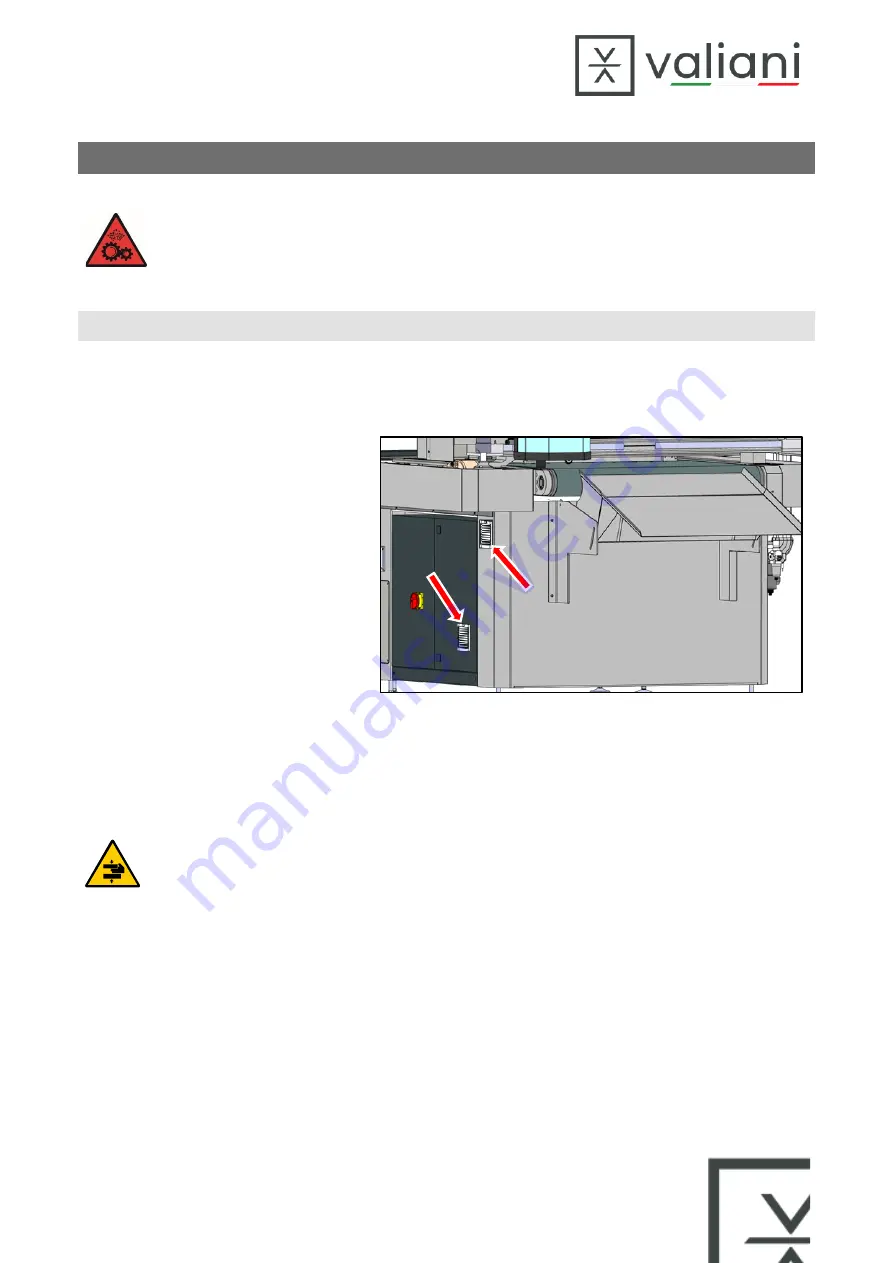
OMNIA
50
8
ROUTINE MAINTENANCE
Very little maintenance is required, and it is limited to the operations detailed in the following paragraphs.
CAUTION! Please disconnect the machine from the
electrical
mains supply, before carrying out any
maintenance operations
8.1
CLEANING
One of the most important maintenance tasks is the frequent and complete cleaning of the following parts:
Worktable (daily)
•
Clean the top of the work table everyday with compressed air or with a soft and dry brush.
Electrical panel fan and the base (every week)
•
Switch off the machine.
•
Remove the air filter cover using a
screwdriver
•
Blow the fan and the air filter with
compressed air.
•
Reinsert the filter inside the cover and
fit it into the seat under the fan.
Cutting head (Everyday)
•
Clean the cutting head using compressed air or with a soft dry cloth to remove dust and any debris left from
production.
•
Check for, and remove, any dirt on the blade protection holder.
DANGER!
Before cleaning the cutting tools remove the blade to avoid any accidental injury.
Vacuum pump cleaning.
Before carrying out any operation, switch off the machine and disconnect it from the mains power supply. Follow the
instructions provided with the pump documentation. To access the pump, remove the machine protection panel
(Figure 5-22).
Figure 8-1
Summary of Contents for OMNIA
Page 1: ...OMNIA Instruction and Maintenance Manual...
Page 2: ......
Page 65: ......
Page 66: ...002695 rev 02...