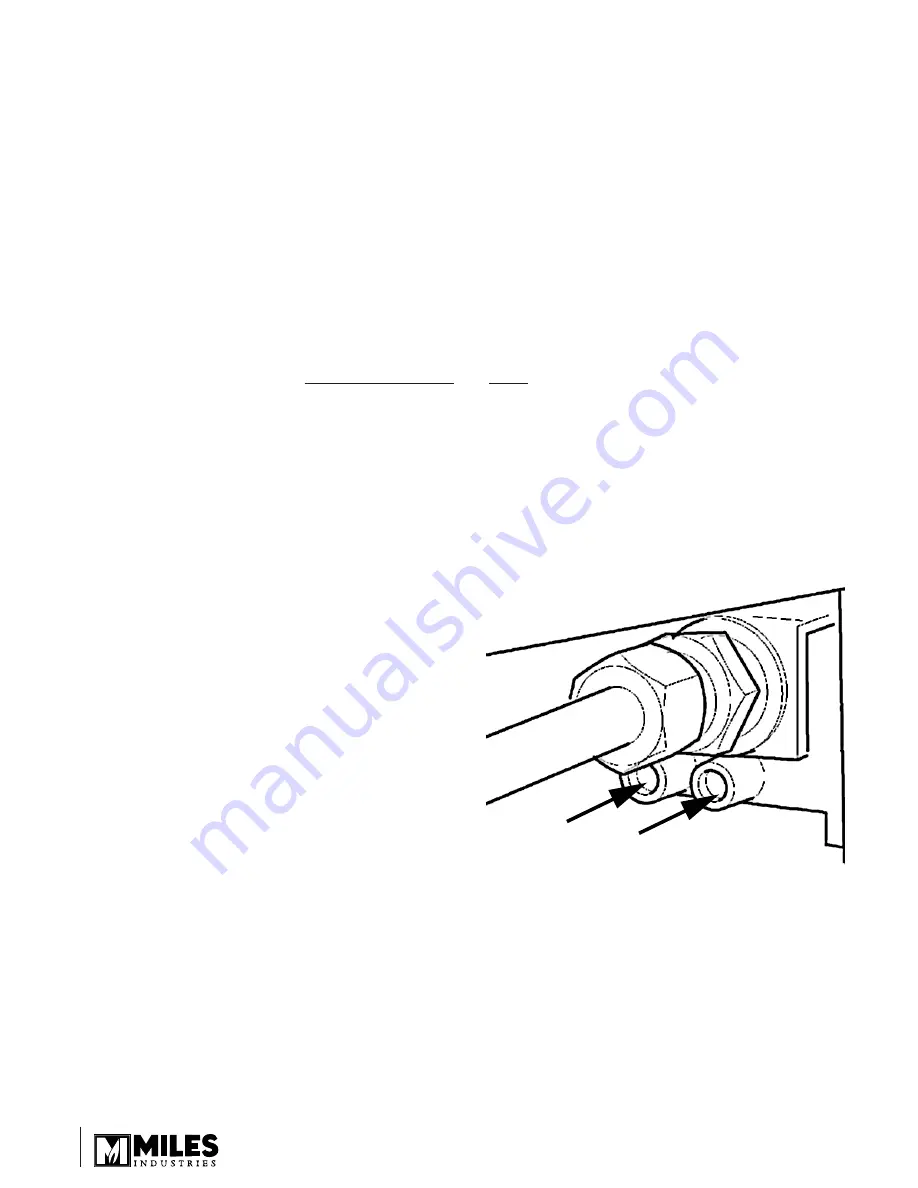
20
20
Gas Supply Installation
• It’s preferable to rough-in the gas line at this point before proceeding with the
fi
rebox installation.
• The appliance is supplied for supply gas connection at the control valve. Supply line connection to the control
valve of the appliance is 3/8 inch NPT (female).
Take care not to apply torque to the valve. An isolating valve may be
fi
tted within the appliance case. Be aware
that the supply pipe should follow routing to clear the remote receiver or optional fan.
• Use only new black iron or steel pipes or copper tubing if acceptable—check local codes.
Note that in USA,
copper tubing must be internally tinned for protection against sulfur compounds.
• Unions in gas lines should be of ground joint type.
• The gas supply line must be sized and installed to provide a supply of gas suf
fi
cient to meet the maximum
demand of the appliance without undue loss of pressure.
• Sealant used must be resistant to the action of all gas constituents including LP gas. Sealant should be applied
lightly to male threads to ensure excess sealant does not enter gas lines.
• The supply line should include a manual shut-off valve and union to allow the appliance to be disconnected for
servicing.
• Pressure test the supply line for leaks.
• The appliance and its individual shut-off valve must be disconnected from the gas supply piping system
during any pressure testing of that system at test pressures in excess of 1/2 psig (3.5kPa).
• The appliance must be isolated from the gas supply piping system by closing its individual manual shut-
off valve during any pressure testing of the gas supply piping system at test pressures equal to or less
than 1/2 psig (3.5kPa).
• Failure to either disconnect or isolate the appliance during pressure testing may result in regulator or valve
damage. Consult your dealer in this case.
• The minimum supply pressure is given in
Speci
fi
cations
section of this manual.
• All piping and connections must be tested for leaks after
installation or servicing. All leaks must be corrected
immediately.
• When testing for leaks:
• Make sure that the appliance is turned off.
• Open the manual shut-off valve.
• Test for leaks by applying a liquid detergent or soap
solution to all joints. Bubbles forming indicate a gas
leak.
Never use an open fl ame to check for leaks
.
• Correct any leak detected immediately.
• The pressure test tapping locations are shown in
fi
gure
above. A built-in non-adjustable regulator controls the
burner manifold pressure. The correct pressure range
is shown in the table in the
Speci
fi
cations
section of
this manual. The pressure check should be made with the burner alight and at its highest setting. See
Lighting
Instructions
section for full operating details.
Supply
pressure
test tapping
Manifold
pressure
test tapping